How Do Companies Deal with Product Recall Management?
Built For
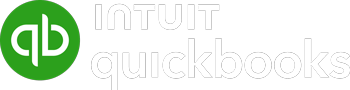
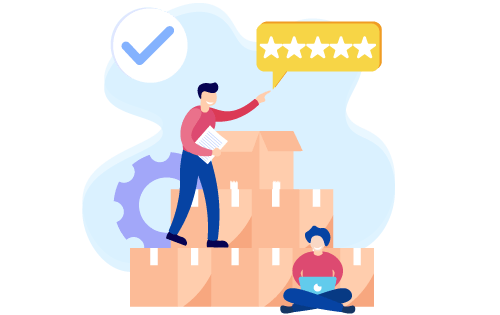
- Common challenges companies face during a product recall
- Role of inventory software in recall management
- Advantages of being recall ready with software
- Real-world case study of a wholesale manufacturer staying proactive with software for possible product recalls
How Do Companies Deal with Product Recall Management?
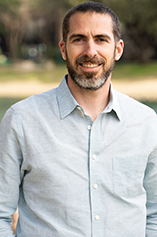
When a company issues a product recall, the stakes are high. Not only does a recall affect the company’s reputation, but it also poses safety risks to consumers and substantial financial risks to the company itself. Managing a product recall efficiently is crucial, yet the process can be complex, involving everything from identifying the problematic products to handling their return and communicating with the affected parties.
Inventory management software brings a modern solution to the age-old problem of product recalls. Inventory software simplifies the identification and tracking of affected products and enhances communication and compliance during a recall. In this article, we’ll explore how inventory management software turns a logistical nightmare into a manageable task, ensuring safety, compliance, and peace of mind for both businesses and consumers.
The Challenges of a Product Recall
When a product recall is announced, it’s not just about pulling items off shelves; it’s a multi-faceted challenge that tests a company’s operational capabilities and crisis management skills.
Here are some of the common hurdles companies face during a product recall:
- Identification of Affected Products: One of the most immediate challenges in a recall is identifying which products are affected. This involves tracing the product’s journey from manufacture to sale, which can be incredibly complex without the right tools.
- Efficient Logistics: Once the products are identified, companies must efficiently retrieve them from consumers, retailers, and warehouses. This logistics operation must quickly prevent further sales and use of the recalled products.
- Communication Overload: Keeping open lines of communication with consumers, retailers, regulatory bodies, and possibly the media is vital. Companies must provide regular updates about the recall process, health and safety information, and how consumers should proceed.
- Financial Impact: Recalls can be expensive. Costs include the logistics of pulling the product from the market, refunds or replacements for consumers, legal fees, and more. Moreover, there’s the potential loss of consumer trust, which can impact sales long after the recall has been resolved.
- Regulatory Compliance: Navigating the legalities surrounding recalls, adhering to government regulations, and ensuring all steps are correctly documented are crucial to avoid penalties and further complications.
These challenges can disrupt normal business operations and have long-term effects on a company’s financial health and reputation. However, with advanced inventory management software, companies can tackle these challenges more effectively and efficiently, minimizing the negative impacts of a recall.
Role of Inventory Management Software in Recall Management
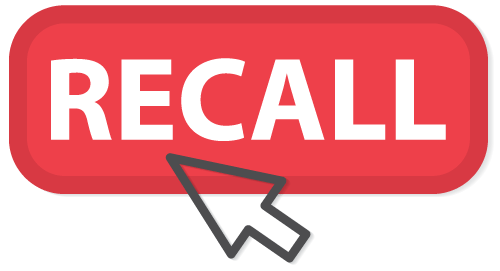
How do companies deal with product recall management? Inventory software plays a critical role in transforming the chaotic process of a product recall into a streamlined operation. Here’s how this technology steps up to address the challenges:
- Real-Time Tracking: The backbone of effective recall management is the capability to track and trace products throughout the supply chain in real time. Inventory management systems provide precise tracking capabilities from production through to customer delivery, ensuring that companies can pinpoint the location of any item at any point. This is crucial in swiftly identifying and isolating affected products to prevent further distribution.
- Batch and Serial Number Tracking: Inventory software allows companies to track products by batches or individual serial numbers. Lot and serial number tracking is invaluable during a recall as it helps identify exactly which products are affected and need to be recalled, reducing the scope and cost of the recall effort and minimizing disruption to unaffected products.
- Data Insights and Reporting: During a recall, it’s vital to have access to robust reporting tools to manage the recall process and comply with regulatory requirements. Inventory management software generates detailed reports on the recall’s progress, the number of items returned, and other vital metrics, which can be critical for regulatory compliance and internal audits.
