Improving Warehouse Coordination
Built For
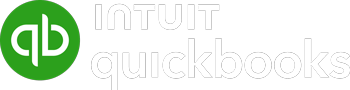
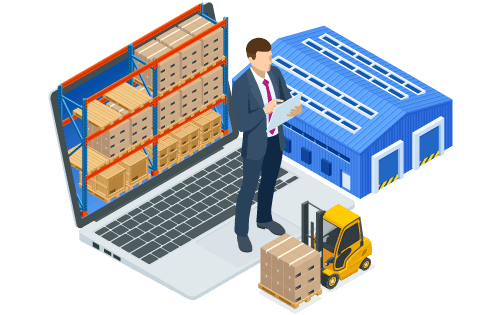
- Importance of warehouse coordination
- Warehouse coordination challenges
- Software solutions for warehouse management
- Real-world example of the transformation of a company’s warehouse operations with inventory software
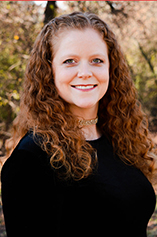
Improving Warehouse Coordination
Efficient coordination in warehouses is the cornerstone of smooth operations and satisfied customers. Orders are processed swiftly, inventory levels are updated in real time, and communication flows seamlessly among team members. This isn’t just a dream scenario; it’s the reality that can be achieved with the right tools and strategies.
Today, we’ll discuss the significance of warehouse coordination and how leveraging advanced software solutions can revolutionize your warehouse management, making it more efficient, accurate, and stress-free.
Understanding Warehouse Coordination
Warehouse coordination involves synchronizing various activities within a warehouse to ensure that operations run efficiently and smoothly. It encompasses managing inventory, overseeing order fulfillment, optimizing space, and providing effective communication among staff.
Effective warehouse coordination is critical for several reasons. First, it enhances productivity by minimizing delays and errors in order processing. When tasks are well-coordinated, staff can work more efficiently, leading to faster turnaround times for receiving, picking, packing, and shipping orders, reducing operational costs and improving customer satisfaction.
Second, proper coordination helps maintain accurate inventory levels. By keeping track of stock movements in real-time, businesses can avoid overstocking or stockouts, both of which can be costly. Accurate inventory data also supports better decision-making and forecasting, enabling companies to plan more effectively.
Finally, good warehouse coordination improves the overall work environment. When everyone knows their role and has the tools they need to perform tasks efficiently, stress is reduced, job satisfaction is enhanced, and staff turnover is lower, leading to a more motivated workforce.
Warehouse coordination is about ensuring all parts of the operation work together seamlessly. It’s the key to boosting productivity, maintaining inventory accuracy, and creating a positive work environment. With the right strategies and tools, such as advanced inventory and warehouse software, achieving effective coordination is well within reach.
Challenges in Warehouse Coordination
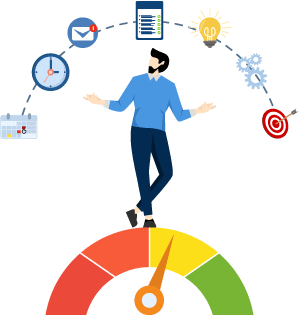
Despite the importance of effective warehouse coordination, numerous challenges can hinder its achievement. Recognizing and addressing coordination issues is critical for maintaining a smooth and efficient warehouse operation. Here are some of the common challenges:
Miscommunication
- Lack of Real-Time Information: Employees can make mistakes without up-to-date information, leading to delays and errors.
- Ineffective Communication Channels: Relying on outdated methods like paper notes or verbal instructions can result in miscommunication and lost information.
Delays
- Inefficient Processes: Manual and repetitive tasks can slow operations, delaying order processing and fulfillment.
- Bottlenecks: Points where tasks pile up in the workflow can cause significant slowdowns, affecting the warehouse’s overall efficiency.
Inventory Inaccuracies
- Incorrect Stock Levels: Inaccurate inventory counts can lead to overstocking or stockouts, both of which are costly.
- Poor Tracking Systems: Without reliable tracking systems, inventory data can easily become outdated or incorrect, leading to further inefficiencies.
Space Utilization
- Suboptimal Layouts: Poorly designed warehouse layouts can lead to wasted space and increased time spent locating items.
- Inefficient Storage: Not effectively using storage space can result in cluttered areas, making it difficult to move goods quickly and safely.
Order Fulfillment Errors
- Picking Mistakes: Errors in picking the wrong items for orders can lead to returns and customer dissatisfaction.
- Packing Errors: Incorrect packing can damage products and increase the likelihood of returns and replacements.
Workforce Management
- Training Gaps: Inadequate training can leave employees unprepared to efficiently handle warehouse systems and processes.
- High Turnover: High employee turnover rates can disrupt operations and increase the time and cost of hiring and training new staff.
These challenges can significantly impact a warehouse’s performance, leading to increased costs, lower customer satisfaction, and a strained workforce. However, with the right strategies and tools, such as inventory and warehouse software, many of these issues can be mitigated, paving the way for smoother, more efficient operations.
How Inventory and Warehouse Software Can Help with Warehouse Coordination
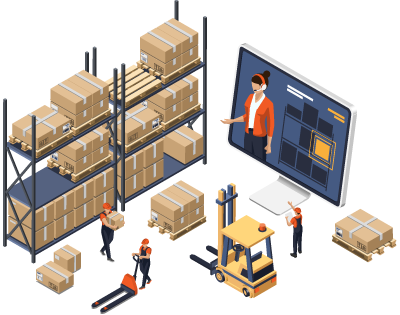
Implementing inventory and warehouse software can address many warehouse coordination challenges, providing a streamlined and efficient operation. Here’s how these advanced tools can make a significant difference:
Enhanced Communication
- Real-Time Updates and Notifications: Warehouse software provides team members access to the latest information, reducing the chances of miscommunication. Notifications about inventory levels, order statuses, and task assignments keep everyone on the same page.
