Improving Operational Efficiency
Built For
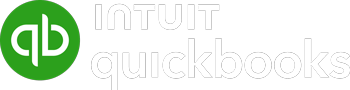
Improving Operational Efficiency
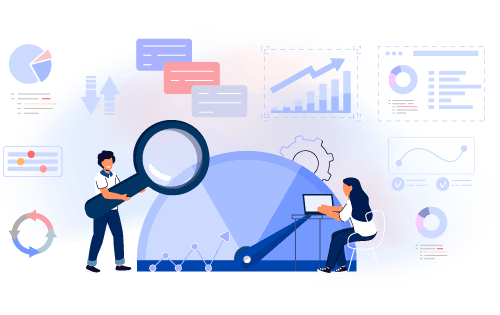
Operational efficiency is core to any thriving business. It’s not just about doing things faster but about optimizing every aspect of your operations to deliver better value to your customers and stakeholders. Operational efficiency is about maximizing your resources, reducing waste, and boosting productivity. When your operations run smoothly, everything from your bottom line to customer satisfaction gets a positive lift.
Whether you manage a small business or oversee a large enterprise, improving operational efficiency leads to significant cost savings, enhanced productivity, and a more agile response to market demands.
Next in The Series: Improving Operational Efficiency
The next articles in our Benefits of Inventory Management series focus on helping you improve operational efficiency in your business. We’ll cover everything from the nuts and bolts of inventory receiving to leveraging mobile devices for better inventory management. Whether you’re a small business owner or a seasoned operations manager, there’s something here for everyone looking to fine-tune their operations.
Improving Operational Efficiency in the Inventory Receiving Process
Efficient inventory receiving is crucial for accurate inventory management. In, The Inventory Receiving Process, we’ll guide you through best practices such as organizing your receiving area, using barcodes and scanners for quick data entry, and implementing a robust inspection process to ensure the accuracy and quality of received goods. We’ll also discuss how to update your inventory records in real time to maintain accurate stock levels.
Faster Order Fulfillment
Speeding up order fulfillment leads to happier customers and repeat business. Here, we’ll explore strategies like optimizing warehouse layout for faster picking, using automation tools to streamline order processing, and employing batch-picking techniques. Additionally, we’ll cover how to use software to manage orders efficiently from multiple sales channels.
Improving Inventory Management Efficiency with Mobile Devices
Mobile devices can transform inventory management, providing real-time updates and reducing errors. Mobile Inventory Management discusses the advantages of using handheld devices for inventory counting, order picking, and stock adjustments.
Inventory Threshold Alerts
Inventory Threshold Alerts help you avoid the pitfalls of overstocking or running out of stock. We’ll explain how to determine appropriate threshold levels for your products, set up automated alerts in your inventory management system, and respond promptly to these alerts to maintain optimal inventory levels.
Quick Purchase Orders
Generating purchase orders quickly and accurately is essential to keep your supply chain running smoothly. Quick Purchase Orders covers how inventory management software helps to create and manage purchase orders efficiently.
Real-Time Inventory Tracking
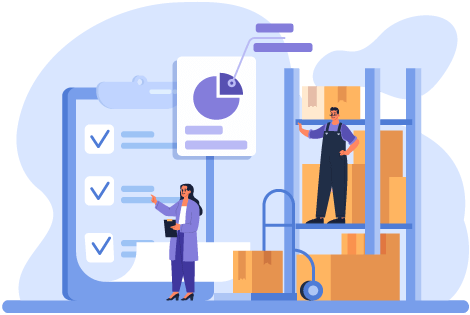
Real-time inventory tracking provides a current view of your stock levels, crucial for making informed decisions. We’ll explore how barcoding and inventory management software can help you achieve real-time tracking and seamless data flow.
Quick Access to Inventory and Order Information
Quick access to inventory and order information can significantly enhance operational efficiency. We’ll explore systems and practices that ensure your team can access up-to-date information on stock levels, order statuses, and customer details.
Conducting Operational Analysis
Operational analysis involves evaluating your processes to identify areas for improvement. We’ll guide you through the steps of conducting an operational analysis, including how inventory software provides visibility and insights that can assist with identifying bottlenecks and using key performance indicators (KPIs) to measure performance.
Reducing or Eliminating Time-Consuming Tasks in Inventory and Order Management
Identifying and eliminating time-consuming tasks can save valuable time for more productive activities. We’ll discuss common time-wasting tasks in inventory and order management and provide tips on streamlining or automating tasks and optimizing workflows.
Picking Efficiency
Picking efficiency is crucial for faster order fulfillment. Improving Picking Efficiency covers techniques such as zone picking, batch picking, and wave picking, as well as using smart picklists that can enhance accuracy and speed.
Inventory Dashboard
An inventory dashboard provides a visual representation of your key metrics and KPIs, making it easier to monitor and manage your inventory. We’ll explore the features of an effective inventory dashboard, how to customize it to suit your needs, and the benefits of having a real-time, centralized view of your inventory data.
Monitor Key Performance Indicators (KPIs)
Monitoring KPIs is essential for tracking your operational efficiency and progress. We round out our Improving Operational Efficiency articles with a discussion on the most critical KPIs for inventory management, such as inventory turnover rate, order accuracy, and fill rate, and cover how to set up and track these KPIs using inventory management software.
Call us at 817-870-1311