Organize Warehouse Space More Effectively
Built For
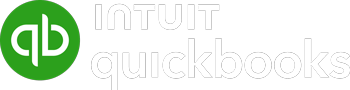
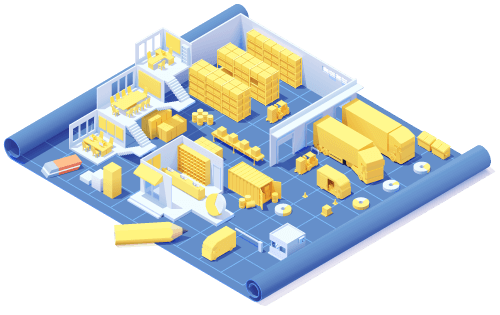
- Assess current warehouse layout
- Implement efficient storage solutions
- Optimize inventory placement
- Leverage technology
- Standardize warehouse procedures
- Regular maintenance and review
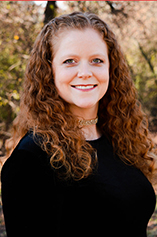
How to Organize Inventory in Your Warehouse Effectively
Running an efficient warehouse is like maintaining a well-oiled machine – everything needs to be in its place and running smoothly. An organized warehouse not only saves time but also boosts productivity, reduces errors, and enhances overall efficiency.
Organizing your warehouse space can make a world of difference. In this article, we’ll explore practical tips and strategies to help you organize your warehouse space more effectively, ensuring a streamlined and efficient operation. Let’s discover how a little organization can go a long way!
Step 1 to Organize Warehouse Space: Assess Current Warehouse Layout
Before diving into any major changes, it’s crucial to understand where your warehouse stands currently. A thorough review of the existing layout will help identify problem areas and inefficiencies. Here’s how you can get started:
- Conduct a Walkthrough: Begin with a comprehensive walkthrough of the warehouse. Take note of areas that seem cluttered, pathways that are obstructed, and items that are hard to find. This firsthand observation will give you a clear picture of what needs attention.
- Collect Data: Gather data on inventory movement and storage. Look at which items are frequently accessed and which ones tend to sit on shelves longer. Understanding these patterns can help you optimize placement and improve accessibility.
- Consult Your Team: Your warehouse staff are the ones working in the space daily, and they can provide valuable insights. Hold a meeting to discuss their observations and suggestions for improvement. They might highlight issues that aren’t immediately obvious.
- Identify Problem Areas: Pinpoint specific problem areas such as congested zones, inefficient storage practices, or safety hazards. Make a list of these issues so you can address them systematically.
- Evaluate Space Utilization: Analyze how your current space is being utilized. Are there areas that could be used more efficiently? Is there unused vertical space that could be better leveraged with higher shelving units?
- Benchmark Against Best Practices: Compare your warehouse layout against industry best practices. Research how similar warehouses organize their space and what technologies or methods they use to maximize efficiency.
By taking the time to assess your current warehouse layout, you’ll have a solid foundation for making informed decisions about how to organize your space more effectively. This proactive approach will pave the way for a more streamlined, productive, and safe warehouse environment.
Step 2 to Organize Warehouse Space: Implement Efficient Storage Solutions and Improve Warehouse Flow
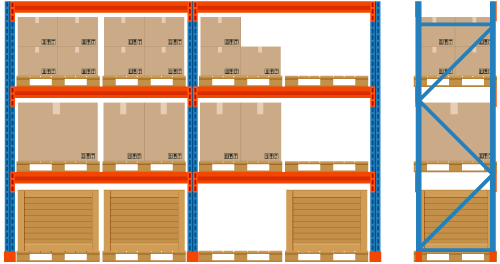
Once you’ve assessed your current warehouse layout, it’s time to implement storage solutions that maximize space and improve efficiency. Here are some practical strategies to consider:
Utilize Shelving and Racking Systems
- Invest in high-quality shelving and racking systems that are tailored to your inventory needs. Adjustable shelves can accommodate items of various sizes and help you make the most of your vertical space.
- Consider using pallet racking for large, bulky items and smaller shelving units for lighter, smaller products.
Implement Vertical Storage
- Don’t let valuable vertical space go to waste. Use tall shelving units and mezzanines to store items higher up. Just ensure that frequently accessed items are kept within easy reach.
- Utilize stackable containers and bins to maximize the use of vertical space within your shelves.
Consider Modular Storage Systems
- Small items can easily get lost or create clutter. Organize them into bins and containers that are clearly labeled. This not only keeps them tidy but also makes them easier to locate.
- Consider using color-coded bins to quickly identify categories of items.
Optimize Aisle Widths
Ensure that aisles are wide enough for easy movement of people and equipment but not so wide that they waste valuable storage space. Finding the right balance is key to maintaining an efficient layout.
Implement FIFO/LIFO Storage
Depending on your inventory turnover, consider implementing FIFO (First In, First Out) or LIFO (Last In, First Out) storage methods. This ensures that older stock is used first and helps prevent items from becoming obsolete.
