5 Strategies for Reducing Fulfillment Errors
Built For
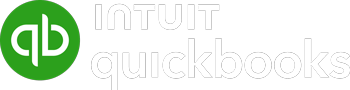
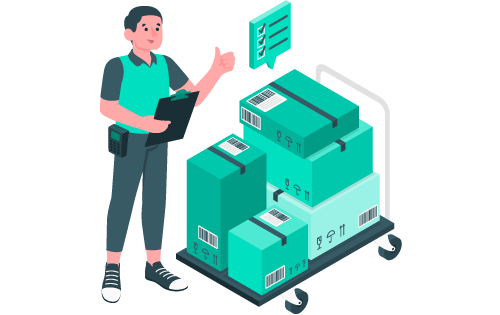
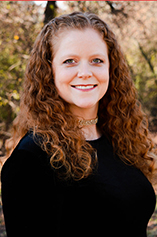
5 Strategies for Reducing Fulfillment Errors
Getting orders right every time is critical in today’s super competitive marketplace. With customers expecting their orders to be perfect and delivered fast, there’s no room for mistakes. Fulfillment errors can be a headache, leading to unhappy customers, extra shipping costs, and wasted time.
Fulfillment errors can pop up at any stage, from picking and packing to shipping and delivery. They often happen because of human mistakes, outdated inventory data, poor team communication, cluttered warehouse layouts, and lack of proper training. Tackling these issues is vital to keeping things running smoothly and cutting unnecessary costs.
Today, we examine common causes of fulfillment errors and share practical tips to help you reduce them. You can significantly reduce mistakes by using inventory management software and barcode technology, optimizing your warehouse setup, and boosting staff training. These steps will make your operations more efficient and help you build stronger customer relationships.
Common Causes of Fulfillment Errors
Understanding why fulfillment errors happen is the first step toward fixing them. Here are some of the most common culprits:
- Human Errors in Picking and Packing. Mistakes happen, especially when employees are working quickly or under pressure. Picking the wrong items or packing orders incorrectly are frequent issues that can lead to customer dissatisfaction.
- Inaccurate Inventory Data. If your inventory records are off, you might think you have enough stock to fulfill an order when you don’t. This can result in delays and backorders, frustrating your customers and complicating your operations.
- Miscommunication Between Departments. Things can go wrong when sales, inventory, and fulfillment teams aren’t on the same page. Orders might get lost in the shuffle or shipped to the wrong address, resulting in customer complaints.
- Inefficient Warehouse Layout. A cluttered or poorly organized warehouse can slow the picking process and increase the likelihood of errors. If items are hard to find or stored in inconvenient locations, it takes longer to fulfill orders, making mistakes more likely.
- Lack of Proper Training. Employees not adequately trained on picking, packing, and using inventory systems are more prone to errors. Ongoing training is essential to ensure everyone knows the best practices and procedures.
By identifying these common issues, you can start to address them and improve your fulfillment process.
Strategy #1 for Reducing Fulfillment Errors: Implement Inventory Management Software with Barcoding
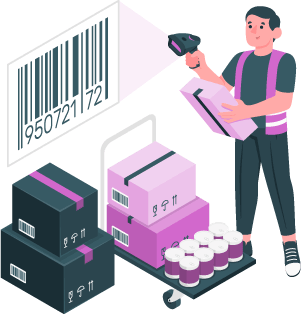
Real-time Inventory Tracking
Keeping your inventory data up-to-date is crucial for reducing fulfillment errors. Inventory management software provides real-time tracking, ensuring your stock levels are always accurate. This prevents situations where an item is oversold, or a product is marked as available when it’s actually out of stock. Having a clear, up-to-the-minute view of your inventory can avoid delays and backorders, leading to smoother operations and happier customers.
Automated Reorder Point Alerts
Automated reorder point alerts in inventory management software allow you to set minimum product quantity thresholds. When an item reaches the predefined threshold, the system triggers an alert to reorder, helping to maintain optimal stock levels. Reorder alerts reduce the risk of stockouts and the manual effort involved in tracking inventory levels. As a result, your team can focus on fulfilling orders accurately rather than constantly monitoring inventory.
Centralizing Orders from All Sales Channels
Centralizing orders from all sales channels is critical for reducing fulfillment errors. When orders come in from various sources—such as eCommerce sites, online marketplaces, EDI, and direct sales—it can be challenging to keep track of everything manually.
Centralization provides a unified view of inventory levels and order statuses, reducing the risk of overselling or stockouts. It also ensures that inventory levels are updated as orders are placed, preventing discrepancies between different sales platforms. Centralized order management enhances coordination between sales and fulfillment teams, leading to fewer mistakes and more efficient operations. Ultimately, this approach helps maintain accurate inventory data and improves customer satisfaction by ensuring correct and timely order fulfillment.
Utilize Barcode Technology
Barcoding simplifies tracking and managing inventory, significantly reducing the risk of manual entry errors. Each product is assigned a barcode, which can be scanned at various stages of the fulfillment process, ensuring that the correct items are picked, packed, and shipped, enhancing accuracy. Barcoding also speeds up the data entry process, making it more efficient and less prone to mistakes.
