Mastering the Art of Purchasing and Supply Management
Built For
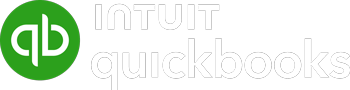
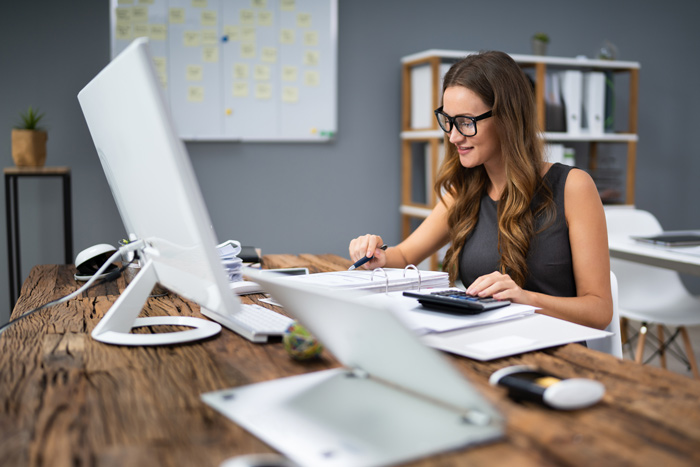
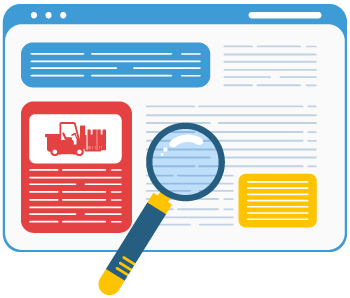
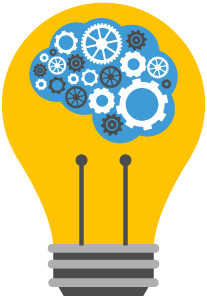
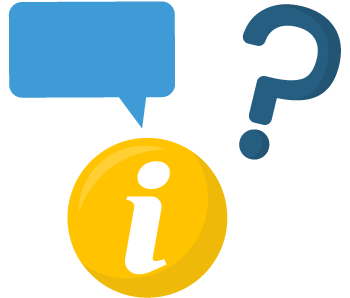
Purchasing and supply management, often referred to as an art, embodies the delicate balance of strategic decision-making, creative problem-solving, and meticulous execution required to orchestrate the seamless flow of resources and goods throughout a complex business ecosystem.
In this article, we delve into the art of purchasing and supply management, also called procurement, equipping you with essential strategies for success in this dynamic field. We explore the fundamentals of purchasing and supply management, examine the pivotal role of technology, and delve into best practices through real-life case studies. Join us on this journey as we uncover key insights and provide valuable guidance to help you navigate the intricacies of purchasing and supply management, empowering you to thrive in today’s ever-evolving business landscape.
Understanding the fundamentals of purchasing and supply management
Purchasing and supply management definition and importance
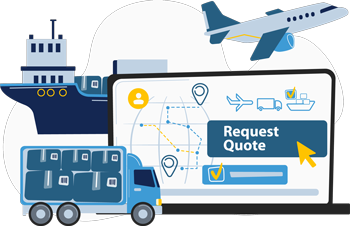
Purchasing and supply management involves sourcing, procuring, and managing the flow of goods and services necessary for an organization’s functioning. Effective purchasing and supply management significantly impacts various aspects of a business, including cost control, risk mitigation, supplier relationships, inventory availability, and overall operational efficiency.
First and foremost, purchasing and supply management directly affect a company’s financial health. By strategically managing the procurement process, organizations optimize costs, negotiate favorable terms with suppliers, and ensure the best value for money spent, including identifying cost-saving opportunities, conducting market research to find competitive suppliers, and leveraging economies of scale through bulk purchasing. By streamlining procurement and supply chain processes, businesses achieve cost efficiencies, reduce overheads, and enhance profitability.
Purchasing and supply management are crucial for mitigating risks and ensuring a reliable supply chain. Businesses face various risks, such as supply disruptions, quality issues, or changes in market dynamics. By implementing robust purchasing and supply management practices, organizations proactively identify and manage risks, diversify their supplier base, and develop contingency plans to maintain business continuity. Strong supplier relationships built through effective purchasing and supply management lead to improved product quality, on-time delivery, and enhanced responsiveness to market changes, ultimately boosting customer satisfaction and loyalty.
What are the responsibilities of a purchasing professional?
