Improving Order Picking Accuracy
Built For
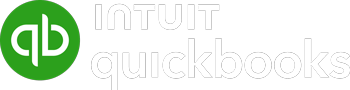
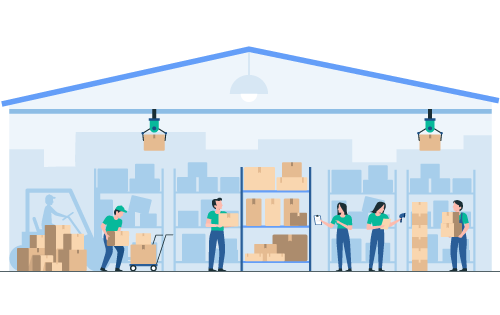
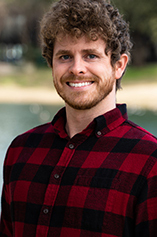
Order Picking Accuracy Improvements
In warehouse operations, accuracy is everything—especially when it comes to order picking. Imagine the frustration of receiving the wrong item or having part of your order missing. It’s not just a hassle for the customer; it’s a potential headache for the business, too. Inaccurate order picking can lead to returns, lost sales, and a hit to your reputation.
But don’t worry—improving order picking accuracy isn’t rocket science. With the right strategies and tools, you can boost your accuracy rates, keep your customers happy, and streamline your operations simultaneously.
Common Challenges in Order Picking
Order picking sounds straightforward—find the item, pick it, and move on to the next. But as anyone in the warehouse knows, it’s not always that simple. Here are some common challenges that can throw a wrench in the works and lead to inaccuracies:
Human Error
No one’s perfect, and mistakes will happen in a bustling warehouse. A picker might grab the wrong item, misread a label, or accidentally skip an item altogether. It’s not intentional, but it can cause big problems down the line, especially if the mistake isn’t caught before the order ships.
Managing Large Inventories
The more extensive your inventory, the harder it is to manage. When you’re dealing with thousands of SKUs, it’s easy for things to get lost in the shuffle. Items might be misplaced, mislabeled, or stored in hard-to-reach places, making it difficult for pickers to locate them quickly and accurately.
Poor Warehouse Layout
A cluttered or poorly organized warehouse can be a nightmare for order picking. If items aren’t stored logically or the aisles are too narrow, pickers can waste valuable time searching for products. This slows down the picking process and increases the likelihood of errors.
Inadequate Technology
Relying on outdated systems or manual processes can lead to inaccuracies. Without the proper technology, it’s harder to track inventory in real time, guide pickers efficiently, or catch mistakes before they happen. The lack of automation can also make it difficult to scale operations as your business grows.
Inconsistent Training
Order picking might seem simple, but all workers need proper training. Inconsistent training leads to inconsistent results, with some pickers excelling while others struggle to keep up. This variation can cause bottlenecks and errors, affecting overall accuracy.
Strategies for Improving Order Picking Accuracy
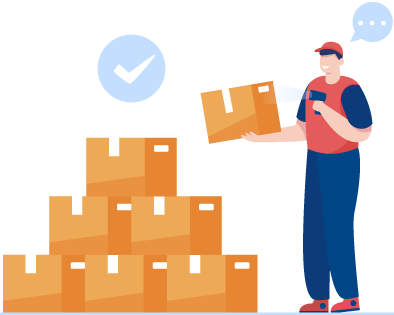
Improving order picking accuracy isn’t just about avoiding mistakes; it’s about creating a system where accuracy becomes second nature. Whether you run a small operation or manage a massive warehouse, these strategies can help you ensure that orders are picked up correctly every time.
Implementing Barcoding Technology
Barcoding is like giving your warehouse a superpower. By scanning barcodes during the picking process, you drastically reduce the chance of human error. Each item is quickly and accurately identified, ensuring the right product gets picked every time. Plus, barcoding technology integrated with inventory management software provides stock tracking in real-time, reducing the risk of picking out-of-stock items.
Optimizing Warehouse Layout
A well-organized warehouse is the backbone of accurate order picking. Start by analyzing your layout and identifying any bottlenecks or areas of confusion. Consider grouping frequently picked items and placing them near the packing area to minimize travel time. Use clear signage and logical labeling to make it easy for pickers to find what they need. The less time they spend searching, the less likely they will make a mistake.
Utilizing Inventory and Order Management Software
Technology is your best friend when it comes to improving accuracy. Inventory and order management software can guide pickers to the exact location of items, provide real-time updates on stock levels, and even alert them to potential errors. By automating these processes, you can ensure pickers always work with the most accurate and up-to-date information, leading to fewer mistakes and faster order fulfillment.
Training and Monitoring
Even with the best tools and layout, your pickers must know how to use them effectively. Regular training sessions keep everyone on the same page, ensuring pickers understand the best practices and the importance of accuracy. But training doesn’t stop after onboarding—ongoing monitoring and feedback are critical to continuous improvement. Use metrics and KPIs to track performance and offer constructive feedback to help pickers improve their accuracy over time.
