Built For
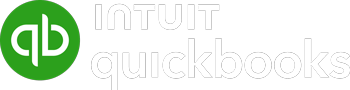
Hobbs Iron & Metal
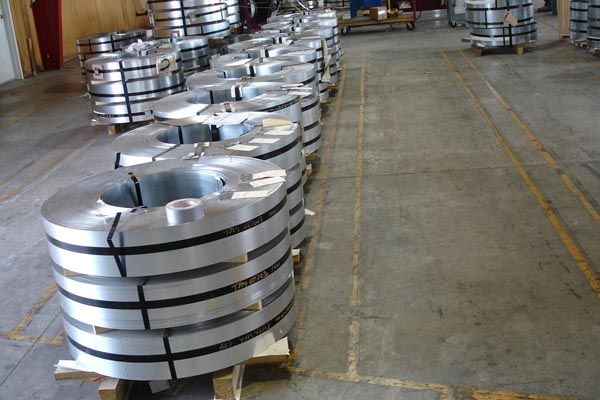
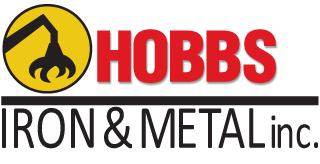
Hobbs Iron & Metal has withstood the test of time – just like the products they sell.
Many decades later, Owner Gene Day still applies the valuable lessons and principles learned from his business mentor.
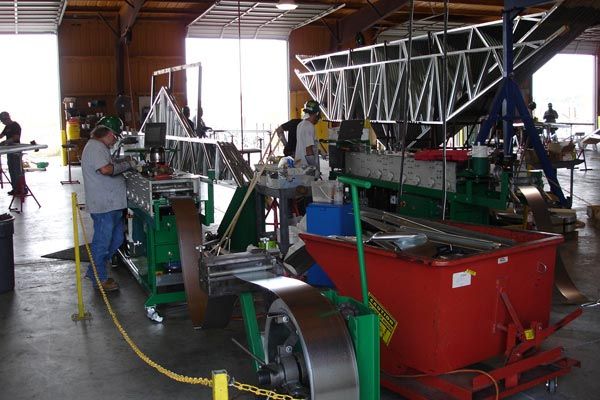
“Years ago, Mr. Bobby Jarvis had a steel company in Lubbock, Texas and when I went to work for him in 1976, he trained me and I started learning about the business. When we acquired Hobbs Iron & Metal in 1978, we wanted to integrate with the retail portion of the business, so we brought new steel to that company and started retailing and wholesaling.”
Day eventually took over ownership of the business, which has now grown to five locations — including their 70,000 square foot warehouse at their main location — and has since added metal building and metal building components to the products they offer.
Hobbs Iron & Metal is committed to providing environmental responsibility and sustainability by applying the best environmental practices possible and continuously looking for ways to innovate the industry of non-renewable resources.
But what’s the foundation of success for Hobbs Iron & Metal?
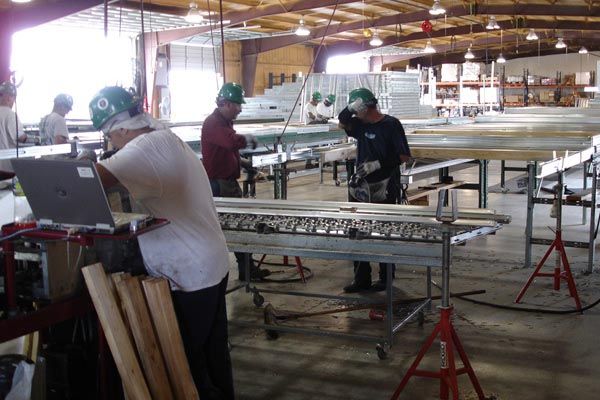
“Our employees. God has blessed us with a lot of really good people who want to grow, care about other people, and care about doing a good job. One or two people can’t create a business like this – it takes a whole bunch of people and that’s definitely been what we attribute our success to,” said Day.
Any time you grow, it’s challenging both on the finances and on the logistics. Growth is not without challenges – the two go hand-in-hand, I believe.”
