Streamlining Your Warehousing Processes from Receiving to Shipping
Built For
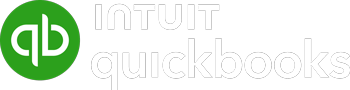
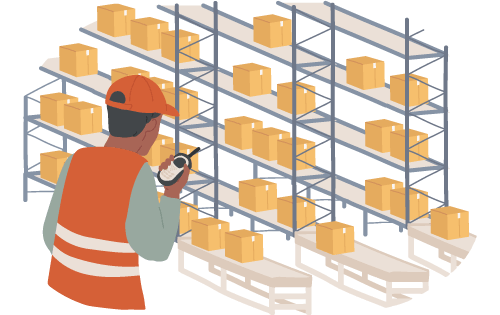
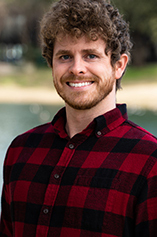
Streamlining Your Warehousing Processes from Receiving to Shipping
Warehousing is the backbone of any business that deals with physical products. Whether managing raw materials or finished goods, your warehouse is a critical hub that keeps your business operations moving.
Efficient warehousing processes ensure that inventory is well managed, orders are fulfilled quickly, and customer satisfaction is maintained. But how do you streamline these processes from the moment inventory arrives to the point where it’s shipped out? Let’s explore how to optimize your warehousing processes from receiving to shipping.
The Importance of Efficient Warehousing Processes
Warehousing is more than just storing items—it’s about managing the flow of goods to support the overall supply chain. Every step in your warehousing process, from receiving goods to shipping out orders, impacts your business’s operational efficiency, costs, and customer experience. Streamlining each stage can save time, reduce errors, and boost your bottom line.
Today, we’ll break down each step in the warehousing process and highlight the best practices to help you streamline operations, all while integrating technology to make the process easier and more accurate.
The Receiving Process: Setting the Stage for Success
The receiving process is the first step in your warehousing operation, setting the tone for everything that follows. If you don’t manage receiving efficiently, you could be dealing with stock discrepancies, inventory loss, or delays further down the line.
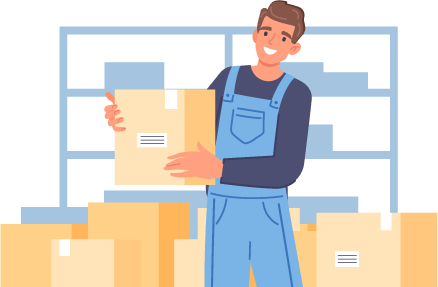
What Happens During Receiving?
Receiving is when goods arrive at your warehouse from a supplier or manufacturer. At this point, items are inspected, verified against purchase orders, and entered into your inventory system. The goal is to ensure that everything matches what was ordered and that discrepancies are addressed immediately.
Best Practices in Warehousing Processes for Streamlining Receiving
Technology is critical in improving warehousing processes and ensuring items are received in your warehouse efficiently and with minimal errors. That accuracy at the outset has ripple effects throughout your warehousing processes.
Two technologies are vital for achieving accuracy in the receiving process:
- Barcode Scanning: One of the best ways to speed up and improve accuracy in the receiving process is by using barcode scanners. Instead of manually entering data, employees can scan items to instantly log them into your inventory system.
- Inventory Software: Inventory software allows real-time updates as goods are received, making it easier to track inventory levels and flag any discrepancies on the spot.
Inventory Management: Keeping Things in Check
Once your inventory is received, the next critical process is managing it effectively. Poor inventory management may lead to overstocking, understocking, or even losing track of goods altogether, directly affecting your ability to fulfill orders.
Key Aspects of Inventory Management
- Tracking Inventory: You need to know exactly what’s in your warehouse and its location. Keeping inventory organized and easily accessible is crucial for avoiding delays in order fulfillment.
- Stock Levels: Efficient inventory management means keeping the right amount of stock on hand—not too much or too little. Overstocking ties up capital and takes up space, while understocking usually results in missed sales opportunities.
Best Practices in Warehousing Processes for Effective Inventory Management
- Leverage Inventory Management Software: Inventory management software tracks stock levels in real time, helps forecast demand, and automates replenishment alerts.
