Brewery Inventory Management Software
Built For
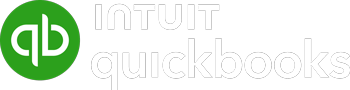
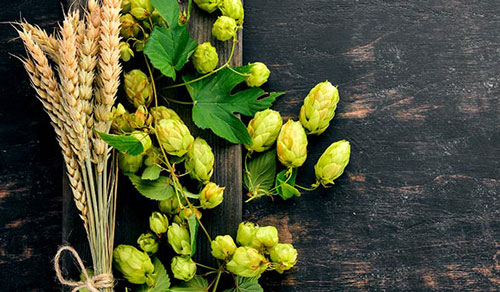
Brewery inventory management software
Craft breweries have no sign of fading away in the United States, as the industry continued to see growth and opportunity in 2018 despite predictions of negative headwinds produced by an oversaturated market.
But before we go any further, let’s define what a “craft brewery” is.
craft breweries, by design, are:
- Small — Producing 6 million barrels of beer or less annually
- Independent — Less than 25% of the craft brewery can be owned by an alcohol industry member that is not itself a craft brewer, such as an individual or a corporate entity such as Miller-Coors and Anheuser-Busch.
- Innovative — What separates a “craft” from a standard brew is a combination of unique flavor profiles, innovative production, and generally more artistic branding.
- Limited in Self-Distribution — Beholden to federal guidelines and state laws regarding distribution, micro and regional breweries rely on 3rd party distributors to move their beers across the country. Brewpubs rely more on site-beer sales, limited local distribution, and distributors if they want to sell beyond locale or state lines.
CRAFT MARKET SEGMENTS:
- Microbrewery – Produces less than 15k barrels a year, with 75% or more sold offsite
- Brewpub – A restaurant-brewery that sells 25% or more of beer on site. Where allowed by state law, brewpubs usually sell “Beer to go” and/or distribute to off-site accounts
- Regional – An independent craft brewery with a majority of volume in “traditional” or “innovative” beers [Deep Ellum Brewing Co., Rahr & Sons Brewing Co.]
Quick Note: If you work within the beer industry and are seeking better beer inventory management, but are not a brewer, check out our beer distribution page.
craft brewery Market Overview:
- In 2018, small and independent brewers collectively produced 25.9 million barrels and realized 4 percent total growth, increasing craft’s overall beer market share by volume to 13.2 percent.
- Retail dollar value was estimated at $27.6 billion, representing 24.1 percent market share and 7 percent growth over 2017
- 50 Craft Breweries out of 7,450 – contribute to the 10% out of 13% in growth the market experienced in 2018.
“Craft maintained a fairly stable growth rate in 2018 and continued to gain share in the beer market,” said Bart Watson, chief economist, Brewers Association.
Sources: Brewers Association; National Beer Wholesalers Association; Brewing Industry Guide

Okay, that’s a lot of data – but it’s important and powerful for small and independent craft brewers to get a lay of the land before investing in or improving on brewery management. For brewers seeking to grow beyond their community or to improve current operations, or both, software for brewery management is a game changer.
Just ask yourself – what separates the “Fastest Growing 50” from the rest of the herd? Considering the market, expansion at that rate can’t be solely driven from interesting beer.
Behind-the-scenes investments in information technology, production, and logistics – meaning centralization, automation, visibility, and analytics – play a big role in advancing nationwide growth. In layman’s terms? They are using brewery management software.
