Consistent Data – The Key to Successful Inventory Management
Built For
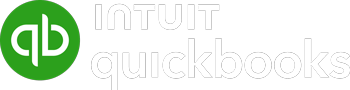
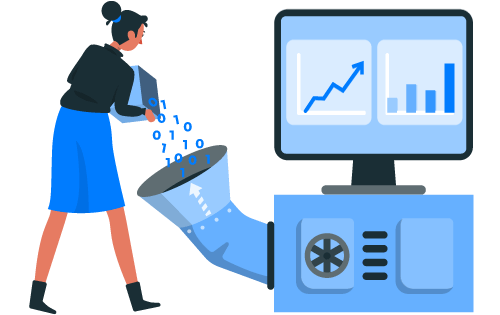
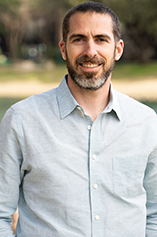
Consistent Data – The Key to Successful Inventory Management
Imagine running a tight ship where all inventory is perfectly accounted for, orders are fulfilled without a hitch, and your customers are always satisfied. It may sound like a dream, but it is possible, or at least closer to attainable than you may think.
Consistent data is a crucial element of a seamless operation. In the world of inventory management, having accurate and reliable data isn’t just a nice to have—it’s essential. Without it, you risk stockouts, overstock situations, and a whole lot of operational headaches.
Today, we discuss why consistent data is the cornerstone of successful inventory management. We’ll explore what consistent data means, the pitfalls of inconsistency, and practical strategies to keep your data in check. Plus, we’ll look at how the right inventory management software can make all the difference.
Understanding Consistent Data
Consistent data in inventory management means ensuring that every piece of information regarding your inventory is accurate, reliable, and up-to-date. It means that the data you have on hand—such as stock levels, product descriptions, locations, and order statuses—matches the reality of your inventory at any given time.
Consistent data is the backbone of your inventory system. When your data is consistent, you can trust that the numbers you see on your screen reflect what’s actually in your warehouse. Trust is vital for making informed decisions, planning accurately, and running your operations smoothly.
Examples of Consistent vs. Inconsistent Data
To illustrate the difference, let’s look at a couple of scenarios.
Consistent Data | Inconsistent Data | |
Stock Levels | Your system shows 100 units of a product in stock. You check the warehouse, and indeed, there are 100 units on the shelf. | Your system shows 50 units of a product in stock, but when you go to fulfill an order, you find only 20 units available. Now, you have to deal with backorders and customer dissatisfaction. |
Order Status | An order placed by a customer is marked as shipped in your system. The tracking number shows the package is on its way to the customer. | An order is marked as fulfilled in your system, but the customer contacts you saying they never received it. After investigating, you find the order was never shipped out. |
Product Descriptions | The dimensions and weight of a product in your system match exactly with the physical product, ensuring shipping costs are calculated correctly. | The weight of a product is incorrectly entered, leading to higher-than-expected shipping costs and potential disputes with customers. |
Inconsistent data can stem from various sources, such as manual entry errors, delayed updates, or lack of synchronization between systems. Regardless of the cause, the impact is often significant, leading to inefficiencies, increased costs, and unhappy customers.
Understanding the importance of consistent data is the first step toward mastering inventory management. Consistent data can build trust and reliability, paving the way for smoother operations and better decision-making.
The Impact of Inconsistent Data
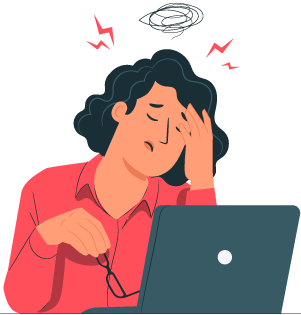
Inconsistent data can wreak havoc on your inventory management process, leading to a cascade of problems that affect every aspect of your business. Let’s delve into some of the most common issues caused by inconsistent data and how they can impact your operations.
Stockouts and Overstock Situations
When your inventory data is inconsistent, it becomes nearly impossible to maintain accurate stock levels. This can lead to stockouts—when you run out of a product and cannot fulfill customer orders. Stockouts result in lost sales and damage your reputation and customer trust. On the flip side, overstock situations occur when your system indicates a need for replenishment, but you already have ample supply on hand. This ties up capital in excess inventory that could be used elsewhere in your business.