Gene Day, Owner
Hobbs Iron & Metal’s prior system was unable to correctly account for the different units of measure they were using – which in turn was taking a toll on their sales.
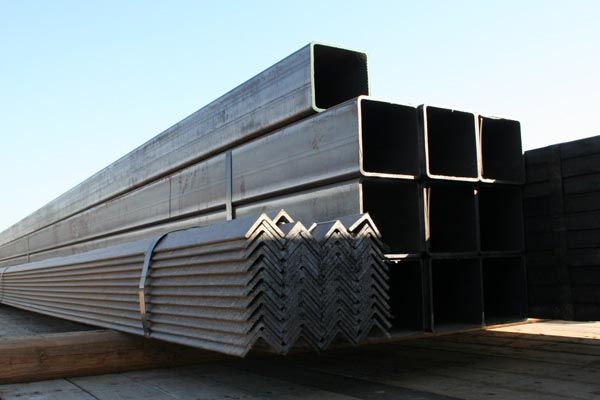
“We sell by the piece, by the foot, by the square foot, or by the weight. Our old program was not calculating the different types of material that we were selling in different units. When we would look at the inventory, it would throw us a negative number or the number wasn’t an actual true on-hand number when we were selling our materials.
It was very challenging because it would frustrate the customer when we would send them out to the yard and either the product wasn’t there or what they wanted was there but our system wasn’t letting us see it. It was a matter of going back and forth between the office and the yard. It was frustrating and time-consuming for us and our customers,” said Yolanda Aranda, Accounting Supervisor, Hobbs Iron & Metal.
She explained the manual efforts needed to try to correct inventory discrepancies…
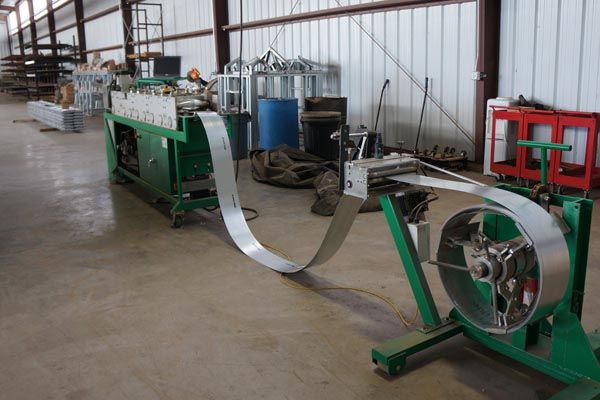
“We were having to make a lot of adjustments and we were having to do an inventory check at least every month – sometimes weekly, especially our stuff that was figured by the pound. To do inventory of our yard, it takes us a whole weekend, starting on a Friday morning till Saturday night or Sunday morning. Being that we couldn’t do that every weekend or once a month, we would take a part of the yard and we would just inventory random stuff one weekend to try to get the right numbers and the following month, we would just focus on the stuff by the foot, etc.”
Hobbs Iron & Metal needed a solution for their growing business so Gene Day began his search by asking others in the steel industry.
“What I found was most of the larger steel companies that could afford it had gone in and had programmers write their own software. It was a very expensive proposition and it was a proposition that was met with mixed results – some of those people had spent a tremendous amount of money and received programs that weren’t functional,” said Day.
However, Hobbs Iron & Metal was able to find a cost-effective solution that was fully capable of the sophisticated inventory features that they needed – Acctivate.
We really needed the features that Acctivate offered and it completed the cycle for us and helped us grow,” said Day.
Aranda added…
Looking at any other inventory solution against Acctivate, Acctivate was able to do our inventory the way we needed it.
Acctivate has been very beneficial for our company – it has been able to make our jobs easier and it’s worked great for us.”