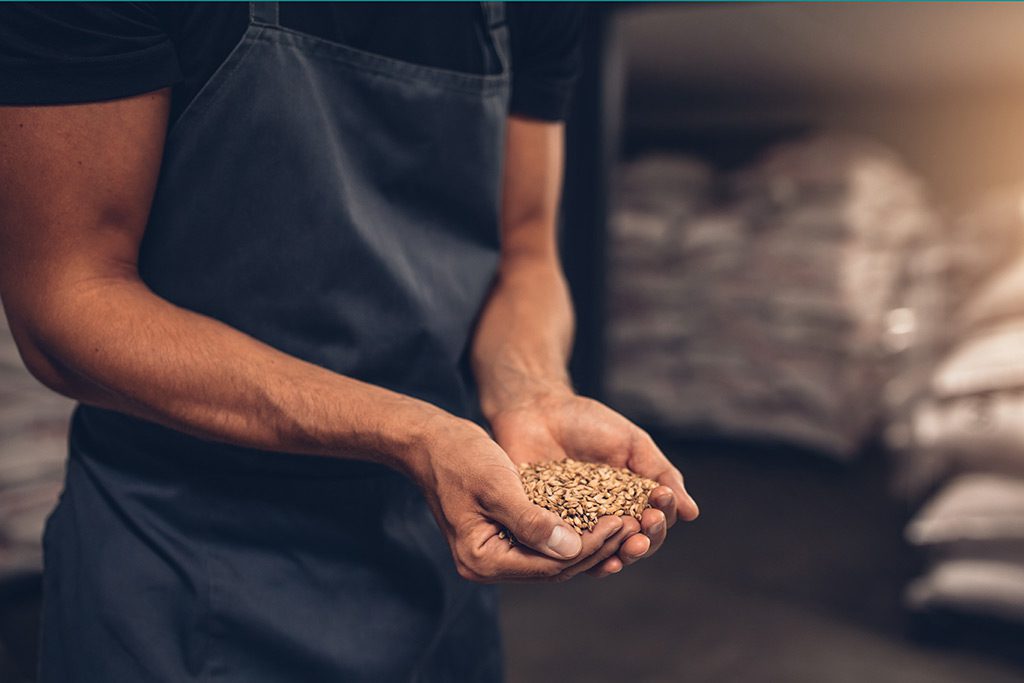
Brewery inventory management software to improve operations
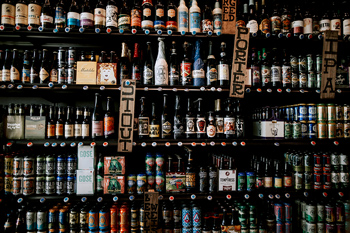
A craft brewery ready to make its way into national markets first and foremost needs real-time, detailed, centralized business intelligence to determine what their local fan base loves and replicate that on a much larger scale. A common issue amongst craft breweries is cash-flow management, and without a precise understanding of how cash flows in and out of a brewery, the greater at risk the brewery is.
A brewery is an operation built for and around inventory production and sales. With changing ingredients, varying production methods, and fluctuating consumer tastes, crafting the best strategies for success must be based on actual data and analysis. The best decisions are informed ones.
Brewery management software with real-time business intelligence is crucial for scaling brewery operations, inventory forecasting, demand planning, and for informed internal decision making — and for a brewery trying to gain a foothold in a crowded marketplace, business intelligence is a must.
Inventory Forecasting optimizes inventory investment by eliminating guesswork and determining per-item demand.
- Establish minimum stock quantity for each item based on expected demand
- Set alerts for when an item drops to reorder point/low on stock
- Auto-generate purchase orders based on inventory requirements
- Enable recommended reorder items & quantities based on set stocking levels and primary suppliers
- Evaluate vendor options and purchase-quantity per product, edit as needed
Sales & Trend Analysis optimizes purchasing and demand planning through sales & trend analysis.
- Better predict future production and purchasing needs
- Craft marketing plans based on product profitably to improve ROI
- Uncover geographical trends to potentially enable cost savings
- Use product-level sales information for more efficient supply chain strategy
Decision Support uses data centralization, analysis, and visibility for more informed decision making.
- Access detailed, historical customer records
- Utilize historical data for analyzing operational and customer trends, uncovering time and cost savings
- Monitor real-time key performance indicators
- Strengthen business management and expedite problem-solving
Acctivate brewery inventory management software crafted for QuickBooks
Acctivate is a convenient solution for breweries using QuickBooks. Instead of switching to a new brewery accounting software or starting a new ledger, Acctivate’s bi-directional integration with QuickBooks means your brewery gains more advanced inventory and business management while maintaining all of your financials securely in QuickBooks.
