What is Kitting and Assembly?
Built For
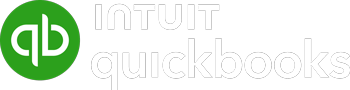
Matt Allen, Account Executive of Acctivate inventory software breaks down both manufacturing methodologies, exploring their differences through their processes, benefits, and common uses.
What is Kitting and Assembly?
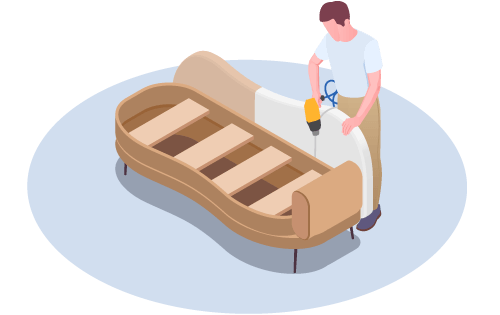
In modern manufacturing, two processes play pivotal roles: “Kitting,” or products made on demand, and “Assembly,” or products made to stock. These methodologies streamline production and adapt nimbly to consumer demands and market dynamics.
Kitting is a responsive approach where products are assembled only after an order is placed. This ensures that every component—from a couch frame to its fabric—is selected to meet specific customer preferences. This process maximizes flexibility and minimizes inventory overhead by using Bill of Materials (BOM) software to dynamically manage resources.
Conversely, assembly represents a more traditional model where products are assembled ahead of time, based on forecasted demand, and stored as finished goods. This approach is exemplified by prepared and packaged items ready to ship upon order, ensuring quick delivery and high customer satisfaction.
Throughout this article, we’ll explore these critical manufacturing processes, discuss their benefits, and consider their future evolution. By understanding the nuances of kitting and assembly, businesses can better align their operations with their strategic goals, enhancing efficiency and customer engagement.
Kitting: Made on Demand
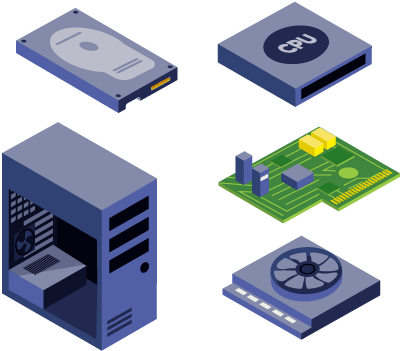
In manufacturing, kitting is a highly strategic approach tailored to meet specific customer needs with precision and efficiency. This process, often steered by advanced Bill of Materials (BOM) software, involves preparing products by assembling their components only when an order is placed. Let’s dive deeper into how this process unfolds and why it benefits modern businesses.
The Kitting Process
- Order Receipt: The kitting process kicks off when a customer places an order. Unlike traditional inventory methods, kitting does not begin until this crucial interaction occurs, ensuring all components are assembled based on current and specific demand.
- Component Selection: The necessary components are identified and selected based on the customer’s specifications. For instance, if the order is for a customizable couch, components like the couch frame and selected fabric are picked from the inventory.
- Assembly: These selected components are then assembled into a complete product. This step is critical as it combines various individual parts into a coherent unit that meets the customer’s exact requirements.
- Packaging and Shipping: Once assembled, the product is promptly packaged and prepared for shipment. The quick transition from assembly to shipping underscores the efficiency of kitting, minimizing storage time and reducing the cost associated with holding inventory.
Benefits of Kitting
- Inventory Management: Kitting reduces the need to maintain large stocks of pre-assembled products, as components are only used as needed. This not only decreases storage costs but also reduces the risk of overproduction.
- Customization and Flexibility: Since assembly occurs post-order, kitting allows for high levels of customization. Businesses can also adapt quickly to changes in customer preferences without the risk of outdated inventory.
- Efficiency and Speed: By assembling products on demand, companies streamline their operations, reducing the time between order receipt and product delivery. This efficiency is a significant advantage in industries where lead time can be a critical competitive factor.