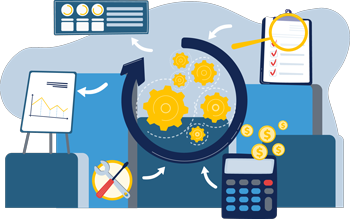
Purchasing professionals are responsible for strategically managing the entire procurement process, from selecting suppliers to predicting demand, optimizing costs, ensuring quality, mitigating risks, and driving overall operational efficiency. Key responsibilities include:
Strategic sourcing
Identifying, evaluating, and selecting suppliers based on quality, cost, reliability, and ethical considerations. The purchasing and supply management sourcing process typically includes conducting market research, negotiating contracts, and managing supplier relationships.
Supplier management
Building and maintaining strong relationships with suppliers to ensure timely delivery, quality control, and continuous improvement. Purchasing and supply management professionals monitor supplier performance, contract compliance, resolve issues, and foster collaboration.
Forecasting and demand planning
Developing and implementing procurement strategies aligned with organizational goals, including forecasting demand, assessing inventory levels, and determining appropriate purchasing quantities and timelines.
Cost control
Working to optimize costs and achieve cost savings through various strategies such as supplier negotiations, analyzing pricing trends, identifying cost reduction opportunities, and implementing cost-effective purchasing practices.
Risk assessment and management
Identifying potential risks in the supply chain, such as supply disruptions, quality issues, or regulatory compliance, and developing mitigation strategies, including implementing contingency plans, diversifying suppliers, and monitoring market conditions.
Purchasing activities
Issuing purchase orders to selected suppliers, specifying the goods or services required, quantities, delivery timelines, and pricing terms. Additionally, purchasing professionals conduct ongoing monitoring to ensure timely receipt of goods and services, verify order accuracy, inspect quality, and resolve discrepancies or issues.
Data analysis and reporting
Utilizing data analytics to gather insights, tracking key performance indicators (KPIs), and generating reports to assist with making informed decisions, identifying areas for improvement, and evaluating supplier performance.
Continuous improvement
Proactively seeking opportunities for process enhancements, cost efficiencies, and quality improvements within the purchasing function, including implementing best practices, exploring new technologies, and staying updated with industry trends.
Challenges and complexities of purchasing and supply management
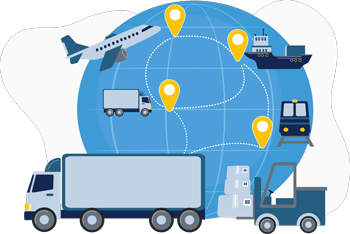
Purchasing and supply management professionals face many challenges and complexities in today’s fast-paced and interconnected business landscape. Supply chain management is constantly changing as a result of globalization, supply chain intricacies, evolving customer demands, and regulatory requirements.
Navigating these challenges requires a deep understanding of industry dynamics, strategic planning, adaptability, technology, and managing risks effectively. In this section, we explore the challenges and complexities that purchasing and supply management professionals encounter, exploring the intricacies that arise with each area. By recognizing these challenges and understanding their impact, organizations can proactively develop solutions and optimize practices to drive successful outcomes in the dynamic realm of purchasing and supply management.
Globalization and supply chain complexity
Globalization and supply chain complexity have a profound impact on businesses today. As companies expand their operations across borders, supply chains become increasingly intricate and interconnected. This complexity arises from diverse factors such as global sourcing, multiple transportation modes, varying regulatory environments, customs, multiple currencies, and ensuring supply chain transparency and traceability – all which present significant challenges. The impact is felt throughout the entire supply chain, affecting inventory management, lead times, supplier relationships, and risk management. Globalization offers opportunities for market expansion and cost efficiencies while also introducing challenges like longer lead times, increased vulnerability to disruptions, and the need for effective coordination throughout the business. To thrive in this dynamic environment, organizations must develop robust strategies, embrace technology, foster collaboration, and maintain adaptability to mitigate risks and capitalize on the benefits that globalization and complex supply chains can offer.
Supplier selection and management
Identifying reliable and high-quality suppliers is crucial, but it can be challenging. The right suppliers can contribute to the organization’s operational efficiency, product quality, innovation, and competitiveness. Effective supplier selection ensures that partners align with the company’s strategic goals, meet quality standards, offer competitive pricing, and provide reliable delivery. On the other hand, poor supplier management can lead to supply chain disruptions, quality issues, missed deadlines, and increased costs. Developing strong supplier relationships, fostering open communication, and implementing performance monitoring systems are essential for maintaining a collaborative and mutually beneficial partnership. By carefully selecting and effectively managing suppliers, organizations optimize their supply chain, reduce risks, enhance product offerings, and gain a competitive advantage.