Leverage Mobile Shelving
Mobile shelving units can be moved as needed, offering flexibility and making it easier to reconfigure your warehouse layout. These are especially useful for spaces that need to adapt frequently.
Label Everything
Clearly label all shelves, bins, and storage areas. Use large, easy-to-read labels that include both text and barcodes. This makes it simple for staff to find and return items quickly.
By implementing these efficient storage solutions, you’ll create a more organized and accessible warehouse. Not only will this save time and reduce errors, but it will also create a safer working environment for your team.
Optimize Receiving and Shipping Areas
- Dedicated Zones: Designate specific areas for receiving and shipping. Keep these zones organized and separate from other warehouse activities to prevent congestion.
- Streamline Processes: Implement efficient procedures for receiving and shipping. Use barcode scanners to quickly check in received items and update inventory counts.
Step 3 to Organize Warehouse Space: Optimize Inventory Placement
Proper inventory placement is essential for a smooth and efficient warehouse operation. By strategically organizing where items are stored, you can reduce picking times, minimize errors, and improve overall workflow. Here are some tips to optimize inventory placement:
Group Similar Items Together
- Store similar items in the same area. This makes it easier to find related products and can speed up the picking process.
- Consider grouping items by category, size, or frequency of use.
Use the ABC Inventory Method
Prioritize your inventory using the ABC method, where:
- A-items are high-value items with low sales frequency.
- B-items are moderate-value items with moderate sales frequency.
- C-items are low-value items with high sales frequency.
Place A-items in secure locations and C-items in easily accessible areas. B-items can be placed in between.
Place High-Turnover Items in Accessible Locations
- Identify items that are frequently picked and place them in the most accessible locations. This reduces the time and effort required to retrieve them.
- Keep high-turnover items near packing and shipping areas to streamline the order fulfillment process.
Consider Ergonomics
- Place heavy or bulky items at waist height to reduce the risk of injury and improve handling efficiency.
- Store lighter items on higher or lower shelves, ensuring they are still easy to reach.
Create a Logical Flow
Design your warehouse layout with a logical flow that guides staff through the picking process efficiently. For example, place frequently picked items near the packing area and less frequently picked items further away.
Use Cross-Docking for Fast-Moving Items
For items that move quickly through your warehouse, consider implementing cross-docking. This process involves unloading items from incoming shipments directly into outbound shipments, reducing storage time and handling costs.
Regularly Review and Adjust Placement
- Inventory needs and patterns can change over time. Regularly review your inventory placement strategy and make adjustments as needed.
- Use data from your inventory and warehouse management system to identify trends and optimize placement continuously.
By optimizing inventory placement, you’ll create a more efficient and streamlined warehouse operation. This not only speeds up the picking process but also enhances accuracy, reduces labor costs, and improves overall productivity.
Step 4 to Organize Warehouse Space: Leverage Technology
Leveraging technology is key to optimizing your warehouse operations. By using inventory and warehouse management software alongside barcode hardware, you can streamline processes, increase accuracy, and boost overall efficiency. Here’s how:
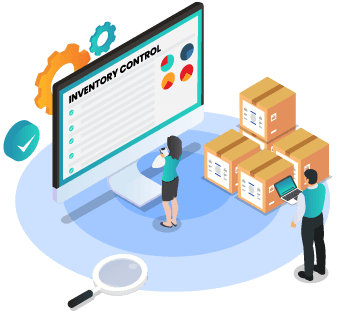
Implement Inventory and Warehouse Management Software
- Track Inventory in Real-Time: Use inventory and warehouse management software to keep track of inventory levels in real-time. This helps prevent stockouts and overstock situations.
- Automate Inventory Updates: Automate the process of updating inventory counts when items are received, moved, or shipped. This reduces manual errors and ensures accuracy.
- Generate Reports and Insights: The software can generate detailed reports on inventory levels, turnover rates, and other key metrics. Use these insights to make informed decisions and optimize inventory management.
Add Barcoding to Your Inventory Software
- Accurate Inventory Tracking: Equip your warehouse with barcode scanners to accurately track the movement of goods. Scanning items as they are received, picked, and shipped ensures precise inventory counts.
- Speed Up Processes: Barcode scanning speeds up the receiving, picking, and packing processes. This not only reduces labor costs but also minimizes the risk of errors.
- Integrate with Software: Ensure that your barcode hardware integrates seamlessly with your inventory and warehouse management software. This integration allows for real-time data updates and improved workflow efficiency.
Enhance Order Fulfillment
- Streamline Picking and Packing: Use technology to create optimized picking routes and packing procedures. This can reduce the time it takes to fulfill orders and improve overall accuracy.
- Automate Reordering: Set up automated reorder points within your software. When inventory levels fall below a certain threshold, the system can automatically generate purchase orders, ensuring you never run out of stock.
Improve Warehouse Layout and Design
- Data-Driven Decisions: Use data from your software to analyze the effectiveness of your warehouse layout. Identify areas for improvement and make data-driven decisions to enhance the flow of goods.
- Simulation and Modeling: Some advanced software solutions offer simulation and modeling tools. Use these tools to test different layout configurations and find the most efficient setup.