- Improved Communication Channels: The software’s communication tools facilitate direct and clear communication between different departments and staff members, eliminating the need for paper notes or verbal messages.
Inventory Tracking and Management
- Accurate Inventory Counts: Automated inventory tracking reduces the risk of human error, ensuring that stock levels are always correct. This helps prevent overstocking and stockouts, optimizing inventory management.
- Real-Time Tracking: With real-time updates on inventory movements, businesses can track items from the moment they enter the warehouse until they leave. This visibility enhances control over inventory and helps in quick decision-making.
Order Processing Efficiency
- Streamlined Order Processing: The software automates various stages of order processing, from receiving orders to picking, packing, and shipping. This reduces the time taken to fulfill orders and minimizes errors.
- Reduced Errors: Inventory and warehouse management software reduces the likelihood of order processing errors, leading to more accurate and efficient order fulfillment.
Optimized Space Utilization
- Better Organization and Layout Planning: Inventory and warehouse management software provides the data necessary to assist in designing an optimal layout for storage and workflow, ensuring that space is used efficiently. This reduces the time taken to locate and retrieve items.
- Efficient Use of Space: By analyzing inventory data, picking routines and placement strategies can be optimized, maximizing available space and minimizing clutter.
Data-Driven Decision Making
- Analytics and Reporting Tools: Advanced reporting and analytics provide insights into warehouse operations, helping managers identify trends, inefficiencies, and opportunities for improvement.
- Predictive Analytics: The software can use historical data to predict future demand, helping businesses plan inventory levels more accurately and avoid stockouts or excess inventory.
Integration with Other Business Systems and Scalability
- Seamless Integration: Inventory and warehouse software should integrate smoothly with other business systems, such as QuickBooks and eCommerce platforms, ensuring that data flows seamlessly between the systems, reducing manual data entry and minimizing errors.
- Growth Accommodation: The software should be able to scale with your business, handling increased inventory levels, more complex operations, and additional users as needed, ensuring the software remains effective as your business grows.
- Flexible Modules: Scalable software with modular features that can be added or upgraded as needed provides a customizable solution that evolves with your business requirements.
Advanced Reporting and Analytics
- Comprehensive Reports: Detailed reporting tools provide insights into various aspects of warehouse operations, from inventory levels to order fulfillment rates, helping managers make informed decisions and identify areas for improvement.
- Customizable Dashboards: Personalized dashboards allow users access to relevant information and tools for their roles, enhancing efficiency and productivity.
Inventory and warehouse software can significantly enhance the efficiency and effectiveness of warehouse operations. Investing in the right software solution improves productivity, accuracy, and overall business performance.
Case Study: Pigs Unlimited
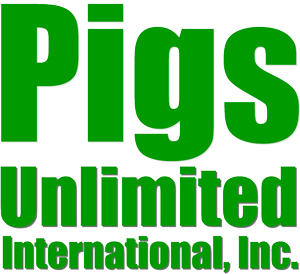
Pigs Unlimited, a pipeline pigs and pigging products manufacturer and distributor, faced significant challenges in warehouse coordination that impacted its operational efficiency. Implementing Acctivate inventory and warehouse software transformed its processes and provided achieved superior synchronization across its business.
Initial Challenges
Pigs Unlimited had separate manufacturing, shipping, and receiving sections and office operations spread across a few suites in a business park. This layout made it difficult to keep all departments in sync. Each shop maintained its own whiteboard to track inventory, which was often outdated and inaccurate. Salespeople had to physically check these boards to give customers accurate quotes, leading to inefficiencies and errors.
Improved Coordination with Acctivate
- Synchronized Operations: Since implementing Acctivate, shop supervisors, office staff, sales teams, and accounting departments work with real-time data, significantly improving communication and coordination.
- Instant Updates: Shop supervisors enter product information as they manufacture items, allowing the sales team to see available stock immediately and provide accurate information to customers. This real-time data flow streamlined operations and reduced delays.
- Preventing Over-Ordering: Acctivate’s purchasing features allow users to see how many items are already on order, preventing double ordering or over-ordering. This visibility ensures resources are used efficiently and reduces unnecessary expenses.
- Accurate Inventory Levels: Acctivate provides detailed information on stock levels, on-hand quantities, expected shipments, and orders in process. Salespeople can provide customers precise quotes without manual inventory checks, enhancing customer service and satisfaction.
- Automated Updates: As soon as items are invoiced, Acctivate automatically updates inventory levels, reducing manual work and errors and ensuring that inventory data is always accurate.
- Streamlined Kitting Processes: Acctivate’s kitting feature automatically adjusts inventory levels when components are used. This automation saves significant time for shop supervisors, allowing them to focus more on production rather than administrative tasks.
- Detailed Bill of Materials: Acctivate stores comprehensive bills of materials for each product, making it easier for salespeople to see all components and available quantities. This feature facilitates accurate inventory management and improves customer service by providing detailed product information.
- Informed Business Decisions: Acctivate’s reporting capabilities provide critical insights into customer preferences, sales trends, and inventory levels. This data helps Pigs Unlimited make informed decisions, optimize their product offerings, and better meet customer needs.
By implementing Acctivate, Pigs Unlimited overcame its coordination challenges and achieved a highly efficient and synchronized operation. Acctivate’s real-time data access, automated processes, and comprehensive reporting tools significantly improved warehouse coordination, enhancing productivity, reduced errors, and better customer satisfaction.
Call us at 817-870-1311