Reducing Warehouse Errors
Built For
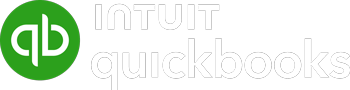
Brad Bearden, Product Manager of Acctivate Inventory Software, shares how inventory software and barcode tech can reduce mistakes, enhance accuracy, and streamline operations.
Reducing Warehouse Errors
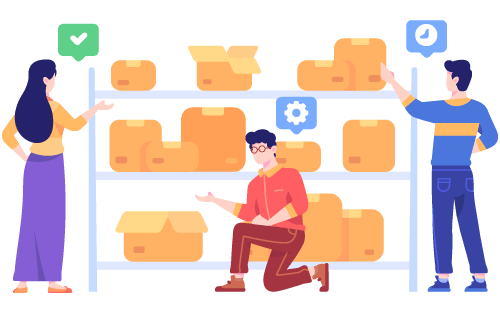
Warehouse errors can feel like a never-ending game of whack-a-mole, constantly popping up and disrupting your smooth operations. These errors can lead to costly mistakes, frustrated customers, and headaches for everyone involved. But it doesn’t have to be this way. By leveraging inventory and order management software paired with barcode technology, you can significantly reduce these errors and streamline your warehouse processes.
Today, we’ll explore how implementing the right systems can help you minimize mistakes, improve accuracy, and boost your overall efficiency. Whether you’re dealing with picking errors, shipping mishaps, or inventory inaccuracies, the right technology can make a world of difference. So, let’s dive in and discover how you can transform your warehouse operations with advanced software and barcode technology.
Common Types of Warehouse Errors
Even the most well-oiled warehouse operations can occasionally run into errors. Understanding common types of errors can help identify and address them more effectively. Here are some of the usual suspects:
Picking Errors
Picking errors occur when the wrong item is selected for an order. This could be due to similar-looking products, misreading labels, or human error. Picking the incorrect item can lead to customer dissatisfaction and increased return rates.
Shipping Errors
Shipping errors happen when an order is sent to the wrong address. This might be due to incorrect labeling, mixing up orders, or miscommunication between departments. Shipping errors incur extra shipping costs and also damage your reputation with customers.
Inventory Mismanagement
Inventory mismanagement errors include discrepancies between actual stock levels and what’s recorded in the system. This could result from improper counting, not recording inventory movements, or system lag. Such errors can lead to stockouts or overstocking, negatively impacting your bottom line.
Labeling and Documentation Mistakes
Labeling and documentation mistakes involve incorrect or missing product labels or paperwork information. These errors can cause confusion, delays in processing orders, and difficulty tracking and managing inventory.
By identifying and understanding these common warehouse errors, you can implement targeted strategies to reduce their occurrence and improve overall warehouse efficiency.
Causes of Warehouse Errors
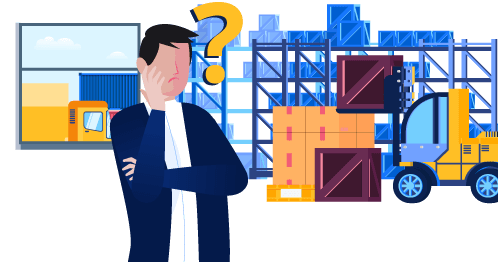
To effectively tackle warehouse errors, it’s crucial to understand the root causes. Here are some common reasons why errors occur in warehouse operations:
Inadequate Training
When warehouse staff are not properly trained, they are more likely to make mistakes. This can include misunderstanding processes, mishandling equipment, or misinterpreting order information. Comprehensive and ongoing training ensures all employees are well-versed in their tasks.
Poor Warehouse Layout and Organization
A disorganized warehouse layout can lead to inefficiencies and mistakes. When items are not stored logically or accessible, employees may struggle to find the correct products, leading to picking errors and delays. A well-organized layout with clear signage and logical product placement can significantly reduce these issues.
Lack of Standardized Processes
Without standardized processes, warehouse operations can become chaotic. Inconsistent procedures can result in errors during picking, packing, shipping, and inventory management. Establishing and adhering to standardized processes ensures operations run smoothly and everyone is on the same page.
Inefficient Communication
Effective communication is vital in a busy warehouse environment. When communication breaks down between team members or departments, errors are more likely to occur. This can lead to miscommunication about orders, incorrect shipments, and overall operational inefficiencies. Implementing robust communication tools and protocols can help mitigate these issues.
Relying on Manual Processes
Relying on manual processes instead of leveraging technology can be a significant source of warehouse errors. Human error frequently occurs with manual data entry, inventory counts, and order processing, leading to inaccuracies and inefficiencies. Without technology, such as inventory management software and barcode systems, tracking inventory accurately, processing orders efficiently, and maintaining up-to-date records becomes challenging. Automating these tasks with advanced software reduces the likelihood of errors, streamlines operations, and frees employees to focus on more strategic activities. By transitioning from manual processes, warehouses can significantly improve accuracy and operational efficiency.
Role of Technology in Reducing Warehouse Errors
Technology plays a crucial role in minimizing warehouse errors and optimizing operations. By focusing on inventory and order management software integrated with barcode technology, warehouses can significantly improve accuracy and efficiency.
Inventory and Order Management Software
Inventory and order management software provides a centralized platform for tracking inventory levels, processing orders, and managing warehouse activities. By automating many manual processes, the risk of human error is reduced, ensuring that data is accurate and up-to-date. Key features include:
- Real-Time Inventory Tracking: The software continuously updates inventory levels as items are received, picked, packed, and shipped. This real-time visibility helps prevent stockouts, overstocking, and other inventory-related errors.