By leveraging these features, inventory management software not only simplifies the recall process but also significantly enhances a company’s ability to handle recalls effectively, protecting both the consumer and the company’s brand.
Advantages of Using Inventory Management Software for Product Recall Readiness
The implementation of inventory management software provides numerous benefits during a recall and across various aspects of a company’s operations. Here are some key advantages:
- Increased Efficiency: Automating key processes like tracking and notifications with inventory management software allows recalls to be managed more quickly and with fewer errors. This efficiency reduces the time products are in the market after a recall is initiated, limiting potential harm and liability.
- Enhanced Accuracy: The precision of batch and serial number tracking ensures that only the affected products are recalled, avoiding unnecessary costs and disruption associated with more comprehensive recalls. Accurate tracking also supports effective stock control during normal operations.
- Improved Compliance: Compliance with regulatory requirements is non-negotiable. Inventory management systems help ensure that all actions before and during a recall are recorded and traceable, allowing for easier compliance with laws and regulations at local, national, and international levels.
- Better Customer Trust and Relations: Efficiently managed recalls demonstrate a company’s commitment to safety and responsiveness. By quickly identifying and addressing issues, companies minimize consumer inconvenience, thereby preserving and often enhancing customer trust and loyalty.
- Cost Savings: Although implementing inventory management software requires an initial investment, the long-term savings from avoided recall-related costs and improved efficiencies are substantial. Furthermore, the ability to conduct precise recalls minimizes the scope and expense of such events.
- Scalability: As companies grow, so do their inventories and the complexity of managing them. Inventory management software can scale to accommodate growth, support new product lines, and manage increasing amounts of data, making it a valuable tool for long-term operational success.
- Data-Driven Decision Making: The insights provided by comprehensive data analysis tools within inventory management systems allow companies to make informed decisions. This data can reveal patterns that may predict future issues, allowing preventive measures to be implemented before problems escalate.
Case Study: Recall Readiness at Harvest Valley Bakery
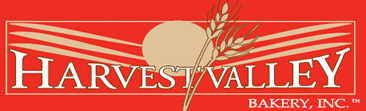
Harvest Valley Bakery, a certified Women’s Business Enterprise in LaSalle, Illinois, is not only renowned for its high-quality private-label cookies and breakfast bars but also for its exceptional standards in production and safety. The bakery, led by owner and president Nancy Jenks, has been operating for over 25 years, serving a diverse range of customers, including schools, airlines, and the military.
Embracing Technology for Enhanced Safety
Miranda DeMaso, the Office Manager at Harvest Valley, plays a crucial role in ensuring the bakery runs smoothly day-to-day and remains recall-ready—a critical aspect for any food production company. Harvest Valley uses Acctivate, an inventory management software that integrates seamlessly with QuickBooks, to handle everything from invoicing to lot-number tracking.
Managing Variability with Precision
One of the unique challenges Harvest Valley faces is ingredient variability, which can affect product consistency due to factors like humidity or different flour brands. Before Acctivate, managing this variability was challenging because the previous software required creating a new recipe each time an ingredient varied. Acctivate’s batch processing features allow the bakery to adjust components in real time without changing the base recipe, maintaining consistent quality and precise lot tracking.
Mastery of Mock Recalls
Though Harvest Valley has never faced a live product recall, its preparedness is tested through regular mock recalls. These exercises are critical in ensuring that if a recall were ever necessary, the team could handle it efficiently and effectively. During a mock recall, Miranda recently collaborated with Acctivate’s support team to customize a report that streamlined the gathering of necessary recall information, demonstrating the system’s flexibility and responsiveness.
Track & Trace: A Favorite Feature
Miranda highlights Acctivate’s Track & Trace as her favorite feature due to its simplicity and effectiveness. The ability to pull up a product and view all associated lot numbers at once significantly reduces the stress of managing potential recalls. This feature allows for quick access to detailed product histories, ensuring that Harvest Valley can meet stringent FDA requirements swiftly—in Miranda’s case, within 30 seconds during mock recalls, compared to the painstaking process of sifting through physical records.
Time and Cost Savings
The efficiency brought by Acctivate extends beyond recall readiness. Harvest Valley has seen significant time savings simply by being able to quickly access lot numbers and detailed product information. This efficiency reduces the risk of errors, like transposed numbers, which are critical in recall situations, and saves money by reducing the labor hours needed for such tasks.
Harvest Valley Bakery’s proactive approach to recall readiness, powered by Acctivate’s robust features, ensures regulatory compliance and safety and reinforces their commitment to quality and customer trust. By integrating advanced inventory management technology, Harvest Valley remains a leader in their field, ready to respond swiftly and effectively to any product safety challenges.
Call us at 817-870-1311