Bill of Materials (BOM) Software
Built For
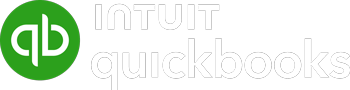
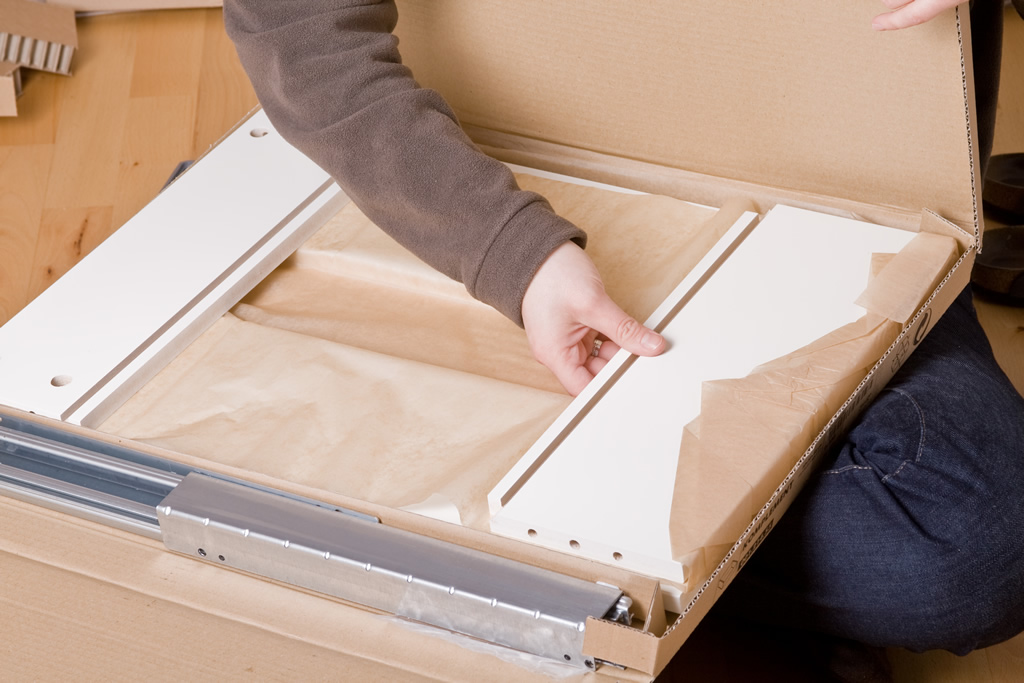
Bill of materials software (BOM) with kitting and assembly maximizes resources
Bill of materials software (BOM) with kitting and assembly capabilities work together to efficiently use business resources and stretching cash flow by maximizing the use of inventory. The bill of materials (BOM) is an important part of the manufacturing process and is used to specify the components used to build a product. Kitting, or making a finished product on demand, and assembly, or creating a finished product to stock inventory, both require the advanced multi-level bill of materials functionality found in inventory management and bill of materials software (BOM).
Whether products are made to stock (assembly), made on demand (kitting) or a combination of the two, Acctivate controls the inventory, and provides visibility on sales, margins, availability and anticipated current and future component inventory requirements.
Bill of Materials (BOM)
As stated above, the bill of materials (BOM) is an important part of the manufacturing process and is used to specify the components used to build a product.
Acctivate’s multi-level bill of materials can be used for products designated as either an assembly (made to stock), a kit (made to order), or can be used with batch process manufacturing, where it is used to handle the formula, recipe, or ingredients list.
Key features of the Acctivate bill of materials software (BOM)
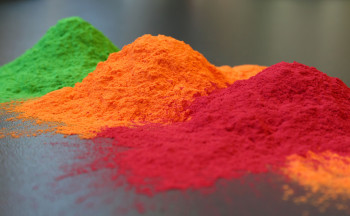
- The Bill of Materials may be changed at any time while preserving the sales history for previously assembled or kitted products
- Unlimited Bill of Materials components
- The components, the completed product, or both may be serialized or lot numbered.
- Partial assemblies can be posted and the remainder can be kept in progress until ready to post
- Custom Kitting to make one-off changes to the quantity of kit components or add/remove components from a kit on a sales order
- Custom manufacturing (Variable build assembly)
- Batch process manufacturing allows for components to be adjusted based on seasonal requirements, availability, or the requirement for substitutions.
