Boost Accuracy with Barcoding Technology
Built For
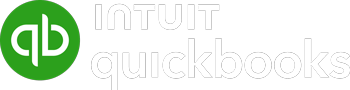
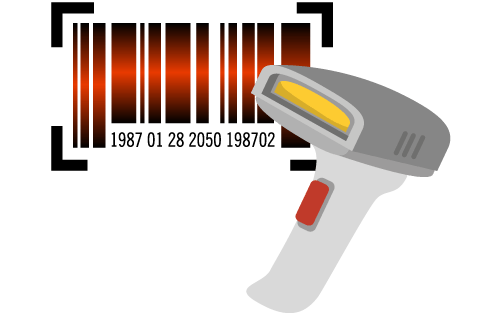
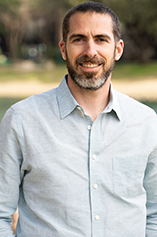
Boost Accuracy with Barcoding Technology
Accuracy is more than just a desirable trait—it’s a necessity. Whether you’re managing inventory, processing orders, or tracking shipments, even a small mistake can lead to costly repercussions. This is where barcoding technology comes into play, offering a powerful solution to ensure precision across all your operations.
Barcoding technology has transformed how businesses handle data, reducing errors and increasing operational efficiency. From ensuring accurate inventory counts to ensuring the right products are shipped out on time, barcoding is an essential tool for businesses looking to maintain high levels of accuracy.
In this article, we’ll explore how barcoding technology can help your business boost accuracy in every aspect of your operations. We’ll dive into barcoding technology, how it works, and how it can improve the accuracy of your inventory management, order fulfillment, and data-tracking processes. So, let’s get started and discover why barcoding technology might be the key to taking your business to the next level.
Understanding Barcoding Technology
Let’s start with the basics—what exactly is barcoding technology? You’ve probably seen barcodes everywhere, from the grocery store to the packages you receive from online orders. A barcode is simply a visual representation of data. It is typically a series of black-and-white lines that hold all sorts of information about the product they’re attached to, like a secret code that only scanners can read.
Now, let’s discuss the tools of the trade. Businesses use barcode scanners to decode these barcodes. Barcode devices come in all shapes and sizes, from the classic handheld scanners you see at checkout counters to mobile devices that warehouse workers use to keep track of inventory. The beauty of barcoding technology is that it’s super versatile and can be integrated into almost any part of your business operations.
So, why does this matter? By using barcodes, you can streamline data entry and reduce the chances of human error. Instead of manually typing in product details (and possibly making a typo), you scan the barcode, and all the information you need is instantly captured and processed. This speeds things up and ensures that the data you’re working with is accurate and up-to-date.
How Barcoding Technology Improves Accuracy
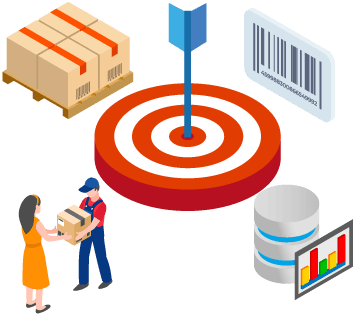
So, you know what barcoding technology is and how it works—now let’s get into the nitty-gritty of how it boosts your business accuracy. Barcoding can seriously level up your operations from inventory management to order fulfillment. Here’s how:
Inventory Accuracy
Keeping track of hundreds (or thousands) of products in your inventory manually sounds like a nightmare, right? That’s where barcoding comes in.
With barcodes, every item in your inventory is tagged with a unique identifier. When you scan a barcode, the system automatically updates your inventory records in real time. This means you always know exactly how much stock you have without second guessing or going on a wild goose chase through the warehouse. Say goodbye to stock discrepancies and hello to accurate inventory counts!
Order Accuracy
Have you ever ordered something online and received the wrong item? Frustrating, isn’t it? Imagine being on the other side of that—sending out the wrong order to a customer. That’s a surefire way to lose repeat business.