Errors in Order Fulfillment
Inconsistent data can cause significant errors in order fulfillment. For example, if your system shows that a product is available when it isn’t, you may take orders you can’t fulfill. This results in delayed shipments, backorders, and dissatisfied customers. Alternatively, if your system indicates that a product is out of stock when it’s not, you miss out on potential sales opportunities. These errors undermine customer confidence and can lead to increased customer churn.
Inaccurate Forecasting and Planning
Effective inventory management relies heavily on accurate data for forecasting demand and planning inventory replenishments. Inconsistent data skews your forecasts, making it difficult to predict future inventory needs accurately. This can lead to either understocking or overstocking, and, as we have discussed, both have financial repercussions. Accurate forecasting is crucial for maintaining a balanced inventory, optimizing storage space, and minimizing holding costs.
Reduced Customer Satisfaction
Customers expect orders to be fulfilled quickly and accurately. When your inventory data is inconsistent, it increases the likelihood of order errors, delays, and out-of-stock notifications after purchase. Each of these issues chips away at customer satisfaction. In today’s competitive market, even a single negative experience can turn a repeat customer into a lost one. Ensuring consistent data helps you meet customer expectations and maintain high satisfaction levels.
Increased Operational Costs
Inconsistent data can lead to operational inefficiencies that drive up costs. For example, frequent stockouts may require expedited shipping to meet customer demands, while overstock situations increase storage and carrying costs. Moreover, the time and resources spent on resolving order errors, handling customer complaints, and conducting manual inventory counts add to operational expenses. Maintaining consistent data can streamline your operations and reduce these unnecessary costs.
Inconsistent data can have a far-reaching impact and significantly hinder a business’s success. Recognizing these issues and taking steps to ensure data consistency is crucial for maintaining efficient operations and delivering exceptional customer experiences.
Strategies for Ensuring Data Consistency
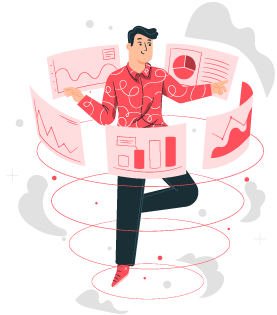
A proactive approach and effective strategies are required for maintaining consistent data in inventory management. Here are some practical steps you can take to ensure data consistency and keep your inventory management process running smoothly.
Leveraging Technology to Automate and Streamline Data Processes
Automation is a powerful tool for maintaining data consistency. Automating data entry, stock-level updates, and order processing reduces the likelihood of human error. Inventory management software with automation capabilities can help streamline these processes and ensure your data remains accurate and up-to-date.
Regular Audits and Data Verification
Conducting regular audits and data verification processes is crucial for maintaining data accuracy. Schedule periodic reviews of your inventory data to identify and correct discrepancies. This might involve physical inventory counts, where you compare actual stock levels with system records, and data reconciliation, where you match your inventory records with sales and purchase data.
Training Staff on Data Entry Best Practices
Your team is a key factor in maintaining data consistency. Ensure that all employees involved in inventory management are trained on best practices for data entry and understand the importance of accurate data, how to correctly enter and update data in the system, and the procedures for reporting and correcting errors. Regular training sessions help reinforce these practices and keep everyone aligned.
Establishing Standardized Procedures
Standardized procedures for data entry and inventory management are essential for consistency. Create detailed guidelines for recording, updating, and verifying data. Ensure that these procedures are documented and easily accessible to all relevant staff. Standardized procedures help ensure that everyone follows the same steps, reducing variability and errors in data handling.
Regularly Updating and Maintaining Inventory Records
Consistent data requires ongoing maintenance and updates. Make it a priority to review and update your inventory records regularly. This might include adding new products, removing obsolete items, and adjusting stock levels based on recent transactions. Keeping your records current ensures that your data reflects the actual state of your inventory.
Conducting Periodic Reviews and Reconciliations
Periodic reviews and reconciliations are essential for catching and correcting inconsistencies. Schedule regular intervals to review and compare your inventory data with physical counts and transaction records. Reconcile any discrepancies promptly to prevent them from compounding over time. This proactive approach helps maintain data accuracy and prevents minor errors from becoming bigger issues.