- On product produced, batch process manufacturing provides the ability to compensate for variable yield with the ability to alter the quantity produced.
Made to Stock: Assembly
Made to stock inventory, or assembly, creates a new product, with the components used depleted from inventory and the new product added to the finished goods inventory.
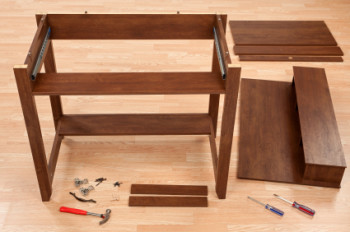
Imagine that a company sells a build it yourself desk as one of its products. This desk is made up of different parts and when the parts are put together, the result is an assembled product – that is, an assembly is created.
The parts to make the assembly may be purchased from different vendors and, when received from each vendor, the assembly parts are entered into inventory.
Once all the required parts for the assembly are received, a product called “desk” is created – which is the assembled product.
Upon creation of the new product, the components used in the assembly are depleted from inventory and the new product is added to replenish the finished goods inventory.
The desk parts are boxed as a product and placed on the shelf. Upon receipt of an order, the boxed product is pulled and shipped.
Made to stock/Assembly: Product example
- There are 3 primary components in this example:
Component 1 = Bookshelf top
Component 2 = Bookshelf sides
Component 3 = Bookshelf base - The bookshelf parts are boxed as a product and placed on the shelf.
- Upon receipt of an order, the boxed product is pulled and shipped.
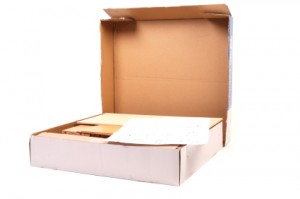
Made to stock/Assembly: Common uses
Light manufacturing: Businesses that make their own inventory products and need to maintain a bill of materials, produce work orders, maintain component/raw materials inventory, foreign or domestic outsourcing.
Made to stock/Assembly: Inventory management
- Upon creation of the new product, the components used in the assembly are depleted from inventory and the new product is added to replenish the finished goods inventory.
- “Where Used” report provides a listing of each product whose bill of materials calls for the use of a component.
Made to stock/Assembly: Pricing
Pricing is based on the end product.
Made to stock/Assembly: Costing
Cost of assembled product is derived from cost of components at the time of assembly.
Made to stock/Assembly: Benefits
- Reduce production cost by producing larger production runs.
- Increase customer satisfaction by shortening lead times.
- Achieve predictability through the use of documented, standardized processes with the creation of a bill of material (BOM).
Made on Demand: Kitting
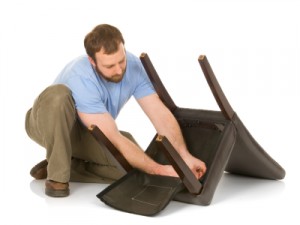
Made on demand, also called kitting, enables companies to sell products as a single unit that are composed of multiple components by kitting, or making them on demand, when shipped.
Made on demand/Kitting: Product example
- There are 2 primary components in the example:
Component 1 = Chair frame
Component 2 = Chair fabric covering - The components can be combined with different fabrics & are not combined to form the end product until an order is received.
- At the time of the order, the components are combined based on the customer’s selection.
- Upon completion, the resulting product is boxed and immediately shipped.
Made on demand/Kitting: Common uses
Situations that require simple assembly or an unassembled collection of components sold as a single unit for a specific order, drawing components from inventory at the time of picking based on an associated BOM.
By using kitting rather than assembly the components are not dedicated to a particular finished product until an order is received and scheduled for delivery for that product.
Made on demand/Kitting: Inventory management
- Upon invoicing of the customer order, the components used in the kit are depleted from inventory.
- Availability is drawn from the components rather than the kit.
- Reorder is at the component level.
- “Where Used” report provides a listing of each product whose bill of materials calls for the use of a component.
Made on demand/Kitting: Pricing
Pricing is based on the end product.
Made on demand/Kitting: Costing
Cost of material is derived from components at the time of shipment.
Made on demand/Kitting: Benefits
- Reduces level of components required by delaying commitment of components until order is received.
- Ability to adapt to changes in customer demand.
- Allows for Just in Time (JIT) inventory management.
- Enables flexible and short-term promotions.
- Achieve predictability through the use of documented, standardized processes with the creation of a bill of material (BOM).
Call us at 817-870-1311