How do I start barcoding my inventory?
Built For
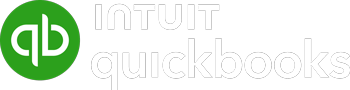
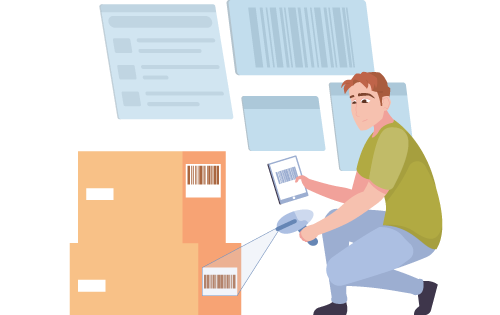
- The basics of barcoding
- The role of the barcode in the warehouse
- Accessing your inventory needs
- Selecting barcode inventory software
- Choosing barcoding hardware
How do I start barcoding my inventory?
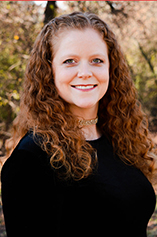
Have you ever found yourself lost in the abyss of your stockroom, wondering if there’s a better way to track that mountain of products? Well, there is, and it’s called barcoding. It’s like giving your products a digital handshake that says, “I’ve got my eye on you.”
Barcoding your inventory might sound like a task for big-box stores or logistics wizards, but it’s actually pretty accessible—and can be a game-changer for businesses of all sizes. We’re talking about speeding up receiving and picking, simplifying stock takes, and having real-time inventory insights at your fingertips. No more guessing when it comes to knowing exactly what’s on your shelves or in your storeroom.
In this article, we’ll explain why barcoding is awesome, how to start using it, and how it’ll make your life easier. Whether selling hand-crafted soap or running a bustling auto parts distribution business, barcoding is the secret ingredient to whipping your inventory into shape.
Understanding the Basics of Barcoding
So, what’s a barcode, anyway? At first glance, it might look like a bunch of lines with numbers underneath them, like the stripes on a zebra if it were a mathematician. But those lines are a language of their own—a language that scanners at the checkout counter speak fluently.
In technical terms, a barcode represents data in a visual, machine-readable form.
Originally, barcodes represented data by varying the spacings and widths of parallel lines, and are referred to as linear or one-dimensional (1D). Nowadays, we also have two-dimensional (2D) barcodes which can store much more information, like QR codes.
A Quick History Lesson
The first scan of a Universal Product Code (UPC) barcode was on a pack of Wrigley’s gum on June 26, 1974, in Troy, Ohio. Barcodes have come a long way since then!
Why Use Barcodes?
Barcodes make selling, tracking, and managing inventory much more efficient. They also help reduce errors—let’s be honest, humans aren’t perfect, and punching in numbers by hand is practically begging for mistakes. With barcodes, you scan and go. It’s quick, accurate, and saves you time and money.
The Role of the Barcode in the Warehouse
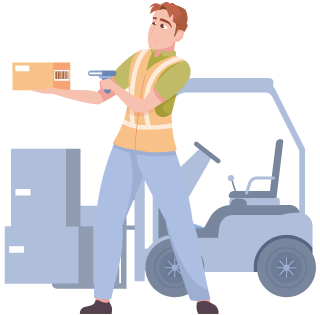
Let’s walk through a day on the job in the warehouse and see how barcodes turn chaos into harmony:
Receiving Inventory
First Contact: As new stock enters the warehouse, each item is scanned, making its grand entrance into your inventory system. This is where the barcode logs the product’s arrival, assigns it a location, and says, “Welcome to the inventory!”
Organizing Stock
A Place for Everything: Barcodes help categorize and assign locations to each item. They tell your staff exactly where items are located, preventing the hide-and-seek game with products.
Picking and Packing Orders
Accuracy: Scanning items during the picking process minimizes errors, ensuring the right product is always ready for its journey.
Inventory Counts
Cycle Counts Made Easy: Gone are the days of clipboards and tally marks. With barcodes, inventory counts are faster and more accurate, keeping your data as fresh as your products.
Quality Control
Seal of Approval: As products leave the warehouse, a final scan confirms that the order is complete and ready for dispatch. It’s like patting each package on the back before it heads out the door.
Returns Processing
Back with Dignity: When items come back as returns, barcodes help reintegrate them into your system, ensuring they’re accounted for and assessed for their next move.
Barcodes serve as the indispensable link between physical items and digital data in every corner of the warehouse. They are pivotal in creating an environment where efficiency reigns supreme, and nothing is left to chance.