Increase Staff Productivity
- Mobile Access: Equip your staff with mobile devices that have access to the inventory and warehouse management software. This allows them to update inventory counts, check stock levels, and complete tasks on the go.
- Training and Support: Ensure that your team is well-trained on how to use the software and barcode hardware. Provide ongoing support and resources to help them utilize the technology effectively.
Enhance Security and Compliance
- Track Inventory Movements: Use the software to monitor and record all inventory movements. This enhances security and helps prevent theft and loss.
- Compliance and Reporting: Ensure that your inventory management practices comply with industry regulations. The software can help generate necessary reports and maintain accurate records for audits.
By leveraging inventory and warehouse management software and barcode hardware, you can significantly enhance the efficiency and accuracy of your warehouse operations. This technology not only streamlines processes but also provides valuable insights that can drive continuous improvement.
Step 5 to Organize Warehouse Space: Standardize Warehouse Procedures & Focus on Staff Training
- Develop Standard Operating Procedures (SOPs): Create and document SOPs for all warehouse tasks, including receiving, picking, packing, and shipping. Standardized procedures ensure consistency and reduce errors.
- Train Staff Regularly: Provide regular training to ensure all staff are familiar with the SOPs. Refresher courses and training for new employees are essential to maintain high standards.
- Implement Cross-Training: Train Staff on Multiple Tasks: Cross-train employees to perform multiple roles within the warehouse. This increases flexibility and ensures that operations can continue smoothly even if some staff are absent.
- Rotate Roles: Regularly rotate staff through different tasks to keep them engaged and reduce monotony.
- Gather Feedback: Regularly solicit feedback from warehouse staff on workflow processes. They can provide valuable insights into areas that need improvement.
- Monitor and Adjust: Use data and feedback to continuously monitor and adjust workflows. Implement changes incrementally and assess their impact before making further adjustments.
Step 6 to Organize Warehouse Space: Regular Maintenance and Review
Maintaining an organized and efficient warehouse requires ongoing effort and regular reviews. Implementing a consistent maintenance and review schedule ensures that your warehouse remains in top condition and adapts to changing needs. Here’s how to keep things running smoothly:
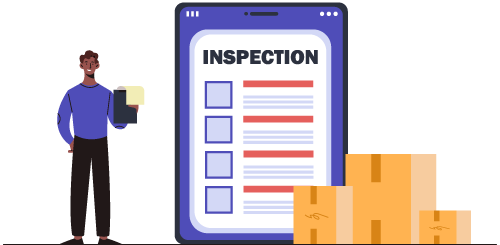
Schedule Regular Clean-Ups
- Daily Tidying: Encourage staff to tidy their work areas at the end of each shift. A clean workspace prevents clutter and helps maintain efficiency.
- Weekly Clean-Ups: Designate a time each week for a more thorough clean-up. This can include organizing shelves, disposing of trash, and cleaning equipment.
Conduct Regular Audits
- Inventory Audits: Perform regular inventory audits to ensure accuracy. Compare physical counts with inventory records and address discrepancies promptly.
- Process Audits: Review warehouse processes periodically to ensure they are being followed correctly and identify any areas for improvement.
Inspect Equipment and Infrastructure
- Equipment Maintenance: Schedule regular maintenance for warehouse equipment such as forklifts, barcode scanners, conveyor systems, and printers. Well-maintained equipment operates more efficiently and safely.
- Infrastructure Checks: Inspect shelving, racks, and other infrastructure regularly for signs of wear and tear. Repair or replace damaged components to maintain safety and efficiency.
Continually Train on Best Practices
- Ongoing Training: Provide ongoing training for staff on organizational best practices and new procedures. Well-trained employees are more efficient and make fewer mistakes.
- Safety Training: Regularly update safety training to ensure staff are aware of best practices and safety protocols.
Solicit Feedback from Staff
- Open Communication: Create an environment where staff feel comfortable providing feedback on warehouse operations. They are often the first to notice inefficiencies or problems.
- Regular Meetings: Hold regular meetings to discuss any issues or suggestions for improvement. Act on feedback to show that their input is valued.
Monitor Key Performance Indicators (KPIs)
- Track KPIs: Monitor key performance indicators such as order fulfillment times, picking accuracy, and inventory turnover rates. These metrics provide insights into the efficiency of your warehouse operations.
- Adjust as Needed: Use the data from KPIs to make informed decisions and adjustments. Regularly review these metrics to ensure continuous improvement.
Adapt to Changes
- Seasonal Adjustments: Be prepared to adjust your warehouse layout and processes for seasonal changes or peak periods. Flexibility is key to maintaining efficiency during high-demand times.
- Evolving Needs: Regularly review your warehouse layout and processes to ensure they meet the current needs of your business. Be willing to adapt and make changes as necessary.
- Review and Reflect: Periodically review the changes and improvements you’ve made. Reflect on what has worked well and what could be improved further.
By committing to regular maintenance and review, you ensure that your warehouse remains organized, efficient, and adaptable. This ongoing effort not only keeps operations running smoothly but also sets the stage for long-term success and continuous improvement.
Call us at 817-870-1311