- Reduced Waste and Enhanced Adaptability: Kitting allows for more accurate inventory forecasts and less waste since components are stored and used based on actual demand rather than predictions. This adaptability is particularly useful in industries experiencing rapid changes in consumer preferences.
Common Uses of Kitting
Kitting is commonly employed in industries that prioritize product customization, such as electronics, automotive, and furniture manufacturing. These sectors benefit from the ability to offer personalized products without the logistical nightmares of traditional inventory management.
Assembly: Made to Stock
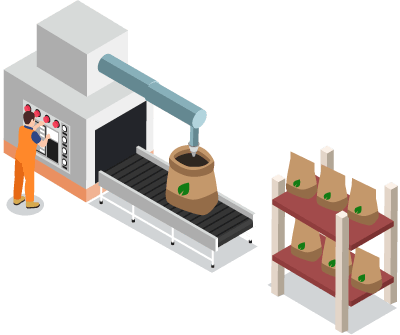
Assembly, or “Made to Stock” manufacturing, is a classic approach where products are assembled from their components in advance and stored as finished goods, ready for immediate shipment upon order. This method is widely utilized across industries to streamline operations and respond quickly to customer orders. Let’s explore the significance of the assembly process in today’s manufacturing landscape.
The Assembly Process
- Component Sourcing and Inventory: The first step in assembly involves sourcing and receiving components from various suppliers. For example, components might be procured from different vendors and stored in inventory.
- Product Assembly: Once all necessary parts are in stock, assembly begins. This stage transforms individual components into a complete, market-ready product.
- Quality Control: After assembly, each product undergoes a thorough quality check to ensure it meets all specifications and quality standards– crucial for maintaining customer satisfaction and reducing the likelihood of returns.
- Packaging and Storage: Completed products are packaged, labeled for sale, and stored in the warehouse as part of the finished goods inventory.
- Order Fulfillment: Upon receipt of a customer order, the finished product is retrieved from inventory, and the order is shipped. This process highlights the advantage of the assembly method—products are immediately available to meet customer demand.
Benefits of Assembly
- Quick Response to Customer Orders: Since products are already assembled and stocked, companies can quickly fulfill orders, enhancing customer satisfaction through reduced lead times.
- Economies of Scale: Assembly allows for mass production, reducing the cost per unit, making this process economically advantageous for products with stable demand.
- Simplified Inventory Management: Tracking finished goods can be simpler than managing numerous individual components, especially when products are standardized.
- Predictability and Consistency: With products assembled and ready to go, companies can ensure consistent quality and availability, aligning closely with customer expectations and demand forecasts.
Common Uses of Assembly
Assembly is particularly beneficial in industries where products are often standardized and produced in large volumes. This method supports businesses in maintaining a ready supply of products, facilitating quick distribution channels and efficient customer service.
Comparison of Kitting vs. Assembly
While both kitting and assembly are crucial in manufacturing, they cater to different operational strategies and customer needs. Understanding the distinctions between these two processes can help businesses choose the most effective approach for their specific circumstances. Here’s a breakdown of each method’s key differences and situational preferences.
Key Differences Between Kitting and Assembly
- Inventory Management: Kitting does not require the pre-assembly of products; components are stored separately and assembled only after an order is placed. This approach minimizes inventory costs and reduces the risk of overstocking. In contrast, assembly involves creating finished products in advance, which require storage until sold, potentially increasing inventory holding costs.
- Customization and Flexibility: Kitting excels in environments where customization and personalization are high priorities. Since assembly occurs post-order, businesses can offer a broader range of product variations without significantly increasing production costs. Assembly, however, is less flexible in this regard, as changes to the product require altering the entire production line, which can be costly and time-consuming.