Strategy #2 for Reducing Fulfillment Errors: Optimize Warehouse Layout
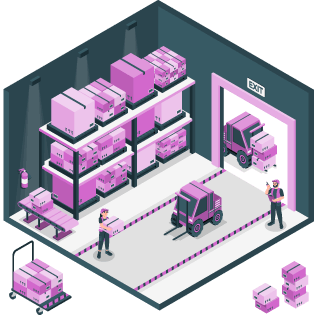
Organizing your warehouse for easy access is essential for speeding up the picking process and reducing errors.
Efficient Storage Solutions
Clearly labeled shelves and bins ensure that items are stored in logical, easy-to-find locations. This organization minimizes the time employees spend searching for products, allowing them to fulfill orders more quickly and accurately.
Streamlining Picking Paths
Creating efficient picking paths in your warehouse significantly reduces the time it takes to pick items for an order. By arranging products to minimize travel distance, you can streamline the picking process. Implementing batch-picking or wave-picking techniques can enhance efficiency by allowing workers to pick multiple orders simultaneously. These strategies help reduce errors and improve overall productivity.
Zone Picking Strategies
Dividing the warehouse into zones can minimize travel time and increase picking accuracy. Each zone is assigned to employees who become experts in their designated areas. This specialization reduces the likelihood of errors, as employees are more familiar with the products in their zones. Zone picking allows for better organization and quicker fulfillment, leading to more accurate and efficient order processing.
Strategy #3 for Reducing Fulfillment Errors: Enhance Staff Training and Accountability
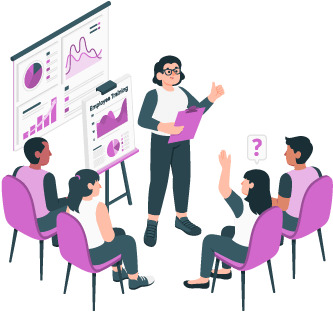
Regular Training Sessions
Regular training sessions for your staff ensure they are up-to-date on best practices and new procedures. Well-trained employees are more likely to follow correct protocols, reducing the chances of errors. Training should cover various aspects of the fulfillment process, from picking and packing to using inventory systems. Continuous education helps maintain high standards of accuracy and efficiency.
Clear Communication of Procedures
Ensuring that everyone understands the fulfillment procedures is crucial for reducing errors. Clear and concise communication of these procedures helps set expectations and provide guidelines for employees to follow. This can be achieved through detailed SOPs (Standard Operating Procedures), training programs, and regular team briefings. When employees know exactly what is expected of them, they are less likely to make mistakes.
Accountability Measures and Performance Tracking
Implementing accountability measures and tracking employee performance can encourage staff to take responsibility for their work. Monitoring key performance indicators (KPIs), such as order accuracy and pick rates, helps identify areas for improvement and recognize high-performing employees. Accountability fosters a culture of precision and reliability, encouraging employees to strive for excellence in their tasks.
Strategy #4 for Reducing Fulfillment Errors: Implement Quality Control Measures
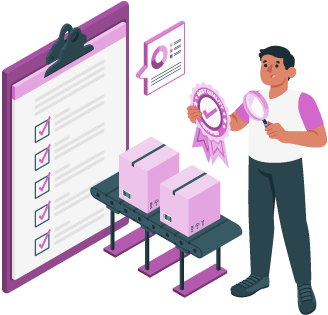
Double-Checking Orders Before Shipment
Verifying that each order is correct before it leaves the warehouse is a simple yet effective way to reduce fulfillment errors. This double-checking process can be performed by a dedicated quality control team or as part of the packing procedure. Ensuring that the right items are shipped to the right customers helps prevent returns and boost customer satisfaction.
Random Quality Audits
Conducting random quality audits can help identify recurring issues and improve processes. These audits involve randomly selecting orders to review for accuracy and procedure compliance. Insights gained from these audits can be used to refine fulfillment processes and address any weaknesses. Conducting regular audits promotes a culture of continuous improvement and high standards.
Using Checklists and Verification Steps
Standardizing the packing process with checklists and verification steps can significantly reduce the chance of mistakes. Employees can follow a step-by-step guide to ensure all items are included and correctly packed. This systematic approach ensures that every order meets the required quality standards.
Strategy #5 for Reducing Fulfillment Errors: Improve Communication and Coordination
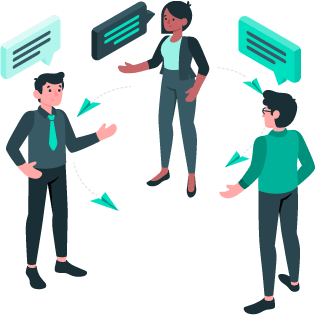
Cross-Departmental Communication Tools
Facilitating information sharing between sales, inventory, and fulfillment teams is essential for reducing errors. Cross-departmental communication tools ensure everyone has access to accurate information, helps in coordinating efforts, and preventing miscommunication that can lead to fulfillment mistakes.
Regular Team Meetings
Holding regular team meetings keeps everyone updated, allows potential issues to be addressed promptly, and provides an opportunity share updates, discuss challenges, and brainstorm solutions. Open communication fosters a collaborative environment where problems can be solved quickly and effectively.
Call us at 817-870-1311