Establishing a Data Governance Framework
A data governance framework can provide a structured approach to data consistency management. This framework should outline roles and responsibilities, data standards, and policies for data management. Create a culture of accountability and accuracy by clearly defining how data should be handled and who is responsible for maintaining it.
Ensuring data consistency is a continuous effort requiring a combination of technology, processes, and people. Implementation of these strategies can significantly reduce the risk of data inconsistencies and create a reliable foundation for your inventory management operations.
The Role of Inventory Management Software in Achieving Consistent Data
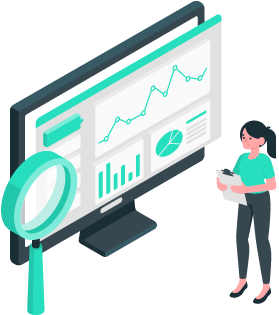
Inventory management software is crucial in ensuring data consistency, offering a range of features and capabilities designed to keep your inventory data accurate and up-to-date. Let’s explore how inventory software helps maintain data consistency and highlight some key integration points, including QuickBooks, eCommerce platforms, EDI systems, and barcode technology.
Real-Time Data Updates
A key benefit of inventory software is its ability to provide real-time data updates. This means that the system immediately reflects these changes every time an inventory-related action occurs—such as a sale, return, or stock adjustment. Real-time updates ensure that your inventory records are continually current, reducing the risk of errors and discrepancies.
Centralizing Data from All Sales Channels
In today’s multi-channel retail environment, having a centralized system consolidating data from all your sales channels is crucial. Inventory management software aggregates orders and customer data from eCommerce platforms, online marketplaces, EDI transactions, and direct sales. Centralizing this data provides several benefits:
- Unified View of Inventory: A centralized system provides a single source for your inventory, sales, and customer data, making it easier to track stock levels, monitor sales performance, and manage replenishments across all channels.
- Improved Decision-Making: With all your sales data in one place, you can gain better insights into your business operations. This comprehensive view allows for more accurate demand forecasting, inventory planning, and strategic decision-making.
- Enhanced Customer Experience: Consistent and accurate data across all channels ensures that customers receive reliable information about product availability. This consistency improves the customer experience, reduces the likelihood of stockouts or backorders, and fosters customer loyalty.
Integration Capabilities
Effective inventory management software can integrate seamlessly with other critical systems, helping maintain data consistency across your business. Here are some key integration points:
QuickBooks Integration: Inventory management software integrated with QuickBooks ensures that your financial and inventory data are synchronized. QuickBooks integration allows for automatic updates to your accounting records whenever inventory levels change, sales are made, or purchases are received. Keeping your financial and inventory data aligned can reduce manual data entry, minimize errors, and streamline your accounting processes.
eCommerce Integration: Connecting your inventory management software with online marketplaces and eCommerce platforms like Shopify, WooCommerce, or Magento, is essential for online businesses. eCommerce integration ensures inventory levels are updated across all your sales channels. When an order is placed, the inventory management system adjusts stock levels, reducing the risk of overselling or stockouts. Centralizing your eCommerce data helps you maintain accurate inventory records and provides a unified view of your online sales performance.
EDI Integration: Electronic Data Interchange (EDI) facilitates the automated exchange of business documents between your system and your trading partners. Integrating EDI system with your inventory management software allows seamless order processing, invoicing, and shipment notifications. EDI integration reduces manual data entry, speeds up transactions, and ensures that your inventory data remains accurate and consistent, particularly beneficial for businesses dealing with large volumes of orders or working with major retailers.
Barcode Technology Integration: Barcoding technology significantly reduces human error and improves data consistency. Scanning barcodes during inventory movements ensures data is captured accurately and automatically, speeding up the process and minimizing the risk of errors.
Customizable Dashboards and Reporting
Inventory management software’s customizable dashboards and reporting tools allows you to tailor the display of critical inventory metrics to your specific needs. Real-time dashboards provide instant access to key performance indicators (KPIs), while detailed reports can help you identify issues, analyze trends, and make informed decisions. Customizable dashboards and reports ensure you have the correct information at your fingertips to maintain data consistency and drive business success.
By leveraging inventory management software’s capabilities, you can achieve and maintain data consistency across your entire inventory management process. Integrations with systems like QuickBooks, eCommerce platforms, and EDI, combined with centralizing data from all sales channels, create a robust foundation for accurate and reliable inventory management.
Call us at 817-870-1311