Assessing Your Inventory Needs
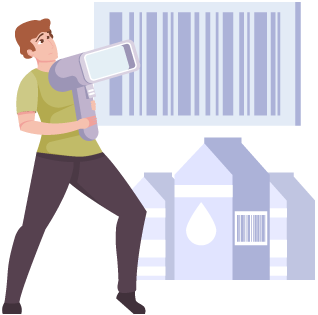
Now that we’ve seen all the places where barcodes can improve warehouse operations, you are probably ready to grab a scanner and get started. But before you jump into the world of barcodes, it’s time for a bit of self-reflection. Look at your inventory. Whether it’s a mountain of books, a sea of apparel, or a mix of this and that, understanding your inventory needs is the first step in choosing the right barcode system.
Inventory Size and Variety
- Small Inventory: If you’re managing only a few products, you might not need a complex barcode system.
- Large or Diverse Inventory: When dealing with lots of products or a wide variety of inventory, a more robust inventory system with barcoding could be your new best friend.
Sales Volume and Traffic
- Low Volume: A basic barcode system could suffice for those with just a few customers.
- High Volume: If your orders seem to never end, consider an inventory system with barcoding that can keep pace with the speed of your sales.
Tracking Needs
- Basic Tracking: Want to know what’s in stock? A simple system is probably all you need.
- Advanced Tracking: Need to track sales trends, reorder levels, or customer preferences? Invest in a system that provides detailed analytics.
Future Growth
Think about where your business is heading. Are you scaling up? Plan for a system that grows with you.
Budget
Determine how much you’re willing to invest. There’s a solution for every budget, so barcodes are within reach.
Now that put some thought into your needs, it’s time to translate that into action. How? By choosing barcode hardware and inventory software, you’ll make your barcoding dreams come true.
The Symbiotic Relationship Between Barcode Hardware and Software
Imagine a barcode scanner without inventory software. It’s like having a piano without someone to play it—a potential symphony left silent. The true power of barcodes isn’t in the scanner’s beep but in what happens after—that little moment when data leaps from the physical world into the digital realm.
Barcode scanners, printers, and other hardware are the hands in our analogy, performing the tactile work of reading and producing barcodes. But without the brain—the inventory software—to interpret and make sense of these scans, the hands are just… well, waving in the air. It’s the software that takes the baton from the hardware and conducts the orchestra.
The Vital Interpreter
- Barcode scans are mere numbers and lines until the software translates them into actionable data. It turns a simple scan into a product name, a quantity, a location, and more.
- Every scan is a conversation, and the software is the interpreter that ensures the message isn’t just heard but understood. It contextualizes each beep into the language of inventory management.
- The bridge between physical and digital inventory, the inventory software ensures that every item scanned is accounted for in real-time, maintaining a mirror image of your physical stock in a digital format.
Selecting Barcode Inventory Management Software
Barcode inventory management software is where your barcoding system comes to life. It’s the central hub that tracks, manages, and analyzes your products and is where to start when starting your barcoding journey.
Features to Look for in Barcode Inventory Management Software
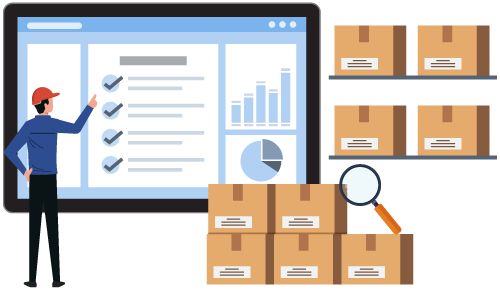
Here’s a breakdown of essential features that can help you slice through the chaos and keep your inventory in tip-top shape:
- Real-Time Tracking: The heartbeat of your inventory; real-time tracking ensures that your records are updated the moment a product hits the shelves or leaves your warehouse. This feature is a must for maintaining accurate stock levels and avoiding the embarrassment of selling products that are actually out of stock.
- Multi-Channel Order Management: In an age where your products are flying off virtual shelves from multiple online marketplaces, your website, via EDI, and your direct sales team, having a system that consolidates orders across all channels is a game-changer. This helps you stay organized and ensures a seamless experience for your customers, no matter where they shop.
- Warehouse Operations: Whether you have a single storeroom or multiple warehouses, barcode software with warehouse management features can help you optimize storage, streamline picking and packing processes, and reduce errors.
- Advanced Purchasing: Stay ahead of the curve with tools that automate your purchasing workflow. Advanced purchasing features help predict when you’ll run out of stock and generate purchase orders in advance, ensuring you never miss a sale due to stockouts.
- User-Friendly Interface: Let’s face it, not everyone is a tech whiz. A user-friendly interface means less time training staff and more time selling products.
