Achieving Accuracy and Precision in Inventory and Order Management
Built For
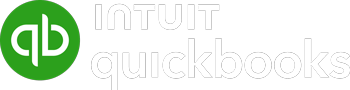
Achieving Accuracy and Precision in Inventory and Order Management
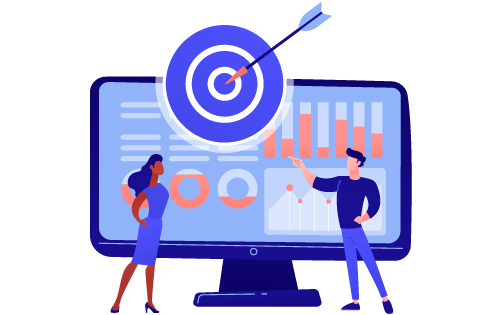
Achieving accuracy and precision in inventory and order management is more critical than ever. How many times have you faced issues like stockouts or overstocking? Or perhaps you’ve dealt with frustrated customers due to incorrect orders? These are common problems that stem from inaccuracies in inventory and order management.
Accuracy ensures that your data matches the actual inventory on hand, while precision ensures that this data is consistently reliable. In other words, accuracy means getting it right, and precision means getting it right every time. Both are essential for smooth operations, customer satisfaction, and, ultimately, the success of your business.
In this article, we’ll explore the importance of accuracy and precision in inventory and order management, delve into common challenges, and provide practical strategies to enhance both.
Understanding Accuracy and Precision
Imagine always having precisely what your customers want, exactly when they want it. Sounds like a dream, right? Well, that’s the magic of accurate demand forecasting. It’s the process that helps businesses predict future customer demand, ensuring they can meet it efficiently and effectively.
Accuracy vs. Precision
Accuracy refers to how close your inventory records are to the actual physical inventory. For example, your inventory records are accurate if your system shows that you have 50 units of a product in stock, and a physical count confirms that you indeed have 50 units.
Precision, on the other hand, is about consistency. It means consistently getting the same results under the same conditions. In inventory management, precision means that you get the same result every time you count your stock. For example, if you count your inventory multiple times and each count consistently shows 50 units, your counting process is precise.
Importance of Accuracy and Precision in Inventory and Order Management
Why are accuracy and precision so crucial? Simply put, they help you avoid the pitfalls of inventory mismanagement. Inaccurate inventory data can lead to stockouts, overstocking, and dissatisfied customers. Lack of precision can cause fluctuating stock levels and erratic order fulfillment, making it hard to trust your inventory data.
Accurate and precise inventory management allows you to make better business decisions, streamline operations, and maintain high levels of customer satisfaction.
Common Challenges to Achieving Accuracy and Precision
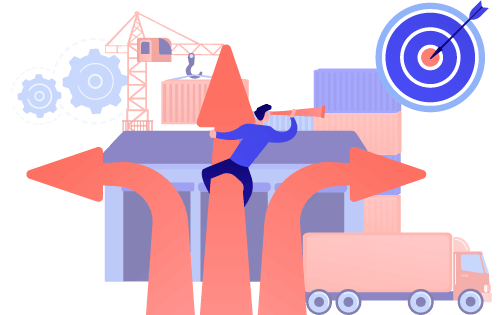
Achieving high levels of inventory and order management accuracy and precision in is no small feat. Various challenges can hinder your efforts, leading to discrepancies, inefficiencies, and customer dissatisfaction. Let’s explore some of the most common obstacles businesses face.
Human Errors in Data Entry
One of the biggest culprits behind inaccurate inventory data is human error. Whether typos, miscounts, or incorrect recording of inventory movements, these errors can accumulate over time, leading to significant discrepancies between recorded and actual inventory levels.
Inefficient Inventory Tracking Methods
Relying on outdated or inefficient inventory tracking methods, such as pen-and-paper logs or basic spreadsheets, can severely impact accuracy and precision. These methods are time-consuming, lack real-time updates, an make it difficult to maintain accurate records as inventory levels change.