- Lead Times and Responsiveness: Assembly can provide shorter lead times for customer orders since products are ready to ship immediately. This is advantageous for products with predictable demand and shorter sales cycles. While potentially slower, kitting offers responsiveness to customer specifications, making it ideal for made-to-order products or where demand is less predictable.
- Scalability and Production Costs: Assembly reduces the cost per unit as production volume increases. This makes it suitable for high-volume, low-variability products. On the other hand, kitting can sometimes involve higher per-unit costs due to the less predictable nature of orders and the need for more complex inventory management.
Situational Preferences
Kitting is preferred when:
- Customization is vital to meeting customer demands.
- The product range is diverse, with numerous possible configurations.
- Inventory costs must be minimized, especially in businesses with limited storage space.
Assembly is preferred when:
- Demand is stable and predictable, allowing for efficient mass production.
- Quick delivery is crucial to customer satisfaction.
- Products are less complex and require standardization for mass market appeal.
Strategic Considerations
Businesses must consider their market demands, production capabilities, and strategic goals when choosing between kitting and assembly. For instance, a company specializing in bespoke furniture may find kitting more aligned with its business model, while a manufacturer of standard electronic gadgets might benefit more from assembly.
Case Study: Green Forest Cabinetry – Excelling Through Kitting
Company Overview
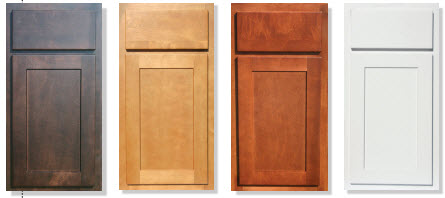
Green Forest Cabinetry, based in Chesapeake, Virginia, with an additional location in Florida, is renowned for its high-quality, easy-to-assemble, and affordable custom cabinets. It serves both homeowners and businesses. Matt Eykamp, IT Manager at Green Forest Cabinetry, describes its mission as “designing, manufacturing, and importing exceptional quality cabinetry,” emphasizing excellent customer service and thoughtfully designed products.
The Challenge
Initially, Green Forest Cabinetry utilized QuickBooks® Enterprise for inventory control. However, as the company grew, it encountered significant limitations with the software’s inventory capabilities, leading to operational frustrations. Eykamp noted, “It had many limits and was not a proper fit for our business.” Recognizing the need for an upgrade, the company focused on finding a solution that could enhance accuracy and simplify order processing, increase the speed and versatility of the software, and improve customer satisfaction.
The Solution
The search for a better system led Green Forest Cabinetry to adopt Acctivate, a software equipped with intelligent features to boost efficiency and support growth while saving time and money. With tools like the Order Manager and Shipping Workstation, as well as integration with the multi-carrier shipping solution StarShip, Acctivate has transformed its order fulfillment process. “We’re processing more orders with greater ease, we’re shipping two-thirds more than before – it’s more accurate, it’s better,” Eykamp explained.
Kitting: A Strategic Advantage
A pivotal aspect of Green Forest Cabinetry’s success with Acctivate is the implementation of kitting. Kitting allows the company to maintain flexibility in inventory management by not dedicating components to a finished product until an order is received. This approach is especially beneficial given their product range, which includes multiple cabinet colors of the same style where only the color component differs. “With Acctivate, we’re able to kit with ease… Kitting simplifies our product structure and it’s very flexible. The kitting is huge for us now,” Eykamp highlighted.
Impact
Adopting kitting has streamlined Green Forest Cabinetry’s production process and enhanced its ability to efficiently meet diverse customer demands. The flexibility afforded by kitting ensures that inventory is used optimally, reducing waste and improving the overall efficiency of their operations. As a result, Green Forest Cabinetry continues to thrive, delivering custom solutions with improved speed and precision, significantly boosting customer satisfaction and company growth.
