Improve Your Tracking Capabilities
Built For
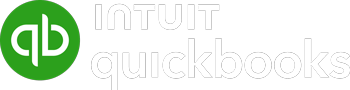
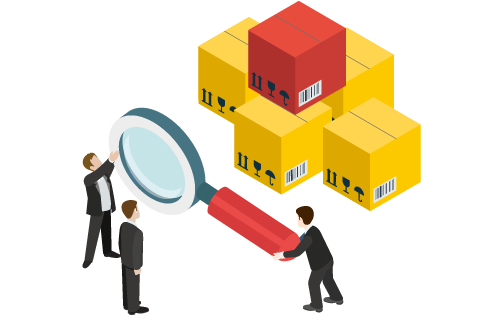
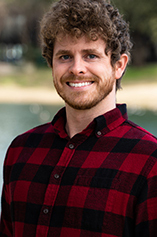
Improve Your Tracking Capabilities
Keeping track of inventory and orders can feel like juggling a dozen balls at once—one slip and the whole process can come crashing down. That’s where strong tracking capabilities and traceability come into play.
Improving your tracking and traceability capabilities isn’t just about preventing chaos; it’s about enhancing efficiency, reducing errors, boosting customer satisfaction, and, in some cases, compliance with regulations. Whether running a small business or managing a large-scale operation, robust tracking and traceability systems are essential. In this blog article, we’ll dive into what makes tracking and traceability crucial, explore key components, and share strategies to elevate your tracking game to the next level.
Understanding Tracking Capabilities
Tracking capabilities refer to the methods and tools used to monitor the movement and status of inventory and orders throughout the supply chain. Effective tracking ensures that every item is accounted for at every stage, from procurement to storage to delivery. But why is tracking so important?
First, tracking provides visibility.
Visibility allows you to see where your products are at any given moment, which is crucial for managing inventory levels, preventing stockouts, and ensuring timely delivery to customers. Without proper tracking, you might end up with too much of one product and not enough of another, which can lead to lost sales and unhappy customers.
Second, tracking enhances accuracy.
Manual tracking methods, such as spreadsheets or paper records, are prone to errors. These errors can lead to misplaced items, incorrect shipments, and increased costs. Tracking systems significantly reduce these errors by providing precise, real-time data.
Third, tracking supports compliance.
Many industries have regulations requiring detailed records of product movements, especially for pharmaceuticals, food products, and hazardous materials. Effective tracking ensures you can easily provide the necessary documentation to meet these regulatory requirements.
Finally, tracking improves traceability.
Traceability is the ability to trace an item’s history or location using recorded identification. This is particularly important for industries where recalls are common. With strong traceability, you can quickly identify and isolate affected products, minimizing the impact on your business and customers.
Key Components of Effective Tracking Systems
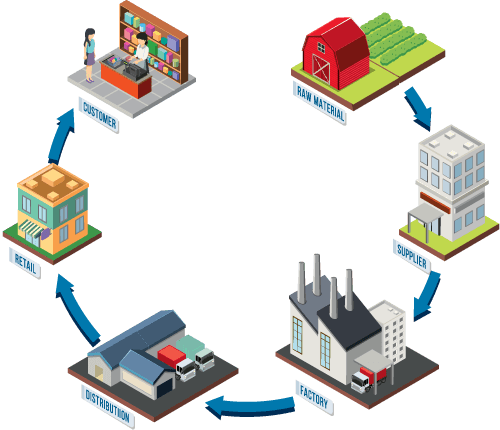
An effective tracking system combines powerful inventory management software with barcode technology and seamless integration with other systems, such as QuickBooks and eCommerce platforms. These components work together to enhance accuracy, improve efficiency, and ensure compliance, providing a comprehensive solution for all your tracking needs.
Inventory Management Software
Inventory management software tracking is the backbone of an effective tracking system. It provides comprehensive tools for managing inventory levels, orders, and traceability. Key features include:
Purchasing
- Simplified Procurement: The process of purchasing inventory is streamlined, reducing the need for manual intervention.
- Supplier Management: Supplier details, lead times, and order histories are tracked to ensure timely and cost-effective procurement.
- Stock Level Alerts: Notifications are sent when stock levels are low, helping to prevent stockouts and overstock situations.
- Purchase Order Generation: Purchase orders are generated quickly based on real-time inventory data, ensuring accuracy and reducing the risk of over or under-ordering.
Inventory
- Multi-location Tracking: Inventory across multiple warehouses or storage locations is monitored, providing a unified view of stock levels.
- Inventory Valuation: Real-time valuation of inventory aids in financial reporting and decision-making.
Traceability
- Lifecycle Tracking: Detailed records of each item’s journey throughout the supply chain are recorded, from procurement to final delivery.
- Regulatory Compliance: Adherence to industry regulations is maintained by providing necessary documentation and traceability for audits.