Brewery management software with powerful inventory control
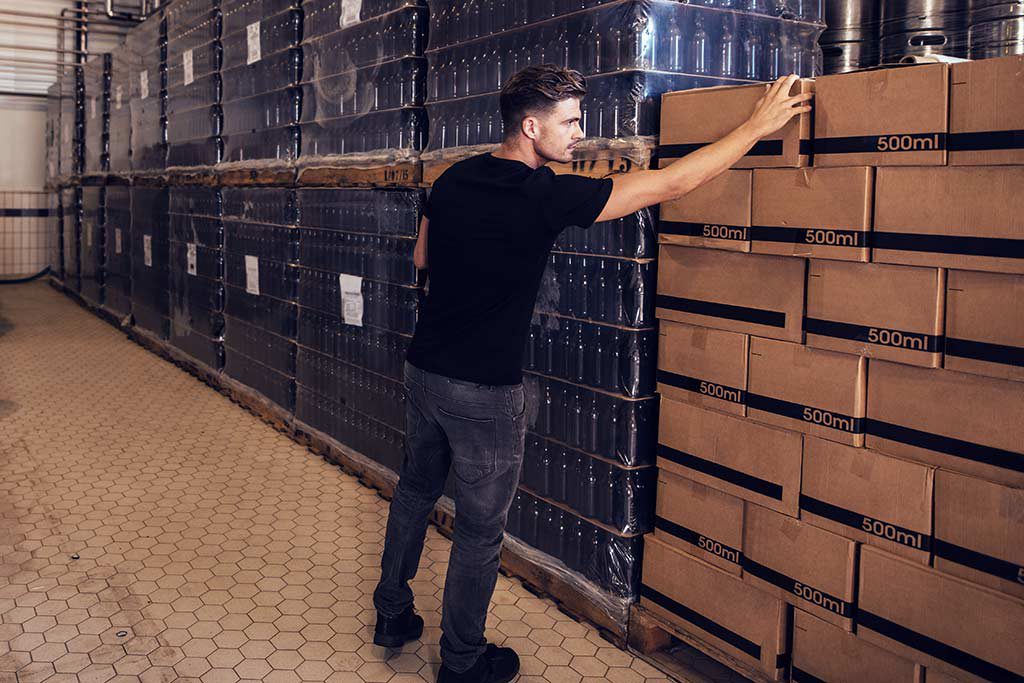
As mentioned above, a brewery with no inventory wouldn’t be a brewery. What can a brewer do without beer inventory management? Probably nothing fun. From raw ingredients to finished, packaged goods, and a whole lot of in between, it is a safe guess that a brewery is dependent on accurate inventory control. With inventory control, a brewery can know, in real-time, what they have and what they need at any given moment. Avoiding under and overstocking is always beneficial for cash flow, especially when inventory items are perishable.
With Inventory Control:
- Store & track an unlimited number of products in real-time
- Attach multiple alternate product IDs and description per product (SKU, UPC, industry-specific, vendor-specific, etc.)
- View inventory (per location) on hand, available, committed, on order, on reserve
- Manage substitutions, bill of materials, costing, and multi-tiered pricing
- Implement barcoding for more efficient inventory processing & fulfillment
- Always understand true costs with landed cost and/or multi-currency
Acctivate brewery management software with enhanced production management
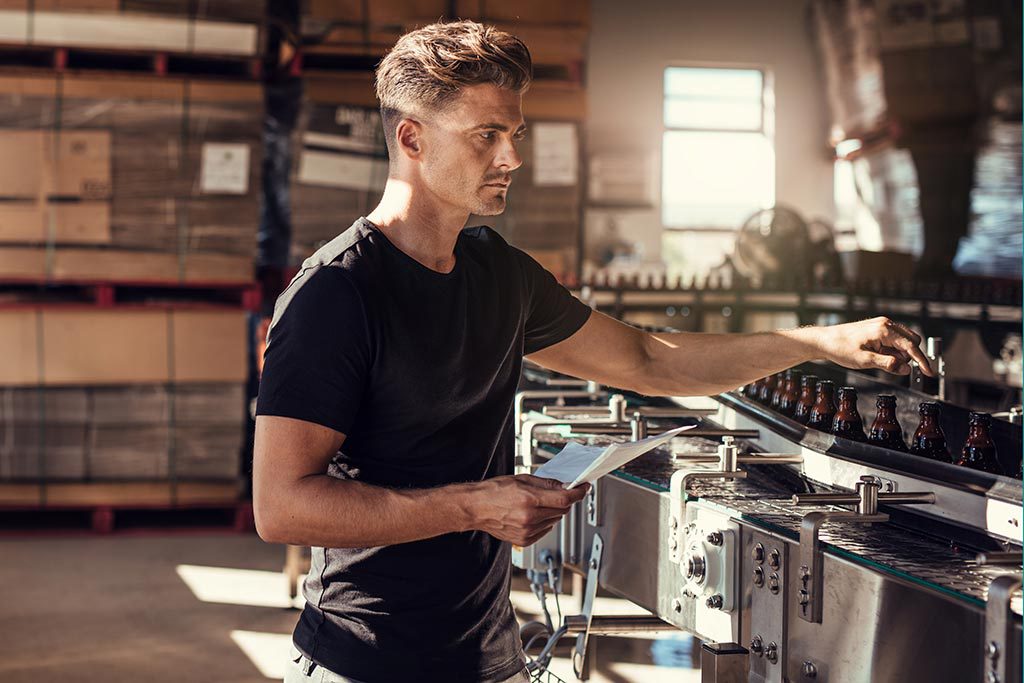
With inventory control, a brewery knows what it has and what it needs. With business intelligence, a brewery can better predict production needs. When it comes to production management, the aforementioned are a brewer’s guide. But on the production floor, there are other, equally important, processes and factors at play. From seasonal ingredients and batch variations, to end products and spillage — every component and step needs to be accounted for.
