What is a Parts Management System?
Built For
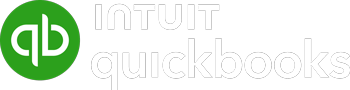
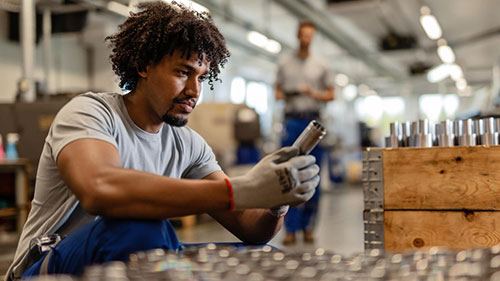
A parts management system is a comprehensive solution that facilitates efficient organization, tracking, and control of a business’ parts, components, and supplies. By providing tools for inventory management, order processing, supplier management, and data analytics, a parts management system helps businesses optimize their supply chain, reduce costs, minimize downtime, and make informed decisions to enhance overall productivity and operational efficiency.
Understanding the parts management system
A comprehensive parts management system comprises a well-structured framework of processes and procedures tightly integrated with a specialized software solution. Parts management encompasses various business functions, from procurement to inventory control and tracking to order management and fulfillment.
Benefits of implementing a parts management system
Streamlined inventory management

A parts management system streamlines inventory management, allowing businesses to track the availability and usage of each part, ensuring that stocks are replenished at the right time and shortages are avoided. A parts management system:
- Enables businesses to track and identify parts accurately using barcodes, lot numbers, and serial numbers, ensuring quick and error-free parts retrieval and traceability.
- Provides real-time visibility of inventory levels, helping prevent stockouts and overstocking, reducing production downtime and unnecessary procurement costs.
- Facilitates seamless multiple-channel order management, automating tasks and minimizing manual errors.
- Aids in effective vendor management, assisting with supplier performance assessment and cost-effective procurement.
- Enhances data accuracy and enables better decision-making.
Cost reduction and budget optimization
Efficient parts management is crucial for organizations to optimize costs and optimize budgets. By implementing an advanced parts management system, companies attain unprecedented levels of inventory accuracy, reduce overstocking, minimize waste, and optimize procurement practices. A parts management system:
- Optimizes inventory levels, preventing overstocking and stockouts, which minimizes excess inventory carrying costs and production downtime expenses.
- Enables businesses to identify and eliminate obsolete or duplicate parts, reducing unnecessary inventory expenses.
- Provides valuable insights into parts usage and demand patterns, allowing businesses to forecast demand, identify cost-saving opportunities, and implement more efficient strategies.
- Enables better supplier management, providing businesses with information to assess vendor performance, understand the true landed costs of parts, streamline purchasing activities, and identify cost reduction opportunities.
Enhanced data accuracy and reporting
By centralizing parts, vendors, orders, and customer data, businesses gain visibility throughout their operations and supply chain, enabling them to make better-informed decisions quickly and efficiently.
Parts management systems’ advanced reporting and analytics features provide valuable insights into parts usage, demand patterns, and costs, assisting businesses with making informed decisions, identifying trends, and implementing improvements in their inventory and supply chain management strategies.
Components of a parts management system
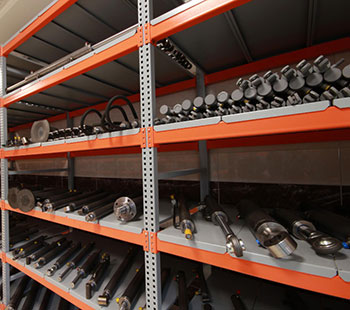
Components of a comprehensive parts management system work together to ensure efficient handling and control of parts and components throughout their lifecycle. The main components of a parts management system include:
Real-time inventory visibility
Real-time visibility of inventory levels is crucial for avoiding stockouts and overstocking situations and also plays a vital role in optimizing inventory management and enhancing overall operational efficiency. With a parts management system, organizations gain access to up-to-date information on available quantities, reserved stock for pending orders, and lead times for restocking. This real-time data enables businesses to make informed decisions, ensuring they maintain adequate stock levels to meet customer demands while avoiding excess inventory that ties up valuable resources and increases carrying costs.
By proactively monitoring inventory levels, businesses can set automatic reorder points, triggering purchase orders when the stock reaches predefined thresholds, thus minimizing the risk of stockouts and costly production or sales interruptions. Moreover, the system’s ability to track reserved stock and lead times aids in accurate planning and order fulfillment, reducing delays and ensuring timely customer deliveries.
Real-time inventory visibility provided by the parts management system fosters inventory optimization, enhances customer satisfaction, and contributes to a lean and agile supply chain, positioning businesses for success in today’s fast-paced market.