- Recall Management: Quick identification and isolation of affected products in case of a recall is facilitated, minimizing impact on the business.
Centralized Order Management
- Order Consolidation: Orders from various sales channels (e.g., eCommerce platforms, EDI, direct sales) are consolidated into a single system.
- Order Tracking: Real-time updates on order status, from receipt to fulfillment, provide processing and delivery tracking.
- Customer Notifications: Automated notifications keep customers informed about their order tracking status.
Integration with QuickBooks
- Financial Synchronization: All financial data, including sales, purchases, and inventory costs, is accurately reflected in QuickBooks and the inventory software with bi-directional integration.
- Reduced Data Entry: The need for manual data entry is reduced or eliminated, reducing errors and saving time.
- Comprehensive Reporting: Detailed financial and inventory reports help businesses make informed decisions.
Real-Time Tracking
- Instant Updates: Dashboards immediately update inventory levels, order status, and other critical data.
- Decision Making: Quick, informed decision-making is enabled with accurate, up-to-date information.
- Customer Communication: Real-time tracking information keeps customers informed about their orders.
Barcode Technology
Barcode technology integrated with inventory management software is a fundamental tracking system component. It enhances accuracy by reducing manual entry errors and speeding up data entry. Barcodes can be used at various stages, from receiving goods to shipping orders, ensuring that each item is accurately tracked throughout its journey.
- Error Reduction: Manual data entry errors are minimized by automating the scanning and recording of inventory movements.
- Speed and Efficiency: Inventory management tasks, such as receiving, picking, packing, and shipping, are performed much more quickly.
- Ease of Use: Recording inventory movements is simplified, making it easy for employees to scan items and update records.
- Receiving Goods: Incoming inventory is scanned and recorded, ensuring accurate and timely updates to stock levels.
- Shipping Orders: Items are picked, packed, and shipped with increased accuracy, reducing the risk of errors in order fulfillment.
- Inventory Audits: Inventory audits are completed quickly and accurately by scanning items and comparing them to system records.
Tracking Capabilities Case Study: AP Tech Group
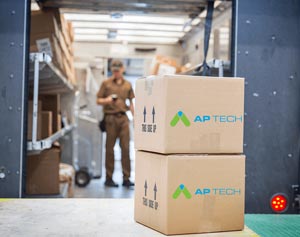
AP Tech Group is a global leader in solid water treatment products used in the industrial cooling and heating equipment industry. Unlike the industry standard of liquid products, AP Tech Group’s solid products significantly reduce shipping costs, enhance safety and environmental sustainability, and facilitate easy application.
The Challenge
As AP Tech Group’s products play a crucial role in maintaining complex and valuable equipment, managing inventory and order fulfillment efficiently became imperative, especially as the number of SKUs grew. Initially, the company used QuickBooks for financial management and relied on spreadsheets for inventory tracking. However, modifying the spreadsheet became cumbersome as their product range expanded and provided minimal reporting or visibility.
The Solution
Seeking a more robust solution, AP Tech Group explored multiple options and ultimately selected Acctivate to manage its operations. The modular design of Acctivate allowed them to implement the necessary features incrementally and scale as the company grew. This modularity and scalability were central factors in their decision.
Integration with QuickBooks
One significant advantage of Acctivate was its seamless integration with QuickBooks, which AP Tech Group already used. This integration ensured their financial data remained up-to-date without extensive retraining on a new system. AP Tech Group streamlined its operations by retaining familiarity with QuickBooks and adding an additional layer of functionality with Acctivate.
Immediate Benefits
After implementing Acctivate, AP Tech Group quickly realized a return on investment. The switch from spreadsheets to Acctivate enhanced inventory management and operational efficiency. Sales staff became more informed about product availability, improving customer satisfaction.
- Lot and Serial Number Tracking: Acctivate enabled AP Tech Group to track equipment serial numbers and chemical product lot numbers. The system allows them to manage recalls efficiently, understand the Cost of Goods Sold more accurately, and enable precise cost tracking by lot number, enhancing the accuracy of their financial reporting.
- Order Fulfillment: Acctivate optimized AP Tech Group’s order fulfillment process, which involves shipping 50 to 100 packages daily. By integrating with UPS and FedEx, the system reduced shipping errors and associated costs. The ability to generate pick tickets and manage the picking process streamlined operations and facilitated quick training for new employees. Additionally, regulation-specific HAZMAT labeling on pick tickets improved compliance.
- Shipping Integration: Acctivate’s integration with shipping carriers provides instant access to tracking numbers automatically sent to customers with their invoices. This automation saved significant time previously spent on manual data entry and customer calls, enhancing overall efficiency and customer satisfaction.
Overall Impact
Since implementing Acctivate, AP Tech Group has seen increased sales without additional processing time. The system has saved considerable time by digitizing paperwork and making all data easily accessible through the database. This comprehensive data accessibility has improved reporting and tracking capabilities and operational stability.
Call us at 817-870-1311