- QuickBooks Integration: QuickBooks is the financial command center for most small and mid-sized businesses. Integration with QuickBooks means that your sales, purchasing, and inventory data can flow smoothly between your inventory software and QuickBooks without double data entry.
- Reporting and Dashboards: A treasure trove of data is no good buried. Robust reporting tools and dashboards give you insights at a glance. Track bestsellers, spot trends, and make informed decisions with data-driven gusto.
- Scalability: Dream big because your software should be able to keep up. Whether expanding product lines or growing your physical footprint, the right software grows with you, avoiding the pain of switching systems just when things are getting good.
- Security: In today’s world, data is gold, and you must protect it. Features like user permissions, audit trails, and secure data storage are the armored vault for your information.
- Integration with eCommerce Platforms: If you’re selling online, direct integration with e-commerce platforms like Shopify or WooCommerce can sync inventory levels, reducing overselling and underselling incidents.
- Accessibility: The world is mobile, and so are you. Mobile accessibility means you can manage your inventory and business on the go, whether in the office or on the go.
With these features in your arsenal, your barcode inventory management software won’t just be a tool—it’ll be the linchpin of your business’s operational efficiency, ready to tackle today’s demands and tomorrow’s growth.
Choosing the Right Barcode Hardware
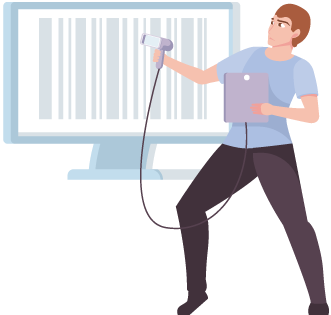
When bringing your barcode system to life, the first step is to chat with your inventory software provider about compatible hardware. Think of it as setting up a date between your software and its hardware match—it’s got to be the right fit to make barcode magic happen.
Starting the Hardware Hunt
Compatibility is Key: Before you fall in love with a scanner or printer, ensure it’s on the same wavelength as your software. Your provider can recommend hardware that’s guaranteed to work seamlessly with your system.
Barcode Scanners
- Wired vs. Wireless: Consider your daily operations. Do you need wired scanners’ reliability or wireless models’ mobility?
- Handheld vs. Stationary: Handheld scanners offer flexibility, while stationary scanners can boost efficiency at fixed points of sale or shipping stations.
- Laser vs. Imager: Select based on your barcode types and environment. Laser scanners are ideal for 1D barcodes and imagers for 2D barcodes and challenging lighting.
- Build to Last: If your workspace is rugged, opt for durable, ruggedized scanners that withstand drops and bumps.
Barcode Printers
- Scale and Space: Match the printer to your scale of operations—desktop printers for moderate printing needs and industrial ones for higher volumes.
- On-the-Go Printing: Mobile printers are handy for labeling away from a central location, making them perfect for large warehouses or when you need to print on demand.
- Quality Counts: Your labels should be as enduring as your products, especially if they face harsh conditions.
Labels
From waterproof, to removable, to freezer-safe, select labels that suit your products and their journey.
Assess the Work Environment
The setting dictates the hardware. A humid greenhouse, a cold storage unit, or a bustling warehouse each demands different hardware qualities.
Ergonomics and User Experience
Comfort must not be compromised. Choose devices that are a good fit for the hands that will hold them all day.
Choosing the right barcode hardware isn’t just about purchasing tools—it’s about investing in the players that will bring your inventory management system to life, all while ensuring they’re the perfect match for your software.
FAQs about Starting with Barcoding Your Inventory
Why should I barcode my inventory?
Barcoding your inventory streamlines the tracking and management process, dramatically reducing errors and saving time. With real-time updates and detailed reporting, you can keep a closer eye on stock levels, make informed purchasing decisions, and improve overall operational efficiency.
What’s the first step in barcoding my inventory?
The first step is assessing your inventory needs based on size, variety, and sales volume. This will help you determine the complexity of the barcode system you require, from the type of barcodes to the inventory management software and hardware you’ll need.
How do I choose the right barcode inventory management software?
Look for software that offers real-time tracking, multi-channel order management, and advanced purchasing features. The interface should be user-friendly and scalable and offer robust reporting and dashboard capabilities. If your business uses QuickBooks, seamless QuickBooks integration is critical.
Do I need special hardware to start barcoding?
Yes, you’ll need barcode scanners and printers that are compatible with your software. Scanners come in various forms, each suited to different environments and needs. Printers also vary depending on your printing volume and conditions.
Can barcode hardware work without software?
No, barcode hardware requires inventory management software to interpret the scanned data. The hardware captures the barcode information, but the software translates this into meaningful data, keeps track of inventory, processes orders, and more.
Call us at 817-870-1311