Cost control and price volatility
The fluctuating costs of raw materials, transportation, and market dynamics pose challenges for purchasing professionals. Balancing cost reduction initiatives while ensuring quality and timely delivery is delicate. Volatile market conditions, such as sudden price hikes or shortages, can disrupt supply chains and require proactive risk management strategies.
Effective cost control measures allow organizations to optimize expenses, improve operational efficiency, and enhance their bottom line. By closely monitoring and managing costs, businesses achieve competitive pricing, better profit margins, and increased financial stability. However, price volatility, which refers to the unpredictable fluctuations in the cost of raw materials, transportation, and market dynamics, presents challenges. It can disrupt supply chains, squeeze profit margins, and require organizations to adapt pricing strategies swiftly. Navigating price volatility requires proactive risk management, strategic sourcing, negotiation skills, and supply chain resilience to mitigate the impact of price fluctuations and maintain profitability. By understanding the total or landed cost of goods, implementing robust cost control practices, and managing price volatility, businesses can achieve financial stability, remain competitive, and position themselves for long-term success.
Technological advancements
From enhanced communication and collaboration to streamlined processes and improved data analysis, technology drives efficiency, productivity, and innovation. Technology automates manual tasks, reduces errors, and accelerates the speed of operations, leading to increased productivity and cost savings. Moreover, technology provides valuable insights through data analytics, empowering organizations to make informed decisions and drive strategic initiatives. It enables seamless connectivity, facilitates remote work, and expands global reach.
Embracing technological advancements is no longer an option but a necessity for organizations to stay competitive, adapt to changing market dynamics, and unlock new opportunities for growth and success.
Risk management and resilience
Purchasing professionals mitigate potential disruptions and avoid costly setbacks by proactively identifying and assessing risks related to suppliers, market conditions, geopolitical factors, and regulatory compliance. Implementing risk management strategies, such as diversifying supplier networks, developing contingency plans, and establishing robust contract terms, enhances the resilience of the purchasing function, enabling organizations to respond effectively to unforeseen events, maintain continuity of supply, and uphold customer commitments. By integrating risk management and resilience into purchasing management practices, organizations can minimize vulnerabilities, protect against supply chain disruptions, and optimize their procurement operations for sustained success.
The role of technology in purchasing and supply management
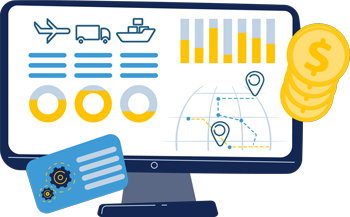
Navigating the challenges and complexities of purchasing and supply management requires a proactive and adaptive approach. However, the ever-evolving landscape of technology presents innovative solutions to address these challenges.
The role of technology in purchasing and supply management cannot be overstated. Technology, specifically purchasing and supply management software, offers a range of tools and capabilities that streamline processes, enhance data analysis, improve communication, and provide unprecedented visibility across the supply chain. By embracing and leveraging a procurement management system, purchasing professionals overcome obstacles, drive efficiency, and unlock new possibilities in their quest for effective procurement and supply chain management.
Let us now examine the transformative power of technology in empowering purchasing professionals and revolutionizing the landscape of purchasing and supply management.
Streamlining procurement processes for optimal performance
Purchasing and supply management software streamlines procurement processes by providing a centralized platform for managing requisitions, supplier information, and purchase orders, automating routine tasks, such as approval workflows and invoice processing, reducing manual effort, and minimizing errors. The software facilitates streamlined supplier management through a centralized supplier database, enabling efficient collaboration, tracking supplier performance, and managing contracts.
Additionally, purchasing and supply management software offers features for cost management, spend analysis, and integration with QuickBooks, ensuring data consistency, improving decision-making, and enhancing overall procurement efficiency and effectiveness. Automating and optimizing key procurement activities, purchasing, and supply management software enables organizations to streamline processes, reduce costs, and drive better outcomes throughout the procurement cycle.
Fostering strong partnerships through enhanced supplier management and collaboration
Purchasing and supply management software greatly assists with supplier management and collaboration by providing a centralized platform for maintaining supplier information. The software streamlines the supplier onboarding process, simplifying the establishment and maintenance of a comprehensive supplier database, enabling purchasing professionals to monitor supplier performance metrics, track key performance indicators, and assess compliance with contractual obligations.