With Brewing Process Management:
- Adjust components based on seasonal requirements, availability, or required substitutions
- Handle variations in input recipe for substitution and quantity changes
- Variable recipe and variable yield capabilities
- Account for spillage and waste
- Handle multiple lots of the same ingredients
- Precise costing by batch
With Bill of Materials (BOM) & Assemblies:
- Specify components and quantities necessary for batch production and assembly (bottling/canning/kegging) with BOM
- Adjust BOM per product at any time while preserving previous transaction history
- Indicate assembly components (ex. BOM for specific batch, chosen container)
- Once assemblies are completed, depleted inventory used in the assembly will be reflected and the assembly itself will be a new “finished good”
- COGs roll forward from components to finished goods
Brewery management software with premier traceability + keg tracking
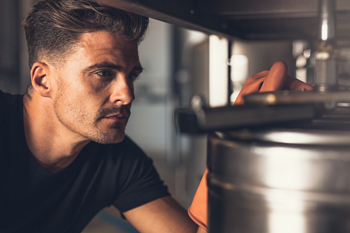
Keeping detailed accounts of each step an ingredient or finished good takes within and beyond the brewery may sound complicated and time-consuming, but with brewery management software, the addition of barcode technology, traceability is as fast and easy as scanning a barcode. Maintaining quality control and product integrity is key for performance, and compliance, in any food or beverage operation. If there is a recall situation, the ability to pinpoint the location(s) of the offending batch (once it has been assembled into bottles, packaged, and moved by a distributor) in minutes, is not only good for business reputation, but also for quickly heading off the recall damage.
For kegs sent to tap rooms, restaurants, or rented out to consumers, a quick scan of the matching serial number will reveal what was sold, when it was sold, and who it was sold too, making it simple to follow up on keg returns.
With Traceability:
- Be recall ready and better able to comply with industry regulations
- Track an unlimited number of raw and finished goods by lot or serial numbers end-to-end, including lot numbers for ingredients used in production
- Track filled kegs (Keg tracking) by a serial number created with a lot number for the beer and an ID number for the keg
- Track assembled products (single bottle/can, 6-pack, 12-pack, 24-pack, etc.) beyond the warehouse with lot numbers
- Manage and track quality-control issues, expiry dates, lot, inspection, and quarantine information
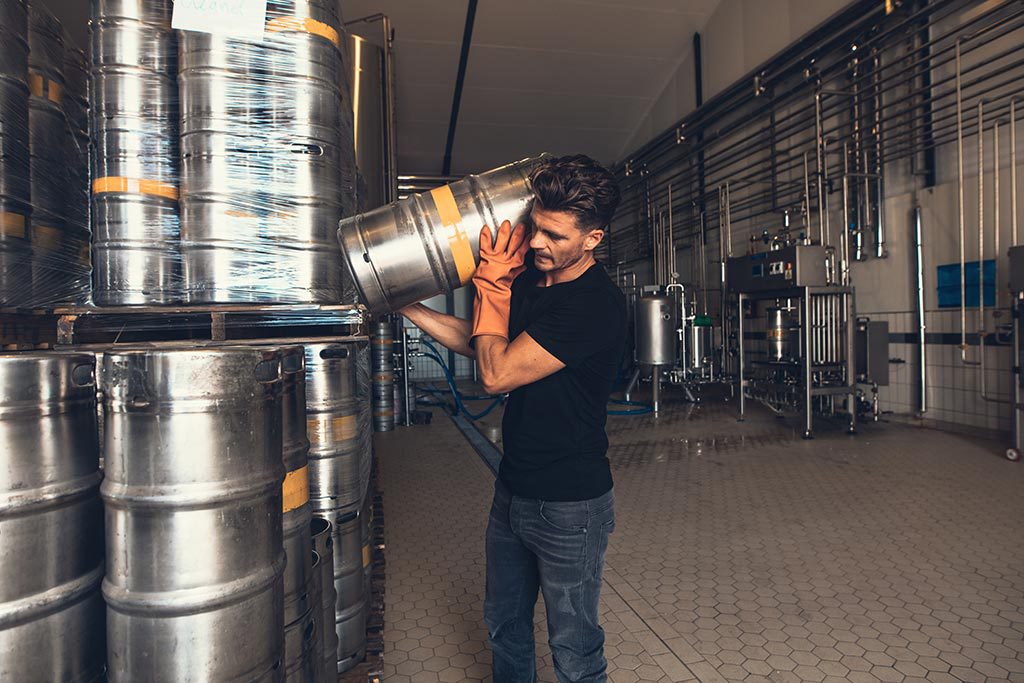
Call us at 817-870-1311