- Organize by SKU: A well-organized warehouse is vital for efficient inventory management. Organizing products by SKU (Stock Keeping Unit) helps ensure that the right product is picked every time, reducing errors and improving efficiency.
- Cycle Counting: Instead of shutting down your warehouse for an annual inventory count, consider implementing cycle counting. This method breaks inventory counts into smaller, manageable segments, reducing downtime while keeping your inventory numbers accurate.
Effective inventory management doesn’t just ensure that you have the right products on hand—it also helps you reduce carrying costs and improve order fulfillment times. By leveraging technology and best practices, you’ll stay organized and efficient.
Picking and Packing: Speed and Accuracy Matter
Picking and packing are the core of your order fulfillment process. Without an efficient system, you risk slowing down the entire operation. Getting the right products out the door as quickly as possible while maintaining accuracy is essential for customer satisfaction.
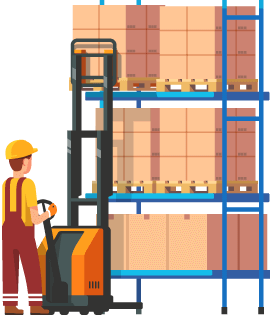
Optimizing the Picking Process
Picking refers to locating the correct items in your warehouse to fulfill customer orders. There are several picking methods that businesses use, depending on the size and layout of their warehouse:
- Batch Picking: This method involves picking multiple orders at once to optimize travel time within the warehouse. Batch picking is ideal when you have multiple orders with similar items.
- Zone Picking: This method divides the warehouse into different zones. Employees are assigned to specific zones and only pick items within that area. This reduces unnecessary movement and speeds up the picking process.
- Wave Picking: In wave picking, orders are grouped based on criteria such as shipping deadlines or product similarity, and employees pick items for multiple orders in a single trip.
Packing with Precision
Once items are picked, they need to be packed efficiently. Packing is not just about speed—it’s about ensuring that the correct items are securely packed and ready for shipping. Using standardized packing procedures and materials helps ensure consistency and reduces the risk of damage during transit.
Best Practices in Warehousing Processes for Picking and Packing
- Barcode Technology: Use barcode scanners to ensure that the correct items are picked every time. This reduces errors and allows for real-time inventory updates.
- Packing Stations: Create designated packing stations where employees can quickly and easily prepare orders for shipping.
- Inventory Software: Automating the picking and packing process with inventory software can streamline operations and increase accuracy.
Efficient picking and packing speed up the order fulfillment process and help maintain high customer satisfaction levels by ensuring that orders are fulfilled correctly the first time.
Shipping: The Final Step in the Journey
Once an order is packed, it’s time to ship it to the customer. Shipping is the final touchpoint in the warehousing process, and getting it right is crucial for maintaining customer satisfaction. Delayed or incorrect shipments can damage your reputation and result in costly returns.
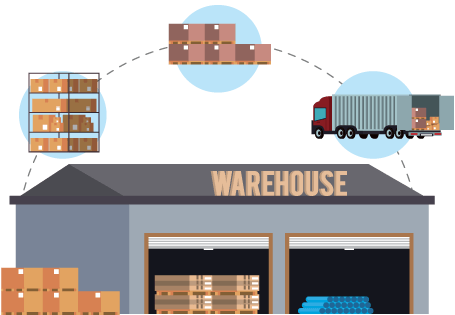
Best Practices in Warehousing Processes for Streamlining Shipping
- Integrate Shipping Software: Shipping software integrated with your inventory system automates the creation of shipping labels and tracking orders in real time. This reduces manual entry errors and ensures accurate shipping information.
- Real-Time Tracking: Providing customers with real-time tracking information helps improve transparency and keeps them informed about their order status.
- Prevent Shipping Errors: Double-check orders before they go out the door using barcode scanners to ensure that the correct items are shipped, reducing costly returns and re-ships.
Streamlining the shipping process can reduce delays and errors, ultimately improving customer satisfaction and reducing shipping costs.
Integrating Technology to Streamline the Entire Process
As seen in the steps above, technology is pivotal in optimizing warehousing processes. Barcode scanners used with advanced inventory management software enhance visibility, boost efficiency, and reduce manual errors at every stage. By leveraging technology, businesses can streamline their entire warehousing operation and ensure smoother, more accurate processes from start to finish.
Call us at 817-870-1311