What is Product Assembly?
Built For
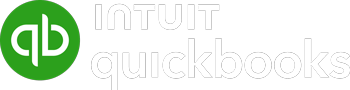
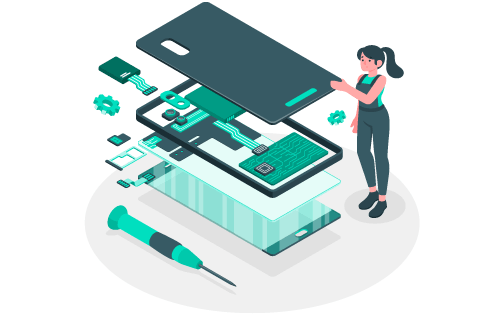
- Assembly process
- Examples of product assembly
- Made to stock vs. made to order
- Managing assemblies in Acctivate
What is Product Assembly?
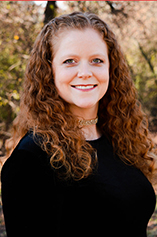
Product assembly is about combining different pieces to create a finished product. Think of product assembly like a puzzle, but instead of pieces of cardboard, you’re working with various product components. These can be as simple as a few screws and boards or as complex as the thousands of parts in a car.
Whether assembling furniture or the latest gadgets, product assembly is vital to bringing products to life.
The Assembly Process
Sourcing and Purchasing Components
The first step in assembly is purchasing your components. You source and receive parts from different suppliers and keep them in inventory. For instance, if you’re making furniture, you might get wood from one vendor, screws from another, and fabric from yet another.
Pre-Assembly
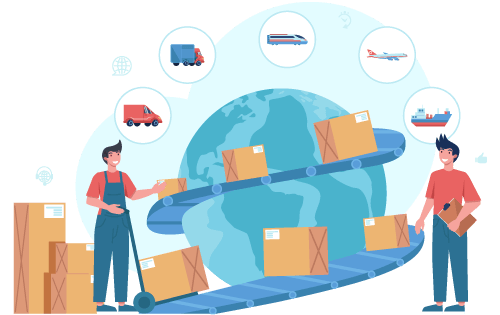
- Bill of Materials (BOM): This is like your shopping list. The BOM details all the components needed for the assembly; without it, you may miss a crucial part.
- Sub-Assembly: Sometimes, smaller parts are put together before the final assembly. It’s like ensuring all your ingredients are prepped before cooking.
- Quality Check: Before assembly, each component should be inspected for defects. This step ensures that everything fits together perfectly and works as it should.
Product Assembly
Once you have all the parts in stock, checked, and prepped, it’s time to start assembling. The magic happens in this stage, transforming individual components into a complete, ready-to-sell product.
Quality Control
After putting everything together, each product should go through a quality check. This step is essential to ensure that everything meets your high standards and specifications. It’s all about keeping your customers happy and minimizing returns.
Packaging and Storage
Once the products pass quality control, they’re packaged, labeled, and stored in your warehouse as part of your finished goods inventory. This step gets your products ready for the final phase.
Order Management and Fulfillment
When a customer places an order—from your website, an eCommerce marketplace, by mail, by fax, or by speaking with one of your representatives—the orders are consolidated in your inventory and order management system, and the inventory quantity is updated.
The finished product is quickly pulled from inventory and shipped out. This is where the Assembly or “Made to Stock” method shines – having products ready to go means you can meet customer demand without delay.
By following these steps, small manufacturers can efficiently manage their production processes and ensure they’re always ready to fulfill customer orders promptly.
Examples of Product Assembly
Electronics Assembly
- Handcrafted Gadgets: Suppose you specialize in handcrafted gadgets, such as custom-built radios or small home automation devices. You’d gather components like circuit boards, casings, and buttons and then assemble them into the final product.
- Lighting: You start with wires, connectors, casings, and lights and put them together to create a functional lighting solution that’s both efficient and stylish. Following assembly, the finished light fixtures are boxed and stored in your warehouse until customers purchase them.
Artisanal Products Assembly
- Jewelry Making: If you make jewelry, the assembly process might involve combining beads, wires, clasps, and other materials to create beautiful, handmade pieces ready for customers to purchase and enjoy.
- Craft Kits: For craft kits, you’d assemble various materials like fabric, thread, needles, and instructions into a neat package that customers can purchase to create their own crafts at home.
Assembly, or Made to Stock, versus Kitting, or Made to Order
There are different approaches to getting products ready for customers in the manufacturing world. As we’ve discussed, “Assembly,” or “Made to Stock,” is one process, while “Kitting,” or “Made to Order,” is also frequently employed. Each has its unique advantages and applications. Let’s break down what these methods entail and how they differ.
Assembly or Made to Stock
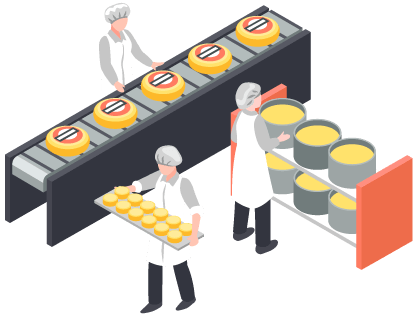
Definition: Assembly, often called “Made to Stock,” involves assembling products from their components in advance and storing them as finished goods. These products are ready to be shipped immediately when a customer places an order.
