How Do You Calculate Safety Stock?
Built For
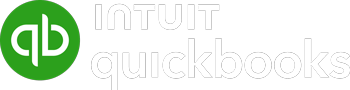
- The whys and hows of safety stock
- The safety stock calculation
- Tips & tricks to effectively manage stock
How Do You Calculate Safety Stock?
Have you ever found yourself in a pickle because you ran out of stock? If you’re nodding your head, you know it’s not just about the oops moment; it’s about the “oh no” when customers can’t get what they want. That’s where safety stock comes in – your secret stash of goods keeps those “out of stock” signs at bay.
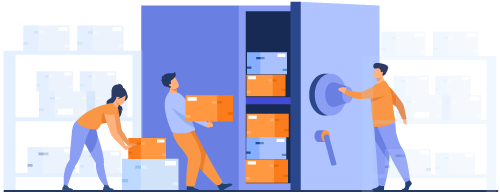
Think of safety stock as your business’s safety net. It’s that extra inventory you keep around just in case things get a little wild. You know, like when everyone suddenly decides they want your product at the same time, or your supplier decides to take the scenic route, and your new stock is taking forever to arrive.
You might be thinking, “Why not just stock up like there’s no tomorrow?” While having a mountain of products might sound like a plan, it’s not the best move. Stockpiling can be pricey, making your cash flow low on cash and flow.
So, how do you figure out this whole safety stock thing without going overboard? That’s what we’re exploring today. We’ll break it down, give you the lowdown on the whys and the hows of safety stock, walk you through a safety stock calculation that won’t make your head spin, and have a few tips and tricks to keep your stock game strong and your customers delighted.
Why Bother with Safety Stock?
Let’s talk about why safety stock is crucial in inventory management. Safety stock is all about dodging those pesky stockouts. Imagine you have a hot product that’s flying off the shelves. Suddenly, you hit a snag – your supplier’s shipment is delayed. Without safety stock, you’re stuck telling customers, “Sorry, we’re all out!” Nobody wants to be that person.
Safety stock is like your buddy who always has an extra charger when your phone’s about to die – it’s there when you need it most. Safety stock is the buffer that keeps you smiling instead of sweating when demand goes up and down like a yo-yo. And let’s not forget about lead times. Safety stock helps you cover that, too.
Safety stock is not just about keeping sales rolling. It’s also about trust. Customers rely on you to have what they need when they need it. When you come through, they remember. And when you don’t, well… they remember that too. Safety stock helps make sure you’re remembered for all the right reasons.
Understanding the Influencers of Safety Stock
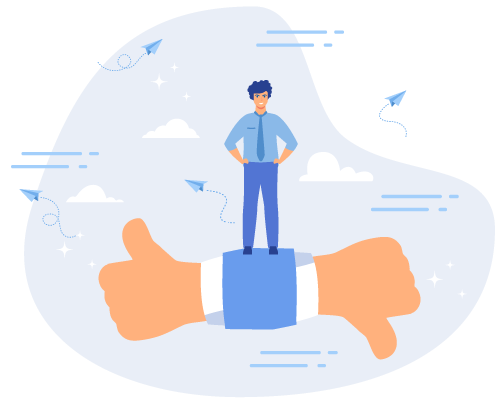
When it comes to safety stock, there’s a bit of a science to getting it just right. Several factors come into play, each one nudging your safety stock levels this way or that. It’s like a finely-tuned ecosystem where each element has its role. Recognizing and understanding these influencers is crucial for maintaining that sweet spot of inventory—not too much, not too little. Let’s delve into these factors and how they can shape your approach to safety stock.
Demand
First up is customer demand. It’s like the weather – sometimes predictable, sometimes you’re caught in the rain without an umbrella. If your product suddenly becomes the next big thing, demand can skyrocket. On the flip side, demand can drop before you can say “sale.” Your safety stock needs to adapt to the rhythm of your customer’s needs.
Lead Time
Have you ever ordered something online, and it took ages to arrive? That’s lead time for you. The time it takes for your products to go from “Hey, we need more!” to “Look, it’s here!” can be full of surprises. If your suppliers have episodes of unpredictability, you need enough safety stock to keep your customers happy when delays occur.
Service Level
Service level is about how often you want to play the hero. A high service level means you’re aiming to have what your customers need almost all the time, and it takes effort and a bit more cash outlay. The higher your service level goal, the more safety stock you’ll want to keep on hand.
The Other Players
It’s not just about supply and demand. Seasonality can swing things – think ice cream in summer or umbrellas in monsoon season. Market trends, promotions, and global events – all join the party and affect your stock levels.
Cash Flow
More safety stock means more money tied up in goods in your warehouse. It’s a balance – you want enough stock to keep sales smooth but not so much that your cash flow gets the blues.
Getting Down to Numbers: Basic Safety Stock Calculation
Ready to dig into some math? Don’t worry, we won’t get too wild. The basic safety stock formula is not too complicated. It’s about having enough stock on the shelf to keep you covered if things get unpredictable.
Safety Stock = (Maximum daily usage * Maximum lead time) – (Average daily usage * Average lead time).