Best Practices for Maintaining High Accuracy Levels
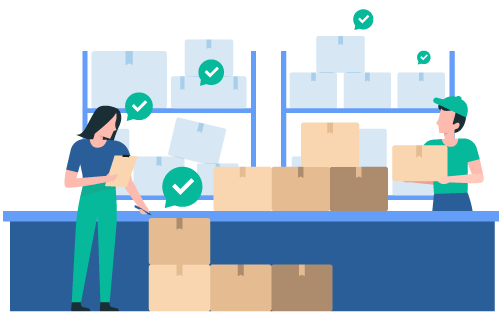
Achieving high accuracy in order picking is a big win, but maintaining that level of precision over time is the real challenge. Here are some best practices to help you keep your accuracy rates high and your customers consistently happy.
Continuous Process Improvement and Regular Audits
The key to maintaining high accuracy is never getting too comfortable with the status quo. Conduct periodic audits to catch any emerging issues before they become major problems. Whether updating your warehouse layout, refining your picking procedures, or tweaking your technology, continuous improvement keeps your operations sharp and efficient.
Set Up Key Performance Indicators (KPIs)
KPIs are your roadmap to success. By setting clear, measurable goals for accuracy, performance can be tracked over time to identify issues that need attention. Some useful KPIs include picking accuracy rate, order error rate, and time spent per pick. Regularly reviewing these metrics allows you to identify issues early and take corrective action before they impact your bottom line.
Encourage a Culture of Accuracy and Accountability
Building a culture that values accuracy starts with leadership. Encourage your team to take pride in their work and understand the importance of getting orders right the first time. Recognize and reward accuracy to motivate your pickers. At the same time, foster a sense of accountability— everyone should know that their role is crucial in ensuring customer satisfaction and operational success.
Invest in Training and Development
Ongoing training is essential for maintaining high accuracy levels. Regular refreshers on best practices, new technology, and process updates keep your team’s skills sharp. Consider implementing a mentorship program where experienced pickers can coach newer team members. The more knowledgeable your team is, the more confident and accurate they’ll be in their work.
Leverage Real-Time Data and Feedback Loops
One of the best ways to maintain accuracy is to use real-time data to inform decisions. With inventory and order management software, you can monitor picking activities as they happen, catching errors before they escalate.
Regularly Maintain and Update Technology
Even the best technology needs some TLC to keep running smoothly. Regularly maintaining and updating your systems ensures they support high accuracy levels. This includes updating software, recalibrating equipment, or simply cleaning barcode scanners. Staying on top of maintenance prevents tech issues from becoming accuracy issues.
Continental D.I.A. Diamond Products, Inc.: Improving Inventory and Order Accuracy
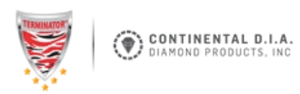
Continental D.I.A. Diamond Products, Inc. (CDIA) was born from the vision and craftsmanship of Vincent Salemi, an Italian immigrant with a passion for working with his hands. What began as a small stone fabrication shop has evolved into a leading company known for delivering innovative and cost-effective tooling solutions. The company’s rise to success is closely tied to its flagship brand, TERMINATOR®, which initially gained recognition through its large circular blades. Over time, the TERMINATOR® brand has expanded globally, offering a comprehensive range of tools for virtually every aspect of the stone fabrication process, including cutting, polishing, and grinding.
CDIA’s journey took a pivotal turn when the company shifted from working with a small number of clients to selling directly to end users. This transition led to rapid growth, expanding their customer base from just 10-15 clients to thousands. With this expansion, CDIA recognized the need for a more robust inventory and order management system.
A Need for Improved Inventory and Order Management
While searching for a solution, CDIA realized that their system, QuickBooks, lacked the necessary inventory and order management features. The company needed a way to accurately control and monitor inventory, conduct year-end counts, and ensure the accuracy of their order management and fulfillment. After extensive research and testing of various software options, CDIA selected Acctivate as their inventory management solution.
Acctivate stood out for its simplicity, logical design, and user-friendly interface. It provided CDIA with the tools to efficiently manage inventory, track sales orders, and fulfill orders with precision. With Acctivate, the team could easily access customer purchase history, invoices, and orders, starkly contrasting the complexity and confusion experienced with other software solutions.
Saving Time and Gaining Accurate, Real-Time Information
Acctivate’s inventory management capabilities have significantly benefited CDIA by saving time and providing accurate, real-time information. The system’s straightforward nature allows the entire team to log on simultaneously, whether working from the main office or remotely. Salespeople across different states can access the system to check product availability, review customer information, and monitor sales.
Moreover, the integration between Acctivate and QuickBooks has streamlined the company’s accounting processes. All the information entered into Acctivate, from order creation to invoicing, is synchronized with QuickBooks, ensuring seamless financial management.
Improving Order Picking Accuracy and Fulfillment Operations
CDIA utilizes Acctivate’s Mobile Inventory Receiving and Mobile Order Picking features to further enhance their operations. These mobile tools allow the company to process 30-50 orders daily more accurately and efficiently. In particular, the mobile order picking feature has reduced human error by enabling employees to verify inventory through handheld devices, ensuring that orders are picked and shipped correctly.
Additionally, integrating Acctivate with UPS and USPS software has simplified the shipping process, saving time by automatically importing shipping information.
CDIA’s adoption of Acctivate has empowered the company to maintain control over its expanding operations, improve accuracy, and continue delivering high-quality products to its growing customer base.
Call us at 817-870-1311