Sturdy, sophisticated system – yet extremely simple to use
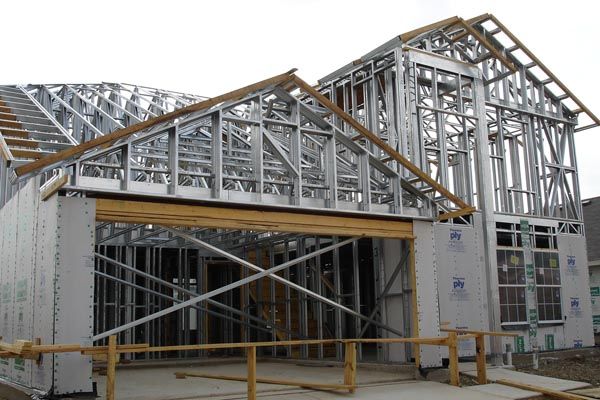
It was very easy to learn and use Acctivate. Acctivate has a lot of tutorials on their Help Site that we use every time we hire someone new – we sit them down one day for training and we let them go through the tutorials on invoicing, making quotes, releasing payments, etc.
Yolanda Aranda, Accounting Supervisor
We also get Acctivate’s newsletter to see when there are going to be certain tutorials or new features. Sandy with Accounts Receivable, and I get them every month and she will go through and look for new features or new tutorials where we can improve our invoicing or learn a quicker or simpler way to do inventory. We’ll select the people who need to learn it or that it affects and we’ll do the tutorials.”
Although it is easy to use, Acctivate is an extremely robust and sturdy solution.
Real time inventory for multiple locations
Acctivate’s powerful system easily supports multiple users — including Hobbs Iron & Metal’s 37 users who are split across their five locations — to provide synchronicity and real-time data.
It’s been great to have multiple users be able to access Acctivate in real-time. Because Hobbs Iron & Metal is our main office, our other offices are linked in to our server and they’re able to look at our real-time inventory so it has benefited us greatly to have multiple users like that.”
Yolanda Aranda, Accounting Supervisor
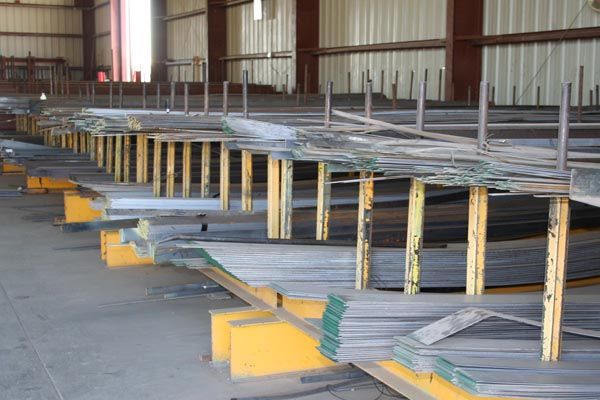
Inventory Control
Acctivate’s user interface easily navigates users through information – simplifying workflow and streamlining the search process.
For me, the handy thing is you can look information up different ways. Also, if the information is in Acctivate, you can’t lose it if it’s ever been saved. You can find it by going to the part number and it’s easy to track all the information that’s ever affected that one part number.
Sandy Nash, Accounts Receivable
My favorite feature is that you can double-click in the fields and you can find anything in Acctivate from the part number – adjustments, assemblies, sales, adjustments, receipts, the payments, anything like that. You can find everything you need to know about that part number.”
Acctivate offers tremendous flexibility with the availability of costing methods including Average, Standard, LIFO, FIFO and Actual.
Acctivate’s costing features have been very beneficial because it lets us know more closely where we stand on the costing of our inventory and the true cost of it from an accounting perspective.
Gene Day, Owner
We were initially attracted to Acctivate because of the costing flexibility – we don’t use multiple types of costing but we have made one change over the years. Prior to Acctivate, we did it through our accounting system but we had a few issues with it. When we added Acctivate, it solved those issues
Pricing
The pricing function in Acctivate has been very beneficial to us because once you look up a part number, you will have access to your management costs and you can actually see from that same window all the different prices you have issued within that month or within that year to see how the prices fluctuated.
Yolanda Aranda, Accounting Supervisor
The management cost has been set up so that once we receive the material, Acctivate will automatically update itself based on the price that we bought it for in that certain month.
Acctivate is very flexible because it allows us to change prices if we need to – so if for some reason we bought something at one price and then the next month it lowered, we have the option to keep it at that higher price as far as the management cost. It allows us to not lose any money on our inventory if we bought it at a certain price.”
