Spare Parts Management System: The Backbone of Operational Efficiency
Built For
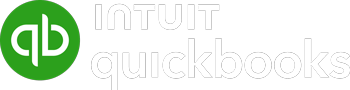
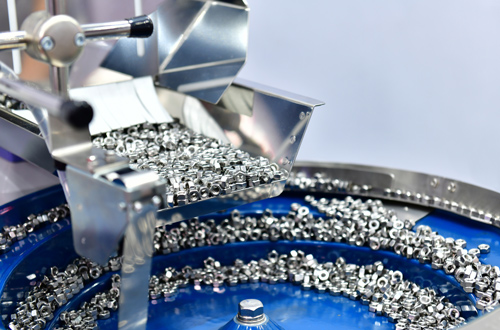
What is a Spare Parts Management System?
Spare parts are the lifeblood of organizations that depend on machinery and technology to achieve their business goals. A spare parts management system is an end-to-end solution that controls the flow of spare parts through the supply chain, from forecasting demand to the eventual delivery of the parts.
A spare parts management system comprises many functionalities, such as demand forecasting, purchasing management, inventory control, order management, and data-driven decision-making facilitated by intuitive dashboards. This article dives into these critical aspects, shedding light on how they synergize to form an indispensable organizational tool.
The Art and Science of Forecasting Demand
Accurately predicting the need for spare parts is pivotal for any efficient spare parts management system. Inadequate forecasting can lead to overstocking, thereby increasing holding costs or understocking, resulting in production delays. A spare parts management system provides accurate, data-driven forecasts based on historical information and trends that help organizations predict future spare parts inventory needs more efficiently and cost-effectively.
A critical aspect of supply chain management, demand forecasting assists with:
Inventory Optimization
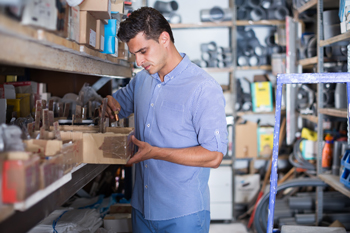
Accurate demand forecasting helps maintain the correct inventory levels, reducing holding costs and the risks associated with overstocking or understocking.
Resource Allocation
Knowing future demand allows for better planning and allocation of resources, such as labor and manufacturing capacity, leading to improved operational efficiency.
Strategic Planning
Forecasting demand over different time horizons provides valuable insights for both short-term operational plans and long-term strategic planning, including market expansion and capital investment.
Improved Customer Satisfaction
Accurate forecasts mean that the right products are available when customers want them, leading to higher customer satisfaction and loyalty.
Cost Savings
Organizations can significantly reduce operational costs by aligning production schedules, workforce, and raw material procurement with accurate demand forecasts.
Purchasing Management: The cornerstone of efficiency
Once demand is forecasted, the next critical step is purchasing management. This function of a spare parts management system involves selecting suppliers, negotiating terms, and overseeing supplier reliability. Efficient purchasing management reduces lead times and optimizes costs, ensuring that the correct parts are available at the right time. A spare parts management system’s capabilities help compare supplier performance and prices, facilitating more informed decision-making.
Effective purchasing management offers numerous benefits, including:
Cost Optimization
One of the most apparent benefits is the opportunity for significant cost savings through bulk purchases, negotiated discounts, and strategic sourcing from low-cost, high-quality suppliers.
Enhanced Supplier Relationships
Establishing long-term partnerships with suppliers ensures a stable supply chain, better credit terms, and opportunities for future collaborations.
Risk Mitigation
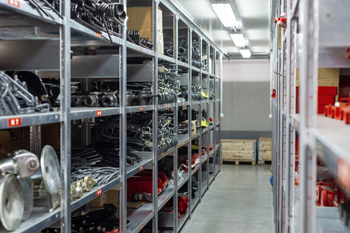
Effective purchasing management allows organizations to assess and manage risks related to supply chain disruptions, price volatility, and quality issues, thereby ensuring a more resilient operation.
Improved Quality Control
By working closely with trusted suppliers, companies maintain better control over the quality of goods purchased, ensuring that the end product meets or exceeds quality standards.
Streamlined Operations
A spare parts management system reduces process inefficiencies, enabling quicker decision-making and smoother operations, which is particularly beneficial for just-in-time inventory systems.
Competitive Advantage
Effective purchasing strategies yield cost benefits and product development innovations, ultimately offering a competitive edge in the market.