Additionally, the purchasing and supply management software facilitates collaboration through document sharing and real-time updates on orders and deliveries. By enhancing supplier management and collaboration, the software strengthens relationships, improves transparency, and enables efficient communication, leading to more effective procurement outcomes and stronger partnerships with suppliers.
Unlocking actionable intelligence by harnessing data analytics
Purchasing and supply management software is pivotal in data analytics by capturing, analyzing, and providing valuable information for informed decision-making. The software collects and aggregates procurement data from various sources, enabling purchasing professionals to analyze spending, identify cost-saving opportunities, and track key performance indicators. Through customizable reports, interactive dashboards, and data visualization tools, the software presents data in a clear and actionable format, allowing procurement professionals to gain meaningful insights into supplier performance, market trends, and procurement patterns. By leveraging data analytics capabilities, purchasing and supply management software empowers professionals to make data-driven decisions, optimize procurement strategies, and continuously improve processes for enhanced efficiency and effectiveness.
Driving profitability through precision demand forecasting and inventory optimization
Purchasing and supply management software collects historical sales data, trends, and other relevant factors to generate demand forecasts assisting purchasing professionals in determining optimal order quantities and avoiding stockouts or excess inventory. Additionally, real-time visibility into inventory levels and alerts for low stock and reorder points allow organizations to optimize inventory levels, reduce carrying costs, and ensure products are available when needed, resulting in improved inventory efficiency and customer satisfaction.
Mitigating uncertainties and risk through centralized operations
Centralizing supplier performance history, inventory management, and order management in a purchasing and supply management system greatly assists purchasing managers with risk management. Purchasing and supply managers can assess the overall risk associated with each supplier by having a centralized repository of supplier performance data, including metrics such as delivery reliability, product quality, and responsiveness. Procurement professionals can identify potential red flags, evaluate supplier performance trends, and make informed decisions about continuing or discontinuing supplier relationships based on their risk profiles.
Additionally, having a centralized system for inventory and order management allows purchasing managers to monitor inventory levels, track order statuses, and anticipate potential supply chain disruptions or delays. By proactively managing inventory and order processes, purchasing managers mitigate risks associated with stockouts, production delays, or excessive carrying costs. Overall, centralizing these crucial elements within a comprehensive system empowers purchasing managers to proactively identify and manage risks, enhancing the overall risk management capabilities of the organization.
Conquering boundaries and navigating the global supply chain
By leveraging the capabilities of purchasing and supply management software, organizations overcome the complexities associated with globalization and supply chain management. The software enhances visibility, streamlines communication, facilitates risk management and enables proactive decision-making, ensuring businesses can effectively navigate the challenges of operating in a global marketplace. Purchasing and supply management software enables organizations to collaborate effectively across time zones and locations, buy (and sell) in multiple currencies, track the movement of goods, identify and mitigate risks, manage compliance with international regulations, enhance traceability, and gain actionable insights.
Purchasing and supply management case studies
The following two case studies highlight the positive impact of implementing inventory, order, and purchasing management software to drive efficiency, profitability, and continued growth.
Transforming operations: Streamlining inventory, purchasing and supply management for China Auto Group
Like many growing businesses, China Auto Group faced numerous challenges in managing its complex supply chain, multiple warehouses, and diverse product lines using Excel spreadsheets and QuickBooks. They needed a comprehensive solution to streamline their operations, improve inventory management, and enhance purchasing and supply management.
By implementing a complete inventory, purchasing, and order management system, China Auto Group experienced significant improvements in its operations. The software provided them with accurate and up-to-date inventory information, enabling better inventory control, reducing stockouts, and improving overall order fulfillment. Enhancing visibility into their supply chain enables China Auto Group to track products across multiple warehouses, optimize stock levels, and ensure efficient logistics management.
Read the full China Auto Group case study.
Driving efficiency and customer satisfaction: Cantrell Turf Equipment’s journey with streamlined purchasing and inventory management
Facing challenges with manual processes, limited visibility, and inefficiencies in their operations, Cantrell Turf Equipment sought a solution to improve operations and customer service.
Cantrell Turf Equipment experienced remarkable improvements across various aspects of its business, including purchasing and supply management, by implementing a comprehensive order, inventory, and purchasing software system. The software provided them with real-time inventory visibility, enabling better inventory control, accurate stock tracking, and streamlined order processing, resulting in improved customer service and reduced stockouts.
Software played a vital role in transforming Cantrell Turf Equipment’s operations by improving inventory management, enhancing purchasing and customer service, and driving overall efficiency.
Read the full Cantrell Turf Equipment case study.
Call us at 817-870-1311