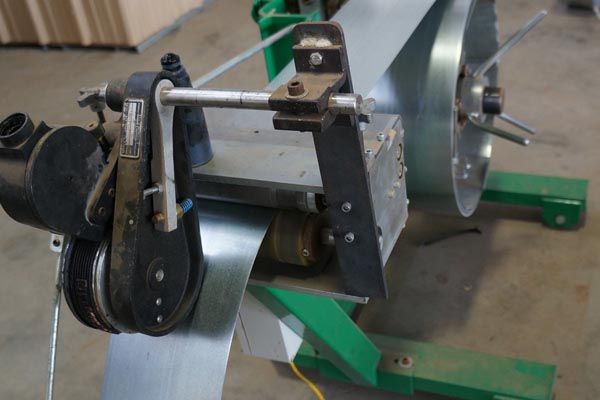
Retail Counter Sales
Acctivate’s retail counter sale function has been a big plus and saved a lot of time and effort. Because what we do is process scrap metal physically, it’s almost like an assembly line – and if you are able to save, for example, five seconds every minute, it’s just exponential. It’s hard to explain how much over the course of a day or a week or a month that time saved will do.
Gene Day, Owner
For every transaction and every sale that we process — which we have numerous transactions at all our locations every day — the time saved using Acctivate certainly adds up a lot more than we ever could realize.”
Day on how their previous system had added extra time and cost to their counter sales…
Up until we added Acctivate, it was just difficult for us to write a ticket at our different locations and to have that integrate into our system. Our invoices would not always go into our accounting system cleanly so we constantly had to go back and make adjustments.
There were added costs that technical people would have to correct. Since it didn’t always transfer in and out of inventory the proper way, every month, they would have to go back to correct things. When we added Acctivate, that took care of the problem and we didn’t have to go back and do all this extra work.”
Sales & Customer Management
Because I am in accounting, the best feature in Acctivate for me is the customer screen. You can pull up the customer and actually see what is past due, what is current, and the invoices. From the same window, I can click on that invoice and it’ll actually open the invoice and show me exactly what was purchased.”
Yolanda Aranda, Accounting Supervisor
She described the order management process with Acctivate…
Sales order management in Acctivate is great. As long as somebody has a receipt or even knows a first name of the customer, we can always track any order including open orders, quotes or invoices so it’s been very beneficial. Acctivate’s been very, very good as far as trying to backtrack and trying to find stuff.”
Acctivate has helped Hobbs Iron & Metal with customer relationship management.
Nowadays a lot of our businesses are going paperless, and now we are able to send an invoice directly from Acctivate without having to print it or fax it – we can email it. This has been very beneficial to us and our customers because normally, all of our customers would rather have an invoice via email rather than a paper invoice – and we can send an email straight from the customer account or the invoice itself.
Acctivate’s also been good for our customers by letting us look up invoices for them in a quick manner and by letting us see our customer accounts, where they stand, what invoices they have, what payments they have made or not made, etc.”
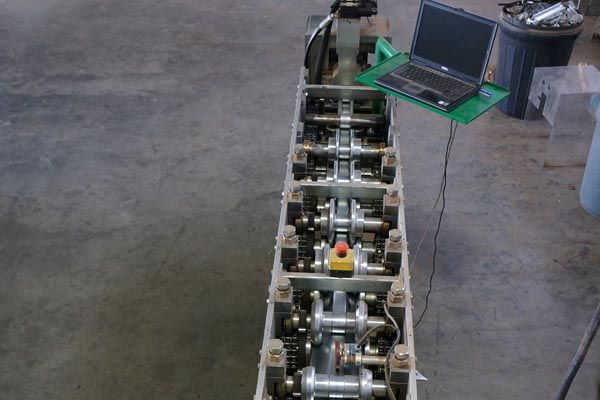
Acctivate – a stable solution that supports growth
Day on Acctivate’s longevity…
Something you always worry about when you buy software is you want to know: is it going to last or is it going to be obsolete in two or three years? That’s always your worst fear…
But I’ve been very pleased with Acctivate since we got it in 2005 – and it’s still doing everything we need it to do and we haven’t even considered changing anything.
As a business, you’re always looking to improve things and I think that’s the real measure – is your software keeping you up to date? In that regard, Acctivate has done a good job.”
Call us at 817-870-1311