Acctivate Picklists
Built For
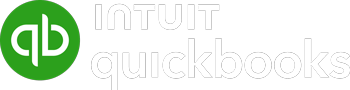
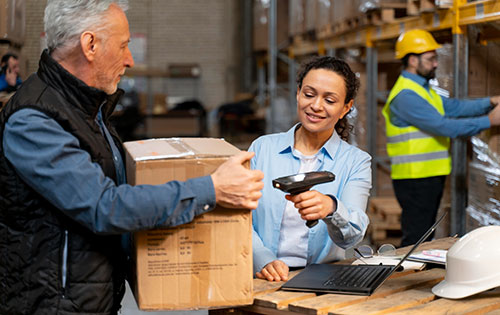
At the heart of the picking and packing process lies a powerful tool: the picklist. A picklist is essentially a detailed guide for warehouse staff, listing the items they need to retrieve to fulfill one or more orders. It’s more than just a list—it’s a roadmap, showing not only what needs to be picked but also where to find it in the warehouse.
Picklists play a crucial role in bridging the gap between sales orders and order fulfillment. Whether you’re managing a small warehouse or a complex multi-location setup, Acctivate Picklists are the key to making your picking and packing process faster, smarter, and more reliable. Once an order is placed, the picklist ensures that the right products are gathered efficiently and in the correct quantities. Picklists allow warehouse staff to streamline the picking process and retrieve products in a logical sequence, minimizing travel time, increasing efficiency, and improving overall accuracy.
Picklists in Action
Imagine a bustling warehouse where orders are flying in, and every second counts. Without the right tools, picking products for these orders can quickly become a logistical nightmare—long treks across shelves, double-checking lists, and risking errors that could lead to customer dissatisfaction. This is where Acctivate Picklists step in, transforming chaos into a well-orchestrated process.
With Acctivate Picklists, warehouse teams work smarter, not harder. Instead of picking each order one at a time, employees can consolidate multiple orders into a single, carefully optimized list. Acctivate maps out the most efficient route through the warehouse, guiding pickers step by step. No more aimless wandering or backtracking—just a clear, straightforward path from product to product.
The result? Orders are picked faster, with less effort, and more accuracy. Acctivate Picklists ensure that each product is picked from the right location, prioritizing availability and proximity. The software does the heavy lifting, calculating the best spots to pull stock from, so pickers don’t have to.
But it’s not just about speed. Accuracy is another hallmark of Acctivate Picklists. They drastically reduce mistakes by providing precise instructions on what to pick and where to pick it from. Fewer errors mean happier customers, fewer returns, and a smoother operation overall.
And the best part? Acctivate Picklists scale with your business. Whether you’re managing a small warehouse or a sprawling multi-location operation, Picklists adapt to fit your needs. Acctivate Picklists are a strategy for success, helping businesses save time, reduce errors, and deliver better service to their customers.
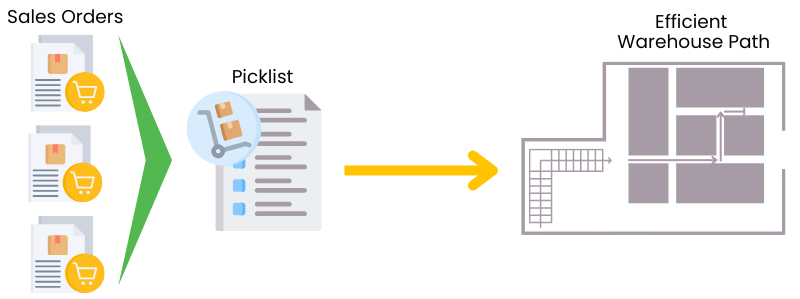
How Acctivate Picklists Work
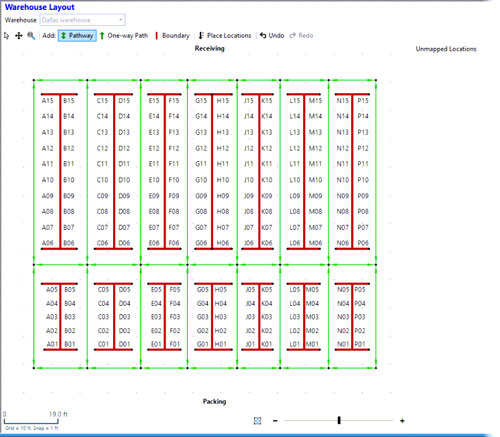
Setting up Acctivate Picklists is like building a foundation for a smoother, more efficient warehouse operation. The process involves a few key steps, but the benefits quickly become apparent once everything is in place.
Picklist Prerequisites
First, imagine your warehouse as a complex map with countless possibilities. The journey begins with enabling the Multiple Locations Module in Acctivate to bring order to this map. This module unlocks the potential to use Picklists, allowing you to organize your warehouse and streamline operations.
How Picklists Assign Locations and Calculate Routes
With multiple locations enabled, you can define and manage the physical layout of your warehouse. Think of it as creating a digital blueprint of your storage areas—bins, shelves, aisles—so the system knows exactly where to direct your pickers.