- Order Processing Automation: Orders are automatically processed and prioritized based on predefined criteria, ensuring that the correct items are picked and shipped promptly. The likelihood of shipping errors is reduced and customer satisfaction improved.
- Integrated Reporting and Analytics: The software generates detailed reports and analytics, providing insights into inventory trends, order accuracy, and overall warehouse performance. This data-driven approach enables continuous improvement and error reduction.
Barcode Technology
Barcode technology complements inventory and order management software by providing reliable and efficient tracking of items throughout the warehouse. Key benefits include:
- Accurate Data Entry: Scanning barcodes eliminates the need for manual data entry, significantly reducing the risk of errors. Each scan updates the inventory management system in real time, ensuring that records are always accurate.
- Efficient Picking and Packing: Barcode scanners streamline the picking and packing process by guiding employees to the correct items and confirming that the right products are selected. This reduces picking errors and ensures that orders are fulfilled accurately.
- Improved Inventory Accuracy: Regular cycle counts and audits using barcode scanners help maintain inventory accuracy. Scanners quickly and accurately count items, making it easy to compare physical stock levels with system records and identify discrepancies.
By leveraging inventory and order management software with barcode technology, warehouses can significantly reduce errors, improve accuracy, and enhance overall efficiency. This powerful combination streamlines operations and provides valuable insights for continuous improvement, ensuring that your warehouse runs like a well-oiled machine.
Best Practices for Maintaining Accuracy
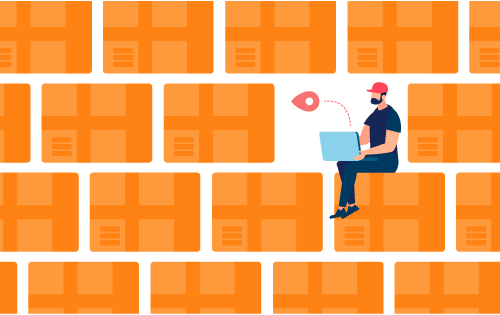
Maintaining high levels of accuracy in your warehouse operations is essential for minimizing errors and ensuring smooth, efficient processes. Here are some best practices to help you achieve and sustain accuracy:
Leveraging Technology and Data Analytics
- Incorporate technology into your warehouse operations to reduce errors.
- Implement inventory and order management software with barcode technology to maintain accurate records, manage stock levels, and streamline workflows.
- Use data analytics to gain insights into your warehouse operations.
- Analyze error patterns, identify root causes, and implement targeted interventions. Data-driven decision-making allows you to proactively address issues and continuously improve your processes.
- Review key performance indicators (KPIs) regularly to monitor progress and adjust strategies.
Optimizing Warehouse Layout
- Design an efficient warehouse layout that minimizes the chances of errors.
- Group similar items together, use clear signage and ensure that frequently picked items are easily accessible.
- Ensure frequently picked items are easily accessible to reduce travel time and minimize picking errors.
- Regularly review and adjust the layout to optimize efficiency.
Regular Audits and Cycle Counts
- Conduct cycle counts and regular audits to verify that your physical inventory matches your system records.
- Schedule checks periodically to catch discrepancies early, address them promptly, and ensure that your inventory data remains accurate and reliable.
- Identify and investigate any discrepancies promptly to prevent errors from escalating.
- Continuously monitor and make adjustments to keep your inventory data accurate and reliable.
Employee Engagement and Feedback Loops
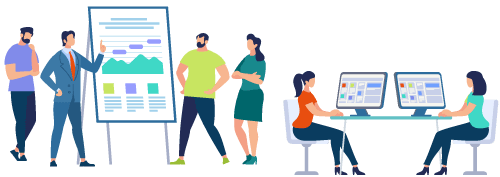
- Empower your employees by providing them the training and tools they need to perform their tasks accurately.
- Implement robust communication tools and protocols to ensure information flows smoothly between team members and departments.
- Holding regular team meetings, providing clear documentation, and the use of instant messaging systems help prevent misunderstandings and ensure everyone is on the same page.
- Solicit feedback from employees on the ground and involve them in identifying areas for improvement.
- Review and refine processes based on feedback and performance data to ensure ongoing optimization and error reduction.
- Encourage a continuous improvement culture in your warehouse.
- Recognize and reward accuracy and address issues promptly to maintain high morale and accountability.
Quality Control Measures
- Introduce quality control measures at various stages of your warehouse operations.
- Double-check orders before they are shipped, verify inventory counts during receiving and conduct spot checks during picking and packing.
Training and Development Programs
- Conduct ongoing training and development programs for your warehouse staff.
- Ensure all employees are well-trained in the correct picking, packing, shipping, and inventory management procedures.
- Keep employees informed about new technologies, processes, and best practices to ensure they are equipped to perform their tasks accurately.
Standardizing Procedures
- Standardize operating procedures to ensure consistency across all warehouse activities.
- Develop clear, step-by-step instructions for receiving, picking, packing, and shipping tasks.
- Ensure that all employees follow these procedures and conduct regular audits to identify any deviations and areas for improvement.
By implementing these best practices, high levels of accuracy in your operations, a reduction in warehouse errors, and overall efficiency can be achieved. Consistent attention to detail and a commitment to continuous improvement will ensure your warehouse runs smoothly and effectively.
Call us at 817-870-1311