Order management and fulfillment
A parts management system revolutionizes the order management process, offering a seamless and efficient approach to handling orders from various channels. The system provides a consolidated view of the order pipeline by centralizing all incoming orders, whether through online platforms, direct sales, or other channels. This centralization eliminates the need for personnel to navigate multiple platforms, reducing the chances of manual errors and data discrepancies.
After receiving the order, the parts management system ensures that orders are swiftly processed and fulfilled, minimizing delays and expediting the shipping process. As orders are automatically routed to the appropriate departments, such as inventory management, packing, and shipping, the risk of miscommunication and bottlenecks is significantly diminished. Real-time order tracking and status updates allow customers and internal stakeholders to stay informed about their orders’ progress, enhancing transparency and customer satisfaction.
The parts management system’s streamlined order management process empowers businesses to operate more efficiently, providing a competitive edge in meeting customer demands quickly and accurately.
Vendor management and procurement
A comprehensive database of suppliers forms the backbone of an efficient parts management system, enabling users to access historical information crucial for tracking supplier performance and assessing their reliability. By maintaining a detailed record of past transactions, delivery timelines, product quality, and overall vendor interactions, the parts management system empowers purchasing managers with valuable insights to make informed decisions. The ability to track and monitor supplier performance based on factors such as timeliness, accuracy, and total cost of goods helps organizations establish fruitful, long-term partnerships with dependable suppliers while identifying areas for improvement in their supply chain. Moreover, the database facilitates the evaluation and selection of vendors based on their track record and capabilities, ensuring that the most suitable partners are chosen for specific requirements.
Incorporating features to streamline procurement activities, the parts management system automatically alerts purchasing managers when stock levels reach specified thresholds. This proactive approach ensures that stockouts are minimized. Purchase orders are generated, tailored to the required quantities and specifications, reducing manual errors and expediting the ordering process. The seamless integration of supplier data, inventory management, and purchasing activities allows organizations to optimize their supply chain operations, enhance productivity, and minimize unnecessary inventory carrying costs.
A centralized database and automated alerting within the parts management system ensure that parts and components are readily available when needed, contributing to an efficient, cost-effective, and highly reliable parts management process.
Parts lookup
Quick and straightforward parts management system accessibility is paramount to streamlining operations, with users able to access a vast inventory with multiple lookup methods swiftly. Whether searching by SKU (Stock Keeping Unit), keyword, part name, serial number, or alternative IDs, the system accommodates diverse search preferences, catering to individual user needs and business preferences. By providing a user-friendly interface and intuitive search functionality, the parts management system facilitates rapid navigation through the extensive inventory database, significantly reducing the time spent locating items.
Comprehensive access to inventory data empowers users across departments to locate the necessary parts efficiently, enhancing overall productivity and operational efficiency.
Barcoding
Barcoding, used in conjunction with the parts management system, enables seamless and rapid identification, tracking, and monitoring throughout the entire lifecycle of the part or component. When receiving new parts, staff members scan the barcode to update the inventory. During storage, barcodes facilitate precise location tracking and inventory updates as parts are moved or used. When parts are used or sold, barcodes provide access to detailed information, reducing the risk of errors.
Traceability
Serial numbers or lot numbers are integral to a parts management system, providing vital traceability and control over individual components or batches. Each part can be assigned a unique serial number or grouped under specific lot numbers, allowing for precise identification and tracking throughout its lifecycle. This information is crucial for quality control, warranty management, and recall procedures, ensuring that any issues related to specific parts can be isolated and addressed swiftly.
Additionally, serial numbers or lot numbers facilitate effective inventory management by enabling accurate stock level monitoring and rotation, minimizing the risk of stockouts or wastage. In cases where parts have different specifications or manufacturing origins, these identifiers help ensure that the correct parts are used for specific applications, enhancing safety and operational efficiency.
Reporting and analytics
Reports and analytics are instrumental in harnessing the full potential of a parts management system, providing valuable insights and data-driven decision-making capabilities. By leveraging the information collected within the system, organizations generate comprehensive reports on inventory levels, parts usage, supplier performance, and usage trends. These reports offer a clear overview of the parts ecosystem, enabling businesses to identify opportunities for cost reduction, optimize inventory levels, and streamline procurement processes.
Advanced analytics delve deeper into the data, uncovering patterns and trends that might not be apparent at first glance. Armed with these actionable insights, companies make informed decisions, forecast demand accurately, and proactively plan for the future.
By leveraging these key components, a parts management system empowers organizations to optimize their inventory, reduce costs, enhance operational efficiency, and ensure smooth operations throughout the supply chain.
Call us at 817-870-1311