Miscommunications and Data Discrepancies
In many businesses, different departments or teams handle various inventory and order management aspects. Miscommunications between these teams can lead to data discrepancies. For instance, if the sales team is unaware of a recent stock adjustment made by the warehouse team, they might oversell or undersell products, resulting in inaccurate inventory data.
Stock Discrepancies and Order Fulfillment Issues
Stock discrepancies occur when there is a mismatch between the recorded and actual physical stock. These discrepancies can arise from theft, damage, misplacement, or administrative errors. Such inconsistencies can lead to order fulfillment issues, where customers receive the wrong products or face delays in receiving their orders, ultimately affecting customer satisfaction and trust.
Seasonal Demand Fluctuations
Seasonal demand fluctuations can also pose challenges to maintaining accuracy and precision. During peak seasons, the rapid increase in order volume can strain your inventory management processes, increasing the likelihood of errors. Conversely, during off-peak times, you may need help maintaining optimal stock levels without overstocking or understocking.
Lack of Standardized Processes
Inconsistent or lack of standardized processes across different locations or teams can lead to varied inventory practices, making it difficult to achieve uniform accuracy and precision. Without clear guidelines and standardized procedures, maintaining consistent and accurate inventory records becomes challenging.
By understanding these common challenges, you can better prepare to address them and implement strategies to improve the accuracy and precision of your inventory and order management processes.
Strategies for Improving Accuracy
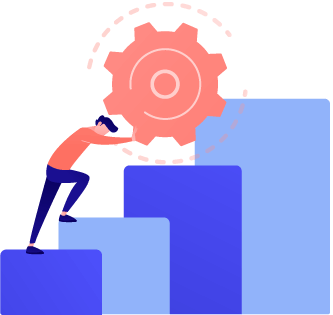
Achieving high levels of inventory and order management accuracy requires a combination of technology, processes, and employee training. Here are some practical strategies to help you improve your inventory management accuracy.
Implementing Barcode Systems
Barcoding is a powerful tool for enhancing inventory accuracy. Using barcode labels and scanners, you can quickly and accurately track inventory movements. Every product is assigned a unique barcode, which, when scanned, updates your inventory management system in real time. This reduces manual errors and ensures that your inventory records are always up-to-date.
Regular Cycle Counts and Audits
Conducting regular cycle counts and audits is essential for maintaining accurate inventory records. Unlike full physical inventories, cycle counting involves regularly counting a small portion of your inventory. This ongoing process helps identify and correct discrepancies promptly. Regular audits further ensure that your inventory data remains accurate over time.
Training Employees on Accurate Data Entry and Inventory Practices
Human errors are a common cause of inventory inaccuracies. To mitigate this, invest in comprehensive training programs for your employees. Teach them the importance of accurate data entry and inventory practices. Ensure they correctly understand how to use your inventory management system and barcode scanners. Regular refresher courses help maintain high standards of accuracy.
Utilizing Real-Time Inventory Tracking Systems
Real-time inventory tracking systems provide continuous updates on inventory levels, helping you maintain accurate records. These systems manage your sales, purchasing, and warehouse management processes, ensuring that every inventory movement is recorded immediately. This real-time visibility allows you to respond quickly to changes in inventory levels, reducing the risk of stockouts or overstocking.
Implementing Quality Control Measures
Incorporate quality control measures at various stages of your inventory management process. For instance, when receiving new stock, perform checks to ensure that the received quantities match the purchase orders. Similarly, when picking and packing orders, double-check the items to ensure accuracy. These quality control steps help catch and correct errors before they impact your inventory records.
Standardizing Inventory Procedures
Develop and enforce standardized inventory procedures across your organization. Clear guidelines and consistent processes ensure everyone follows the same steps when handling inventory. Standardization minimizes variability in managing inventory, reducing the chances of errors and discrepancies.
Implementing these strategies can significantly improve the accuracy of your inventory management processes. Accurate inventory data is the foundation for efficient operations, better decision-making, and enhanced customer satisfaction.
