The Inventory Receiving Process
Built For
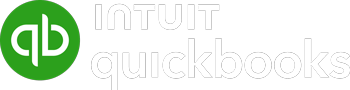
The Inventory Receiving Process
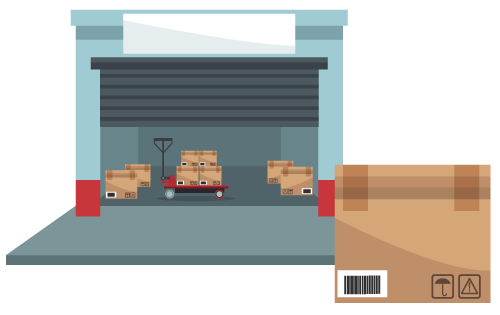
The inventory-receiving process is a critical step that sets the tone for warehouse operations. Ensuring your inventory is received accurately and efficiently significantly impacts overall operational efficiency.
Think of the inventory-receiving process as the gatekeeper of your warehouse. It’s the first point of contact for all incoming goods, and if handled correctly, it can prevent bottlenecks, reduce errors, and save valuable time and resources. But what exactly does an efficient receiving process look like, and how can you achieve it?
In this article, we’ll explore the key components of the inventory-receiving process, examine common challenges, and share best practices for improving efficiency. From automating data entry to optimizing your warehouse layout, we’ll cover practical strategies that can help streamline your operations and boost productivity. By the end, you’ll clearly understand how to transform your inventory-receiving process into a well-oiled machine ready to handle your business’ demands.
Understanding the Inventory Receiving Process
The inventory-receiving process is the foundation of effective inventory management. It involves several steps that ensure incoming goods are accurately accounted for, inspected, and properly stored. Understanding these steps and the common challenges associated with them is crucial for improving operational efficiency.
Critical Components of the Inventory Receiving Process
- Receipt of Goods: This is the first step, when goods arrive at the warehouse or receiving dock. Receiving inventory involves verifying the delivery against the purchase order to ensure the correct items and quantities have been delivered.
- Inspection and Quality Control: After receipt, the goods are inspected for damage or discrepancies. This step ensures that only quality products are added to the inventory, preventing future issues related to faulty goods.
- Documentation and Data Entry: Accurate documentation includes recording the items received in the inventory management system, updating stock levels, and ensuring all relevant paperwork is completed and filed.
- Labeling and Barcoding: Received items are labeled and barcoded to streamline the tracking process. This step simplifies future inventory checks and order fulfillment, making it easy to locate and identify items in the warehouse.
- Storage and Organization: The final step involves moving the received goods to their designated storage locations. Proper organization here ensures that items are easy to find and reduces the time spent locating products during order fulfillment.
Common Challenges in Inventory Receiving
Despite its importance, the inventory-receiving process is often fraught with challenges hindering efficiency. Here are some common issues businesses face:
- Inaccurate Shipments: Receiving goods that don’t match the purchase order in terms of quantity or specifications can lead to delays and additional costs. It’s crucial to have a system to catch these discrepancies early.
- Damage During Transit: Goods can sometimes arrive damaged, affecting inventory levels and customer satisfaction. Implementing a thorough inspection process helps mitigate this risk.
- Manual Data Entry Errors: Relying on manual entry to update inventory records can lead to mistakes that ripple through the entire inventory management system. Automating this process can significantly reduce errors.
- Inefficient Storage Practices: Poor organization in the warehouse can lead to increased time spent locating items, which slows down the entire operation. Optimizing storage practices can save time and improve efficiency.
Understanding these challenges and components is the first step toward streamlining your inventory-receiving process. In the following sections, we’ll explore best practices and technological solutions that can help overcome these challenges and enhance your overall efficiency.
Best Practices for Improving Efficiency
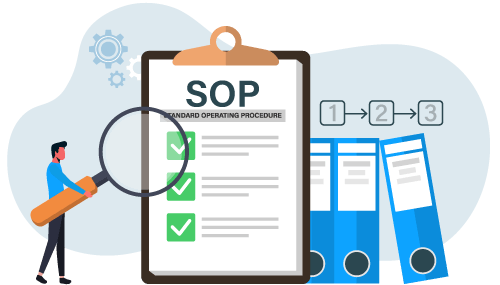
Improving the efficiency of your inventory-receiving process involves implementing best practices that streamline operations, reduce errors, and save time.