Data-Driven Decisions
Advanced spare parts management systems are equipped with analytics tools that provide insights into spending patterns, supplier performance, and market trends. This data can be leveraged to make more informed decisions, enhancing operational efficiency.
Inventory Control and Storage: Where every square foot counts
Managing inventory is a complex undertaking that extends far beyond the basic concept of stocking items on shelves. A well-designed spare parts management system considers various metrics such as usage rates, criticality, and lead times for spare parts. Understanding these elements allows organizations to implement a dynamic stocking strategy that ensures the most frequently used and critical parts are easily accessible, minimizing retrieval times and making the most of valuable storage space, thereby reducing overhead costs.
In addition to these considerations, the lot and batch tracking concept adds another layer of sophistication to inventory control. Lot tracking enables organizations to trace parts back to their original production run, offering insights into both quality and origin, which is particularly useful in industries where compliance with quality standards is paramount, such as healthcare and aerospace, helping with recalling specific lots if a defect or quality issue arises, without affecting the entire inventory. Batch tracking, often used for items with expiration dates, allows organizations to manage stock based on batches and helps ensure that parts are used, sold, or disposed of within their shelf-life. Both these tracking methodologies provide a granular view of inventory, facilitating more effective quality control and risk management.
By embracing these advanced techniques in inventory control, organizations can unlock a host of benefits from a spare parts management system, including:
Reduced Carrying Costs
Optimized inventory levels mean less money is tied up in stock, resulting in lower carrying costs, which include storage, insurance, and personnel expenses.
Enhanced Traceability and Compliance
Tracing parts back to their original production run or batch through lot and batch tracking ensures compliance with industry standards and regulations, a critical component in healthcare, aerospace, and automotive sectors.
Quick Response to Quality Issues
Lot and batch tracking facilitates quick and targeted recalls or quality checks, minimizing disruption to operations and potential reputation damage.
Improved Stock Accuracy
Advanced inventory techniques provide real-time updates on stock levels, leading to more accurate demand forecasting and purchasing decisions.
Minimized Stockouts and Overstocking
By aligning inventory levels closely with demand, organizations can minimize the costly problems of stockouts and overstocking, thus ensuring higher customer satisfaction.
Increased Operational Efficiency
Streamlined spare parts management systems use advanced techniques to improve the efficiency of warehouse operations by reducing retrieval times and making optimal use of storage space.
Sustainability Benefits
Efficient inventory management leads to less waste in terms of expired or obsolete parts and the energy costs associated with storing them, contributing to an organization’s sustainability goals.
Order Management and Distribution: The Final Frontier
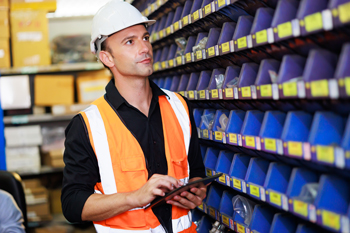
After procurement and inventory management comes the equally crucial order management and distribution process. A spare parts management system facilitates easy order management and tracking from order placement to delivery, enhancing the end-user experience and allowing quicker response times in cases of incorrect deliveries or product defects. In a nutshell, effective order management and distribution are essential for ensuring that the spare parts reach their destination in the shortest time possible while adhering to quality standards.
A high-performing order management and fulfillment process provides a range of benefits that impact both operational efficiency and customer satisfaction, including:
Enhanced Customer Experience
A seamless and quick order management process ensures customers receive their products promptly, improving customer satisfaction.
Reduced Operational Costs
Automated and streamlined order processes significantly lower the cost per transaction, as fewer manual interventions and errors mean reduced need for rework and adjustments.
Real-Time Visibility
High-performing order management systems offer real-time tracking and analytics, giving customers and businesses up-to-date information on order status, inventory levels, and other critical data.
Scalability
A spare parts management system adapts to increased orders or complexity, allowing the business to grow without a proportionate increase in operational challenges or costs.
The Power of Data: Dashboards and real-time visibility
In this age of information, data is king, and this is especially true for spare parts management systems. Real-time dashboards offer invaluable insights into inventory levels, order statuses, and performance metrics. This data-driven approach aids in proactive decision-making and enables organizations to fine-tune their procurement, stocking, and distribution strategies. By continually measuring performance against set benchmarks, companies can achieve operational excellence.
Call us at 817-870-1311