Case Study: DeLorean Motor Company – Streamlining Assembly with Acctivate
Company Overview
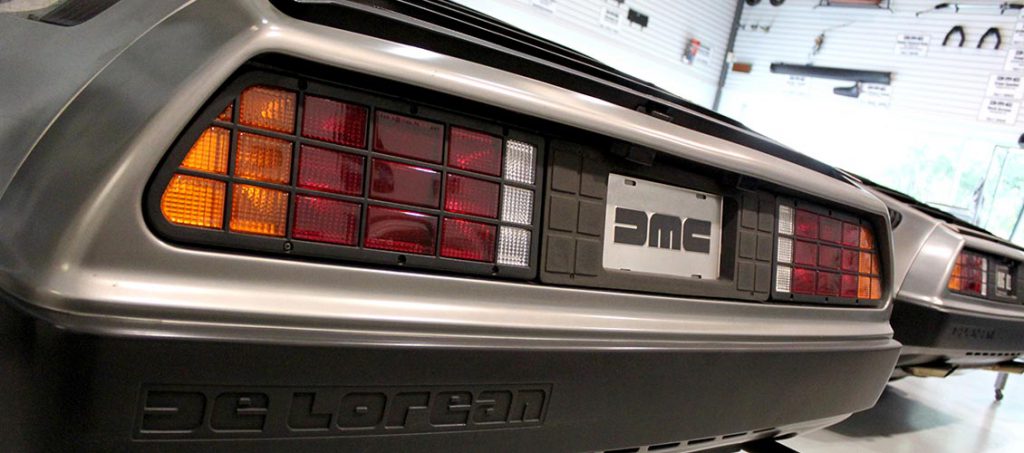
The DeLorean Motor Company, with a rich legacy tied to innovation and iconic styling, has established itself as a central figure in maintaining and revitalizing DeLorean vehicles. Led by Stephen Wynne, who embraced the challenge of preserving this unique brand since acquiring its remaining inventory and rights in the late 20th century, DMC has been dedicated to providing top-quality parts and services to DeLorean enthusiasts worldwide.
The Challenge
Maintaining a legacy as distinct as the DeLorean’s requires passion, precision, and efficiency in managing a vast inventory of unique parts and executing complex assemblies. The company needed a robust system that could handle these demands seamlessly to keep up with servicing existing vehicles and producing new parts.
The Solution
Since 2006, DeLorean Motor Company has been leveraging Acctivate Inventory Management Software to enhance its operational capabilities. Acctivate’s assembly feature has transformed how DeLorean handles the production of new parts. According to a company mechanic, the software makes it possible to efficiently assemble multiple parts into a new product. “I can put different parts and products together to make a new product using the Assemblies feature in Acctivate. Once I’m done with the physical assembly, I assemble it in Acctivate,” he explained.
The Assembly Process
The assembly feature in Acctivate allows DeLorean staff to streamline the creation of new assemblies. For example, a mechanic might need to combine 20 different components to assemble a particular part of the DeLorean.
Using Acctivate, the process is simplified to just a few clicks: selecting ‘Inventory Assembly’> ‘New’ and adding the required parts. This automation saves significant time—about 30 minutes per assembly—and reduces the potential for error that comes with manual entry.
Benefits and Impact
- Efficiency: Acctivate’s assembly feature has significantly sped up the assembly process at DeLorean, making it easier and faster to produce the necessary parts and keep up with customer demand.
- Accuracy: With automated assembly entries, the likelihood of errors is minimized, ensuring that each part is accounted for and assembled correctly.
- Time Savings: The streamlined process saves approximately 30 minutes per assembly, allowing mechanics to focus more on quality control and less on paperwork.
Conclusion
For DeLorean Motor Company, Acctivate’s assembly features have been a game-changer. They have improved workflow and supported the company’s commitment to maintaining the legendary status of the DeLorean vehicles while ensuring that fans and owners receive the best possible service and parts. This case study showcases how integrating the right technology can facilitate more efficient assembly processes, which is crucial for businesses dealing with complex products and high customer expectations.
Call us at 817-870-1311