Automate Data Entry
Manual data entry is error-prone and time-consuming. Automating this process can significantly increase accuracy and speed. Implementing barcode scanners and inventory management software automates the data entry process, allowing for quick and accurate recording of received goods and reducing the risk of human error.
Implement Standard Operating Procedures (SOPs)
Clear and consistent procedures are essential for an efficient receiving process. SOP examples include detailed checklists for verifying shipments, guidelines for handling damaged goods, and steps for entering data into the inventory system.
- Consistency: SOPs ensure employees follow the same steps when receiving goods, reducing variability and mistakes.
- Documentation: Well-documented procedures make it easier to train new employees and ensure they quickly become proficient in the receiving process.
- Training Staff on SOPs: Regular training sessions and refresher courses help ensure all employees are familiar with and adhere to the established procedures.
Optimize Warehouse Layout
A well-organized warehouse layout can drastically reduce the time spent moving and storing received goods.
- Implement a Logical Flow: Arrange your warehouse to follow a logical flow from receiving to storage. This could mean having staging areas for inspection and labeling before goods are moved to their final storage locations.
- Organize the Receiving Area: Designate a specific area for receiving goods that is easily accessible and close to storage locations, minimizing the distance goods need to be moved.
An optimized layout reduces the time spent handling goods, minimizes the risk of damage during movement, and improves overall efficiency.
Use Real-Time Inventory Tracking
Real-time tracking provides immediate visibility into inventory levels and locations, helping you make informed decisions quickly. Having up-to-date information on inventory levels allows you to swiftly respond to demand changes and avoid stockouts or overstock situations.
Schedule Deliveries Efficiently
Coordinating delivery schedules with suppliers prevents bottlenecks and ensures a smooth receiving process. Work with your suppliers to schedule deliveries at times that minimize disruption to your operations. Avoid scheduling multiple large deliveries at the same time.
Staggering deliveries helps manage workload, prevents overcrowding in the receiving area, and reduces the risk of errors.
Conduct Regular Audits and Inspections
Regular audits ensure that your inventory records match the stock levels, helping identify discrepancies early.
- Using Audit Data: Analyze the data from audits to identify patterns, such as frequently damaged goods or recurring discrepancies, and take steps to address these issues.
- Best Practices for Physical Inspections: Develop a routine for inspecting received goods, checking for damages, and verifying quantities against purchase orders.
Technology Solutions for Enhanced Efficiency
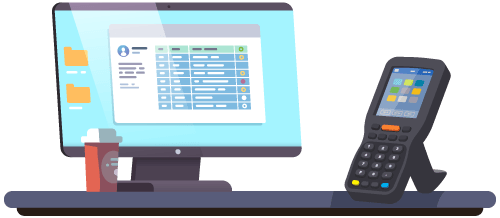
Leveraging the right technology significantly enhances the efficiency of your inventory receiving process.
Inventory Management Software
Inventory management software transforms how you handle inventory receiving.
- Integration with Other Systems: Inventory management systems integrate seamlessly with other business software, such as QuickBooks and eCommerce platforms. This ensures a smooth flow of information across your operations, reducing the need for duplicate data entry and minimizing errors.
- Real-Time Data Updates: Inventory management software provides real-time updates on stock levels as goods are received, ensuring inventory records are accurate and up-to-date and providing immediate visibility helps in making informed decisions quickly and effectively.
- Automated Data Entry: Inventory management software integrated with barcode scanners automates the data entry process, reducing manual errors and speeding up the receiving process.
- Reporting and Analytics: Advanced reporting and analytics help you monitor receiving activities, identify trends, and make data-driven decisions to improve efficiency.
Barcode Technology
Barcode technology is essential for enhancing the accuracy and speed of the inventory-receiving process. Here’s why it’s so effective:
- Quick and Accurate Data Capture: Barcode scanners capture item information quickly and accurately reducing the time spent on manual data entry. Each scanned item is recorded in the inventory management system, documenting the correct items and quantities.
- Error Reduction: Barcodes eliminate the possibility of human error in data entry. This accuracy is crucial for maintaining precise inventory records and ensuring that stock levels reflect the actual items received.
- Efficient Tracking: Barcodes make it easy to track items throughout the warehouse. Each item can be scanned at various points in the receiving and storage process, providing real-time updates to the inventory management system.
Focusing on these two key technologies—inventory management software and barcode technology—can significantly improve the efficiency and accuracy of your inventory receiving process. These tools work together to reduce errors, automate data entry, and provide real-time visibility into your inventory, helping you maintain a streamlined and effective receiving operation.
Call us at 817-870-1311