What is Order Picking in a Warehouse?
Built For
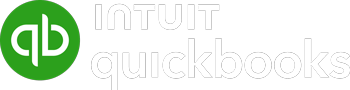
- Different methods of order picking
- The role of inventory software in streamlining the process
- Order picking challenges & best practices
What is Order Picking in a Warehouse?
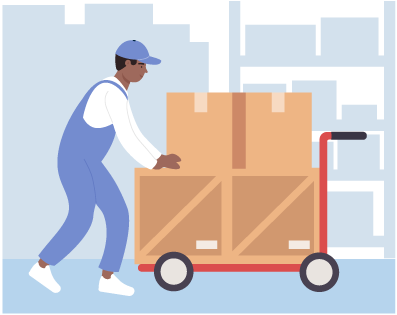
In the heart of every bustling warehouse, a critical process unfolds that is pivotal to customer satisfaction and operational efficiency—order picking. This fundamental activity is where the rubber meets the road in warehouse logistics, determining how swiftly and accurately customers receive their goods. But what exactly is order picking, and why does it command such a crucial role in the supply chain?
Order picking is the process by which goods are selected from inventory and assembled for shipment to fulfill customer orders. It might sound straightforward, but it encompasses many strategies, tools, and systems designed to optimize this complex operation. In an era where multi-channel commerce reigns supreme and the speed of delivery is often as important as the product itself, efficient order picking has become more than a necessity—it’s a competitive differentiator.
This article explores the many aspects of order picking, the different methods warehouses employ, the technologies reshaping their landscape, and the challenges and best practices businesses must navigate.
Understanding Order Picking
So, let’s get down to brass tacks. Imagine you’re online shopping for a new pair of sneakers. You click “Order,” and a warehouse springs into action somewhere. That’s where order picking comes into play. It’s like the warehouse version of a treasure hunt, except the map is an order slip, and the treasure is the products customers eagerly await.
Order picking isn’t just grabbing items off a shelf. It’s the art of navigating a giant puzzle where every piece must fit perfectly into the day’s shipping plan. And it’s not just about speed; it’s about getting the right items in the correct quantity without playing a game of mix-ups that would make your customers’ heads spin.
It happens everywhere—from that giant e-commerce platform delivering gadgets and gizmos aplenty to a small business shipping out orders each day. Accurate order picking is vital to a successful supply chain, and working behind the scenes to ensure what you want ends up in your hands, hopefully as fast as possible.
In the following sections, we’ll break down the types of order-picking methods—because, yes, there are many ways to pick an order—and how technology is making the process more intelligent, faster, and, dare we say, even a little bit fun.
Let’s Talk Order Picking Styles
Grab your picker’s vest and comfy shoes—we’re about to sprint through the fascinating world of order-picking methods. Like a football coach has a playbook, warehouse managers have a strategy book for order picking. Trust me; choosing the right play can make all the difference when the game is on the line.
Discrete Order Picking
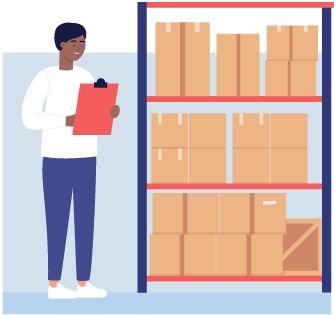
Do you know those solo performers who prefer the spotlight all to themselves? That’s discrete order picking. Pickers handle one order at a time, ensuring they give it their undivided attention. It’s all about accuracy and quality, one order, one picker, no mix-ups—simple and reliable.
Batch Picking
Next, we have batch picking, where a picker collects items for multiple orders in one go, which is perfect for small items that can fit into a single bin or cart. It’s like making a round of appetizers for a group—you’re aiming to please many in one swoop.
Zone Picking
Imagine you have your own little kingdom within the warehouse—that’s zone picking for you. Each picker rules over their domain, grabbing items within their zone only. It’s like a relay race; pickers pass the order until it’s complete. Coordination is key; when done right, it’s poetry in motion.
Wave Picking
Sometimes, you have to mix things up based on what the day throws at you, and that’s where wave picking comes in. Wave picking combines the best of batch and zone picking but adds a twist with timing. Orders are picked at different times of the day in waves—think of it as catching the right wave for the smoothest surf ride to the shore.
Cluster Picking
Finally, there’s cluster picking, where a picker simultaneously grabs items for several orders, thanks to a smart cart that keeps everything organized. It’s like a game of Tetris, where every block (or product) fits perfectly into its spot, making the most of each trip down the aisle.
Each method has its own rhythm and flow, and warehouse managers employ the method that best aligns with their operations.
Scanning the Way to Smoother Picking with Inventory and Order Management Software
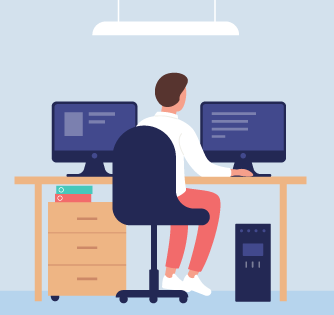
We’re about to unpack the digital tools that keep the pulse of warehouse operations solid and steady.