Advantages
- Quick Response Time: Products are ready for immediate shipment, ensuring fast customer delivery.
- Efficiency: Streamlined production process with consistent product availability.
- Customer Satisfaction: High readiness can increase customer satisfaction due to quick delivery times.
Kitting or Made to Order
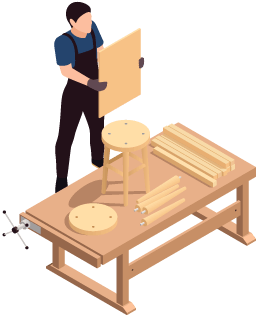
Definition: Kitting, or Made to Order, involves assembling components only after a customer orders. This method is highly customizable and efficient for managing inventory and meeting specific customer requirements.
Advantages
- Customization: Allows products to be tailored to individual customer needs and preferences.
- Inventory Management: Reduces the need for extensive inventories of finished products, as items are assembled on demand.
- Flexibility: Adapts quickly to changes in customer demand and market trends.
Comparison of Assembly and Kitting
Speed vs. Flexibility
- Assembly (Made to Stock): Focuses on speed, with products ready for immediate shipment.
- Kitting (Made to Order): Prioritizes flexibility and customization, assembling products only when orders are received.
Inventory Management
- Assembly (Made to Stock): Requires maintaining an inventory of finished products, which can tie up resources but ensures readiness.
- Kitting (Made to Order): This method maintains an inventory of components instead of finished products, which can be more efficient and cost-effective.
Customer Experience
- Assembly (Made to Stock): Offers quick delivery, appealing to customers who value fast service.
- Kitting (Made to Order): Offers customized products, appealing to customers who value personalization and specificity.
Choosing between Assembly (Made to Stock) and Kitting (Made to Order) depends on your business model, product type, and customer expectations. Small manufacturers might find kitting beneficial for its flexibility and customization, while assembly could benefit businesses by prioritizing quick turnaround times and high product availability. Both methods have their place in the manufacturing landscape, and understanding their strengths can help you make the best choice for your operations.
New Feature in Acctivate for Creating Assemblies
Acctivate has made some cool improvements to make assembling products even easier. We’ve introduced a new process for batch-creating assembly sessions, making it simple to keep your inventory stocked and meet demand without breaking a sweat.
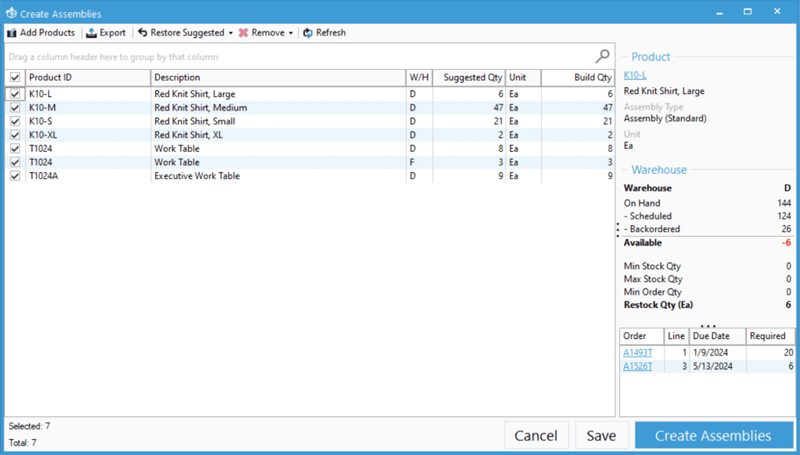
Key Highlights of the New Creating Assemblies Window
Inventory Manager Window
- You start with the new Inventory Manager window. Here, you can see which assembly products are running low and must be replenished.
- Select the suggested products for assembly, or pick any products you want to assemble.
Create Assemblies Window
- This window provides a clear view of your inventory levels and displays which sales orders need the products you’re assembling.
- You can either go with the suggested build quantities or tweak them to better suit your needs.
- Once everything looks good, you create the assembly session for the selected products.
Benefits
- Efficiency: The new Creating Assemblies window streamlines the assembly process, cutting down on manual work.
- Transparency: You get a clear view of what’s in stock and what’s needed, making inventory management a breeze.
- Flexibility: Adjusting build quantities based on current demand helps you stay agile and responsive.
The new assembly creation widow in Acctivate simplifies the assembly process, ensuring your assembly products are always ready to meet customer demand.
Understanding product assembly and leveraging tools like Acctivate, which can simplify both the assembly and kitting processes, significantly boosts your manufacturing efficiency and inventory management. Whether you’re putting together furniture or assembling high-tech gadgets, having the right tools and processes makes all the difference. Happy assembling!
Call us at 817-870-1311