Android Warehouse Management System
Built For
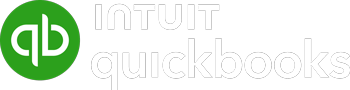
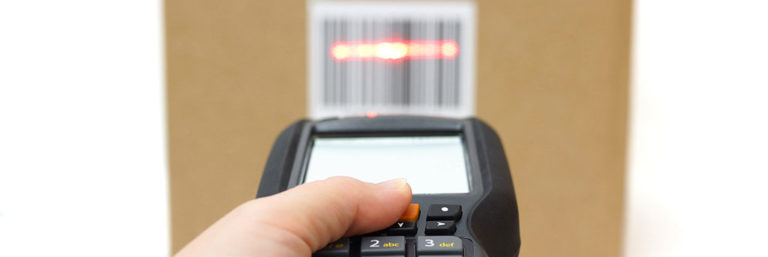
Android Warehouse Management System
Warehouses running on manual or outdated, disjointed systems are not primed for growth. Instead of wasting time and money trying to run a warehouse manually or with old systems, consider an Android warehouse management system.
Why you need an Android warehouse management system
Google’s Android boasts 90% of smartphone users, but their operating systems reach further, exchanging phones for rugged devices in the hands of warehouse teams across the United States.
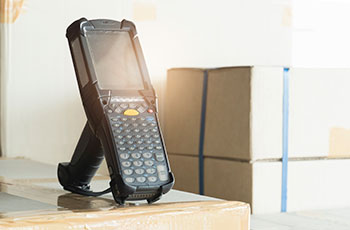
Microsoft’s future of supporting Windows devices in the warehouse is slowly being phased out – meaning current users will become legacy users and will eventually lack access to tech support and necessary updates.
Acctivate’s adaptation of an Android warehouse management system is the solution for not only operating at maximum efficiency and, productivity but also for future-proofing warehouses as Android operating systems become more and more dominant in the market than they already are.
Acctivate’s Android warehouse management system introduces two key features, order picking and inventory receiving – the two most frequent tasks in any warehouse. The devices also allow for quick barcode scans to present a user with any and all relevant data encoded into a particular barcode.
Order picking with an Android warehouse management system
The days of manual misguided (literally) order picking are now a thing of the past. With the introduction of an Android warehouse management system and Android OS rugged devices (barcode scanners) into the warehouse, order picking is easier than ever before.
When it is time for a warehouse employee to pick orders, the first step is picking up the device. An Android warehouse management system drastically improves the speed and accuracy of order picking operations. On the screen, a list of order numbers will appear with the customer’s name listed underneath, and the date of the order requested to the right. Once an order is clicked, a picklist is created presenting all the items requested as well as their corresponding quantities and bin locations. A user can simply key the picked quantity into the device to fulfill the picked order or scan the barcode as many times as needed to meet the quantity. After one product is picked, a user can simply just click down to the next order and do the same process over again. As each order is completed, a picking workflow status can be updated to keep other warehouse staff up to date. Once completely picked, shipping labels and pack lists can be created.
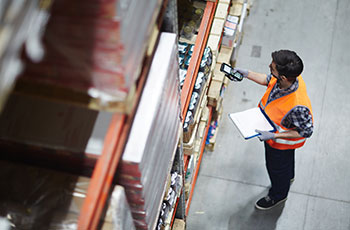
Receiving inventory with an Android warehouse management system
Inventory receiving with an Android warehouse management system works similarly to order picking. When a user picks up the device, a list of purchase orders will appear. A user selects the appropriate purchase order items to receive along with corresponding quantities and bin locations for put away. A user can either scan the barcode the number of times needed or just quickly input the quantity received into the keypad. After a purchase order is fully received, a user can post the receipt to add the inventory immediately or the receipt session can be saved and opened at any desktop workstation running Acctivate.
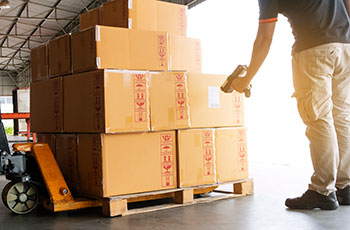
An Android warehouse management system and Acctivate
Acctivate offers the necessary tools to optimize lagging warehouse systems and create more efficiency and accuracy in your warehouse. Acctivate’s introduction of the Android warehouse management system is an exciting step for the future of Acctivate warehouse technology.
Acctivate Warehouse Management System for QuickBooks
For QuickBooks users, Acctivate’s Android warehouse management system is a no-brainer. QuickBooks and Acctivate support a bi-directional integration allowing QuickBooks users to continue managing accounting within QuickBooks while gaining the advanced tools and support of Acctivate.
Call us at 817-870-1311