Barcoding technology helps you avoid this by ensuring that the right items are picked, packed, and shipped to the customer every time. When you scan a product’s barcode during the picking process, the system confirms that it matches the customer’s order. It’s like having a built-in quality control system that catches mistakes before they happen.
Data Accuracy
Let’s face it—data entry errors are bound to happen when relying on humans to manually input information. But with barcoding, you can automate data capture, making it more accurate and reliable. Every scan directly inputs data into your system, eliminating the risk of typos or misreads. Plus, all that data is centralized, so you always have a clear, consistent view of what’s going on in your business. Whether tracking inventory levels, monitoring sales, or keeping tabs on shipments, barcoding ensures your data is spot-on.
Barcoding technology takes the guesswork out of your operations. It gives you the tools to maintain high accuracy across your inventory, orders, and data—so you can run your business more efficiently and keep your customers happy.
Implementing Barcoding in Your Business
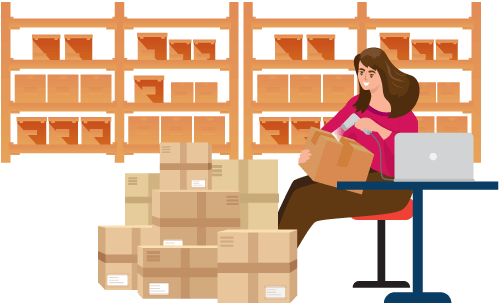
Ready to jump on the barcoding bandwagon? Great choice! But before you dive in, there are a few things to consider to ensure your barcoding implementation goes off without a hitch. Here’s a step-by-step guide to getting barcoding up and running in your business.
Step 1: Start with Your Inventory and Order Management System
One of the best things about barcoding technology is how easily it integrates with inventory and order management software. Once integrated, barcoding can automatically update your inventory and assist with processing orders without lifting a finger. So, step one is to determine the requirements for adding barcoding to your inventory software.
Step 2: Purchase Your Barcode Technology
First, you’ll need to decide on the type of barcoding scanners you need. The scanners must work with your inventory software, and you’ll need to determine whether stationary handheld scanners or mobile devices work best for your warehouse team.
Step 3: Implement Barcoding in the Warehouse
With your barcode technology in hand, it’s time to put it to work in the warehouse. Start by labeling all existing inventory with barcodes, ensuring each item is appropriately tagged and recorded in your inventory system. This process might take some time, but it’s crucial for laying a solid foundation.
Next, integrate barcoding into your everyday warehouse processes, like receiving new stock, picking items for orders, and performing regular inventory counts. By making barcoding an integral part of your warehouse operations, you’ll create a more efficient and accurate workflow that reduces errors and speeds up tasks.
Step 4: Set Up Standard Operating Procedures (SOPs)
Establishing Standard Operating Procedures (SOPs) for barcoding ensures smooth operation. These could include guidelines on labeling new inventory, performing inventory counts frequently, and handling discrepancies. Clear SOPs will help your team know exactly what to do in any situation, minimizing errors and ensuring consistency.
Step 5: Train Your Team
Barcoding technology is user-friendly, but you’ll still want to train your team to make the most of it. Whether it’s learning how to properly scan items, understanding what to do if a barcode won’t scan, or troubleshooting issues, a little training goes a long way.
Step 5: Maintain Your Barcodes
Barcodes are durable, but they’re not invincible. Over time, they can get damaged or fade, especially in rough environments. Regularly checking your barcodes’ quality and replacing worn-out labels will help keep your system running smoothly. It’s also a good idea to monitor your scanners and ensure they’re well-maintained and working properly.
By following these steps, you’ll be well on your way to successfully implementing barcoding in your business. Not only will you boost accuracy, but you’ll also streamline your operations, making everything more efficient and less prone to error.
Call us at 817-870-1311