Simple, right? Let’s break it down:
- Maximum daily usage: This is the most you’ve ever sold in a day. Think about when your product was hotter than a summer blockbuster, and everyone wanted one.
- Maximum lead time: The longest it’s ever taken for new stock to arrive. Remember when it felt like your shipment was on a world tour before it got to you? That’s your max lead time.
- Average daily usage: This is your day-in, day-out average; it’s what you usually see.
- Average lead time: This is the usual time for your stock to arrive after you reorder.
You get a safety stock figure tailored to your business’s heartbeat by crunching these numbers. It’s your cushion, your “just in case,” your “I got this” for when life throws a curveball at your inventory. It’s also important to remember that this isn’t an exact science. It’s more like a recipe you tweak until you get your secret sauce right.
Simple Safety Stock Formula in Action: A Step-by-Step Example
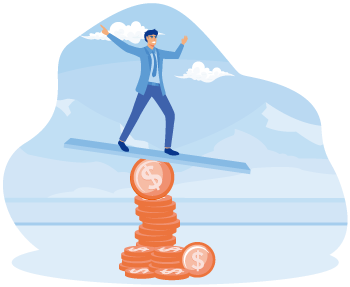
Let’s put theory into practice and see how the basic safety stock formula works in the real world. Grab your calculator, and let’s crunch some numbers with a real-life example.
Suppose you’re running a toy-selling business that sells action figures, and you need to figure out your safety stock. You don’t want to miss out on sales, but you also don’t want action figures taking over every inch of your storage room. So, here’s what you have:
- Maximum daily usage: The most you’ve ever sold in a day is 120 figures when the latest blockbuster movie dropped.
- Maximum lead time: Once, due to a port strike, it took 30 days for your new stock to arrive.
- Average daily usage: On a regular day, you sell about 50 figures.
- Average lead time: Typically, it takes 15 days for your stock to arrive after placing an order.
Now, let’s put those numbers into our formula:
Safety Stock = (Maximum daily usage * Maximum lead time) – (Average daily usage * Average lead time)
Plugging in your numbers:
Safety Stock = (120 figures * 30 days) – (50 figures * 15 days)
Safety Stock = (3600 figures) – (750 figures)
Safety Stock = 2850 figures
Using this basic formula, you’d want to keep a safety stock of 2850 action figures to protect against stockouts during a supply delay or a sudden spike in demand. This number is your inventory cushion, ensuring that you’re covered even if another movie comes out or there’s another delay.
Remember, this is a simplified example to illustrate the concept. While our basic safety stock calculation provides a solid starting point, more sophisticated techniques designed to fine-tune your safety net are typically used in inventory management. Advanced safety stock methods consider a more comprehensive array of variables, including the variability in demand and lead times, and often use statistical models to offer a more precise buffer against uncertainty. By deploying advanced approaches, businesses can better align their safety stock levels with their specific risk tolerance, service level goals, and financial constraints, ensuring they’re prepared for whatever the market throws their way without tying up unnecessary capital.
Leveraging Inventory Management Software for Safety Stock Precision
Inventory management software is a necessity for businesses looking to nail their safety stock levels. Gone are the days of back-of-the-envelope calculations and gut feelings. Today’s software crunches the numbers for you, considering the myriad factors influencing demand, supply, and everything in between.
What does inventory management software mean for your business? It means accuracy, efficiency, and peace of mind. You can easily calculate safety stock, ensuring that your inventory levels are optimized based on real-time data and historical trends, saving time, lowering the risk of human error, and enabling you to focus on other areas of your business.
Moreover, inventory management software can provide valuable insights into your sales patterns, highlight potential supply chain disruptions before they become critical, and suggest adjustments to your safety stock levels as market conditions change. This level of responsiveness is crucial in today’s market, where quickly adapting to changes can be the difference between thriving and merely surviving.
How Do You Calculate Safety Stock? FAQS
What is Safety Stock?
Safety stock is an extra quantity of inventory kept on hand to prevent stockouts caused by fluctuations in demand and lead times. Safety stock is a buffer to ensure you can meet customer demand without interruption, even when unexpected supply chain disruptions occur.
Why is Calculating Safety Stock Important?
Proper safety stock calculation balances customer demand and minimizes inventory costs. Too little safety stock risks stockouts and lost sales, while too much ties up valuable capital in unsold inventory. Accurate safety stock levels help businesses avoid these pitfalls.
How Do You Calculate Basic Safety Stock?
The basic, simplified formula for calculating safety stock is: Safety Stock = (Maximum daily usage * Maximum lead time) – (Average daily usage * Average lead time). This formula provides a starting point for understanding how much extra inventory you should keep to cover variations in demand and supply.
What Factors Influence Safety Stock Levels?
Several factors impact safety stock levels, including demand variability, lead time variability, service level goals, and broader market trends or seasonal fluctuations. Understanding these factors is essential for setting appropriate safety stock levels.
How Can Inventory Management Software Help with Safety Stock?
Inventory management software automates calculating and maintaining safety stock levels, using algorithms and real-time data to optimize inventory. Inventory management software reduces the risk of human error, saves time, and provides insights into sales patterns and potential supply chain disruptions, allowing for more accurate and responsive inventory management.
Call us at 817-870-1311