Strategies for Enhancing Precision
While accuracy ensures that your inventory records match the actual physical inventory, precision guarantees consistency in your processes. Here are some effective strategies to enhance precision in inventory and order management.
Leveraging Advanced Inventory Management Software
Advanced inventory management software is crucial for maintaining precision. Such software offers reorder point alerts, real-time inventory updates, and comprehensive reporting tools. These features help ensure that your inventory processes are consistently reliable and that data is accurately recorded every time.
Setting Up Reorder Point Alerts
Reorder point alerts help maintain optimal stock levels by triggering alerts to issue purchase orders when inventory levels fall below a certain threshold. This automation ensures that stock replenishment is consistent and timely, minimizing the risk of stockouts or overstocking.
Using Predictive Analytics for Demand Forecasting
Predictive analytics enhance the precision of your inventory management. Predictive analytics tools accurately forecast future demand by analyzing historical data and market trends. This enables you to plan your inventory purchasing more effectively, ensuring you have the right products in the right quantities at the right time.
Ensuring Precise Order Picking and Packing Processes
Precision in order picking and packing is essential for fulfilling orders accurately. A systematic approach to picking and packing, such as zone or batch picking, can help streamline these processes. Additionally, technology like barcode scanners can ensure that the correct items are picked and packed every time.
Role of Inventory and Order Management Software for Achieving Accuracy and Precision
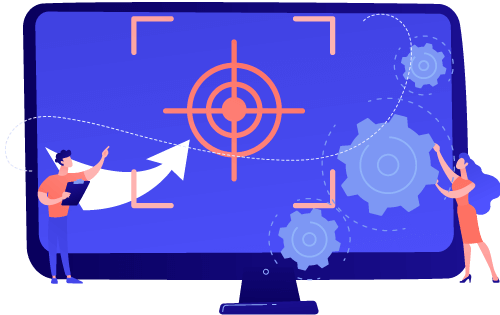
Inventory and order management software plays a pivotal role in achieving both accuracy and precision. Here are some key features of such software that contribute to these goals:
Real-Time Inventory Updates
Inventory management software provides real-time updates, ensuring your inventory data is always current. This real-time visibility helps prevent discrepancies and allows for immediate adjustments when necessary.
Integration with Barcode Scanning Technology
Integration with barcode scanning technology enhances both accuracy and precision. Scanning barcodes for inventory movements, order picking, and shipping ensures that data is recorded accurately and consistently.
Comprehensive Reporting and Analytics
Inventory management software offers comprehensive reporting and analytics tools. These tools provide insights into inventory performance, helping you identify patterns, detect discrepancies, and make informed decisions to maintain accuracy and precision.
Best Practices for Maintaining High Levels of Accuracy and Precision
Achieving accuracy and precision in inventory and order management is an ongoing process. Here are some best practices to help you maintain these high standards:
Continuous Training and Development for Staff
Regular training ensures your staff stays updated on the best practices for inventory management. Continuous development programs reinforce the importance of accuracy and precision, leading to more consistent performance.
Regular Review and Optimization of Inventory Processes
Periodically review your inventory processes to identify areas for improvement. Optimization efforts, such as refining your picking methods, helps maintain high levels of accuracy and precision.
Investing in the Right Technology and Tools
Investing in the right technology, such as advanced inventory management software and barcode scanning systems, is crucial for maintaining accuracy and precision. Ensure that your tools are up-to-date and can support your inventory management needs.
Monitoring and Analyzing Key Performance Indicators (KPIs)
Regularly monitor and analyze KPIs related to accuracy and precision, such as inventory turnover rates, order fulfillment accuracy, and stock discrepancy rates. These metrics provide valuable insights into your inventory management performance and help you identify areas for improvement.
Achieving accuracy and precision in inventory and order management is critical for smooth operations, customer satisfaction, and business success. You can create a reliable and efficient inventory management system by understanding the importance of these concepts, addressing common challenges, and implementing effective strategies. Remember, continuous improvement and the right technology are vital to maintaining high levels of accuracy and precision. Embrace these best practices and watch your inventory and order management processes thrive.
Call us at 817-870-1311