Inventory and Order Management Software: The Central Hub
Consider inventory and order management software the central hub of a warehouse’s operations. It’s a comprehensive platform that goes beyond simply monitoring what’s on your shelves. Inventory and order software monitors every unit, ensuring that what’s on the screen matches what’s in the warehouse. It uses historical data and analytics to anticipate what you’ll need next. It’s about having a clear picture, not just of the now but also of the next.
Additionally, inventory and order management software centralizes offline and online orders from eCommerce sites, marketplaces, EDI, direct sales, fax, or phone, ensuring all orders are processed with the same accuracy and efficiency.
Streamlining Picking and Packing with Barcode Technology
When inventory and order management software directs the show, it points pickers in the right direction, carving out the most efficient path through the aisles. Barcode scanners then step in to validate each selection. A straightforward yet powerful device, barcode scanners bring a new level of accuracy to picking orders. With each scan, the software verifies that the right product is selected, matching the digital order with the physical item. It’s a simple action that maintains the integrity of the picking process, instantly updating the system and keeping the inventory count spot-on.
The Outcome: Enhanced Operations
Implementing these technologies will transform the warehouse floor into a model of efficiency. Errors become rare, customer satisfaction rises, and the rhythm of work flows unimpeded by unnecessary delays or corrections. Pickers are equipped to work smarter, not harder, and the entire fulfillment process is optimized.
Inventory and order management software, paired with reliable barcode technology, is crucial for warehouses aiming to meet the modern demands of speed and accuracy.
Navigating the Hurdles of Order Picking
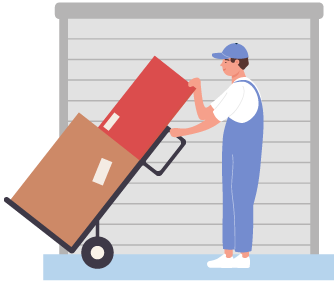
In warehouse operations, picking is about overcoming various challenges that can turn a smooth operation into a logistical labyrinth. Here’s a look at the hurdles every warehouse faces and how the pros tackle them.
Dealing with Peaks and Valleys
The ebb and flow of demand can catch even the most well-oiled warehouse off guard. Peaks like Black Friday, Cyber Monday, and holiday seasons can lead to a tsunami of orders, while slower periods can leave resources idle. Striking a balance requires agility and scaling up or down at a moment’s notice.
The Accuracy-Speed Trade-Off
The race against the clock is real. Customers expect fast deliveries, but speed can’t come at the cost of accuracy. Every incorrect order is a double whammy: it disappoints the customer and requires additional resources. Nailing this balancing act is like walking a tightrope, with customer satisfaction on one side and operational efficiency on the other.
The Space-Time Continuum
In warehouse lingo, space is time. The more ground a picker has to cover, the longer it takes to fulfill an order. Smart warehouse design is crucial, minimizing travel time and ensuring popular items are easily accessible. But even with the best layout, unexpected surges in certain products can throw a wrench in the works.
Keeping Up with the SKUs
In the age of personalization and variety, SKU proliferation is inevitable. But with every new product variation comes added complexity in storage and retrieval. Ensuring pickers can swiftly locate and identify the correct SKU among hundreds—if not thousands—is like finding a needle in a haystack.
Evolving Order Profiles
Gone are the days of bulk orders and uniform shipments. Today’s orders are a patchwork of single items, various sizes, and different packaging needs, all heading to different places. Adapting to these varied order profiles while keeping costs down and efficiency up is a continuous juggling act.
Staying Ahead of the Curve
Order picking isn’t just about today’s challenges; it’s also about anticipating tomorrow’s. As consumer behavior evolves and technology advances, warehouses must be clairvoyant and constantly adapt to stay ahead of the game.
Overcoming these challenges isn’t easy, but those who do it well find that the rewards—happy customers, fewer returns, and a healthier bottom line—are well worth the effort.
Order Picking in Warehouses FAQs
What is order picking in a warehouse?
Order picking is the process of retrieving products from their storage locations in the warehouse to fulfill customer orders. It’s a critical step in the distribution chain that directly affects delivery times and customer satisfaction.
Why is order picking important in a warehouse?
Warehouses can improve picking accuracy by implementing technology solutions like barcode scanning and inventory and order management software, optimizing warehouse layout for smoother picking routes, providing thorough training for pickers, and conducting regular audits to identify and correct inefficiencies.
What’s the difference between batch picking and zone picking?
Batch picking involves collecting items for multiple orders simultaneously to reduce the number of trips to the same location, while zone picking assigns individual pickers to specific areas of the warehouse to pick items within that zone for multiple orders, which are then consolidated later.
Call us at 817-870-1311