Location Assignment: Picklists automate the selection of product locations based on:
- Highest or Lowest Availability: Configurable to prioritize locations with the most or least stock.
- Sequence and Proximity: Ensures products are picked in a logical order to reduce travel time.
For instance, if a product is stored in multiple locations, the system will allocate quantities from the most appropriate locations based on the configured priority.
Route Optimization: Acctivate uses advanced algorithms to compute the shortest and most efficient picking route. The system evaluates all locations on the Picklist and sequences them into an optimal path, starting and ending at the packing station. This ensures a circular route that minimizes backtracking.
Stocking Your Inventory
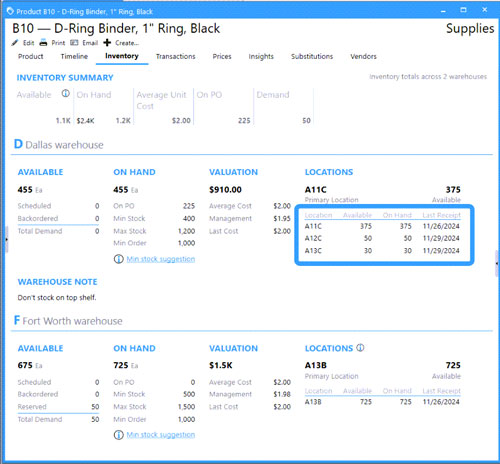
Next comes stocking your inventory. This step requires counting your products and assigning them to specific locations in the warehouse. It’s a bit of legwork upfront, but it ensures every product has a home and every order line can be traced back to its spot. To maintain consistency, you can enable the option to require warehouse locations on all transactions. This way, no detail slips through the cracks.
With the groundwork laid, it’s time to enable Picklists in Acctivate. This feature integrates directly into your workflow, making it easy to generate Picklists from your sales orders and ensuring that the system guides your team smoothly from one action to the next.
Creating a Picklist
Once everything is configured, creating Picklists is a breeze – you simply select orders in the Acctivate Order Manager that are ready to be picked. With just a few clicks, you can group multiple orders into a single Picklist or create one for an individual sales order. The system even gives you options to customize how the Picklist is generated—whether you want to group orders by location or treat them separately.
Once you set up and use Acctivate Picklists, you’ll see how seamlessly they integrate into your order fulfillment process. They’re designed to take the guesswork out of picking, automatically assigning locations, and calculating optimal routes. This level of precision ensures your warehouse operates like a well-oiled machine.
Using Picklists with Acctivate Mobile
With Acctivate Mobile, Picklists come alive. A simple barcode scan pulls up the details of the Picklist, showing exactly what needs to be picked and from where. There’s no need to shuffle through paper documents –the system ensures everything is updated in real time, reducing errors and boosting productivity.
What sets this process apart is the precision and accountability it brings. Once a user starts working on a Picklist, it’s locked to them, ensuring no overlap or confusion. Every step is tracked, and progress is visible, making it easy to monitor operations. It’s like having a personal assistant for every picker, guiding them to the correct locations and ensuring they’re on track.
Completing a Picklist
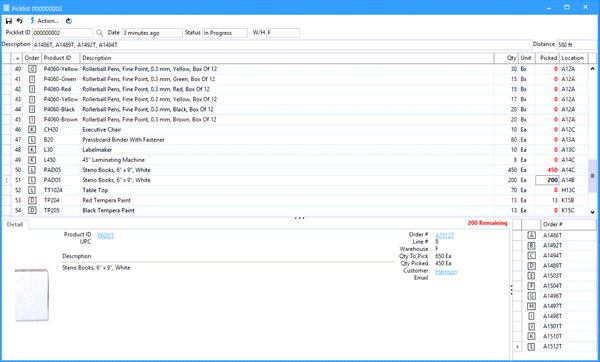
The journey of a Picklist doesn’t end with picking. Once the last item is retrieved from the shelves, it’s time to complete the Picklist and bring everything full circle.
This step is all about accuracy. Before marking the Picklist as complete, workers verify quantities—either confirming what’s been picked or making adjustments as needed. The system ensures that every picked item matches what’s recorded in the sales order. It’s a moment to double-check, correct, and guarantee perfection.
Completing the Picklist is simple but impactful. With a few clicks, the picker updates the status to “Picked.” Behind the scenes, Acctivate adjusts inventory levels, updates the related sales orders, and even automatically places any unpicked items on backorder. It’s a seamless transition that keeps everything running smoothly.
Think of it as the final handshake in the process—tying together the efforts of the warehouse team, the software, and the business as a whole. Completing a Picklist isn’t just a task; it’s the culmination of an optimized system that saves time, reduces errors, and ensures orders are ready for the next step.
Acctivate Picklists provide a smarter way to handle warehouse operations. By automating location assignments, optimizing routes, and consolidating orders, Picklists save time and improve accuracy and are ideal for businesses looking to streamline their workflows and scale their operations.
Call us at 817-870-1311