BOM Costs
Built For
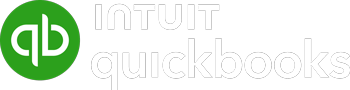
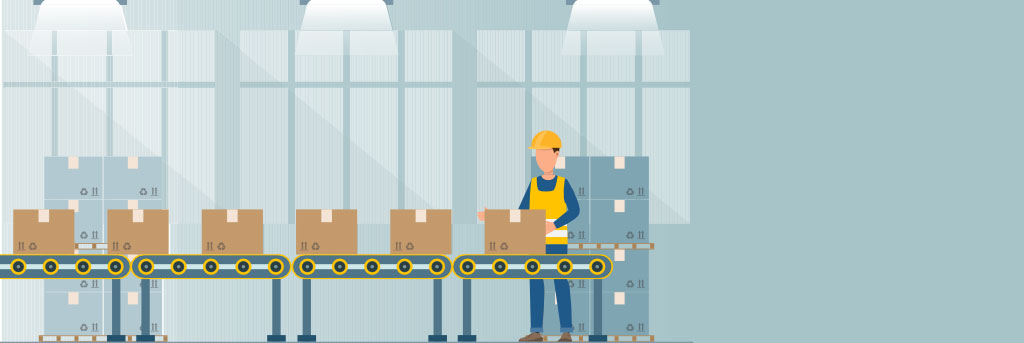
BOM Costs
A Bill of Materials (BOM) is a comprehensive list of all the components used to manufacture an assembly, a kit, and/or for finished food/beverage products via batch processing. A BOM can include raw materials, sub-components, sub-assemblies, and parts, as well as quantities, units of measure, descriptions, and any other relevant elements.
Creating and tracking accurate BOM costs is important for ensuring manufacturing processes are efficient and as cost-effective as possible. BOMs also help monitor inventory levels, improve purchasing decisions, keep workflows running smoothly on the production floor, and in the end, ensure accurate cost of goods, protect bottom lines, and expand profit margins.
With Acctivate Inventory Software, creating detailed BOMs and tracking BOM costs is straightforward. Acctivate tracks BOM costs for assemblies, kits, and finished food/beverage products. Understanding the true costs of finished goods and ensuring accurate COGs are reflected allows a business to make better-informed purchasing and manufacturing decisions, especially when all necessary data is stored in one, central location (Acctivate).
BOM Costs & Assemblies
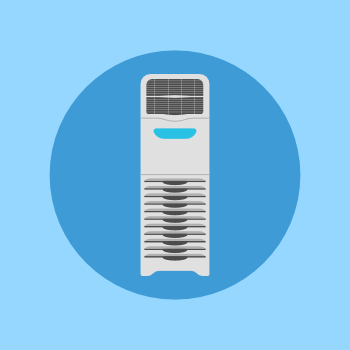
Assemblies are typically “made-to-stock inventory.” When an assembly transaction occurs, components used in the assembly are removed from inventory and the assembly product is added to inventory. An assembly is a zero-sum transaction which means the sum of the component costs make up the cost of the assembly product. An assembly is added back into inventory as a new product.
Let’s say the product being assembled is an air purification system. To have the air purification system, first it must be assembled, therefore the components must be pulled from inventory to go into the assembly build. In Acctivate, the components used will be depleted from inventory; once the air purification system is built, the final product will be added into Acctivate and physically placed on warehouse shelves ready to sell. Acctivate tracks the BOM costs for the air purification system, whether one or twenty are built at a time, from start to finish.
If the assembly of a product is outsourced to a 3rd party, Acctivate’s Landed Cost module can be used to account for labor and freight charges when the bill has arrived. In this case, applying landed cost charges along with the original assembly costs provides a much more accurate view of end-unit costs.
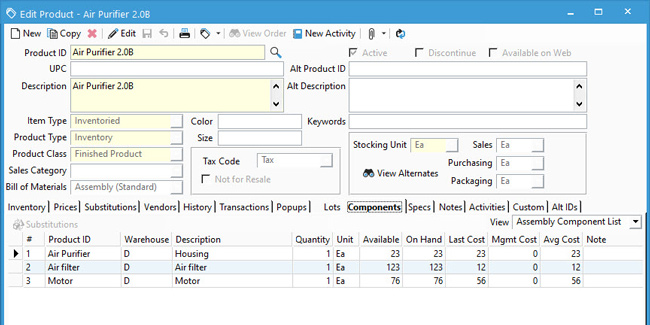
BOM Costs & Kitting
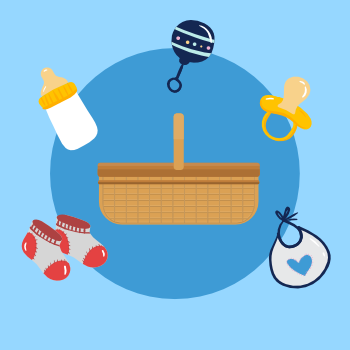
Kits are also known as “on-demand inventory.” When a kit transaction occurs, components used in the kit are removed from inventory and packaged or built together, then shipped immediately. The cost of the kit is the cost of the individual components bundled together.
For a kitting example, let’s use a gift basket. A customer can select five specific items to be included in the basket. The items are removed from inventory, placed in the basket, packaged and shipped immediately – not placed in the warehouse. The final cost of the kit (the gift basket with the items in it) would be totaled from all the components + the basket used. The cost comes from the components themselves and not the final product. In Acctivate, the gift basket would be set up as a kit, the resulting BOM costs would reflect each of the kit items being sold individually but as one product (the kit).
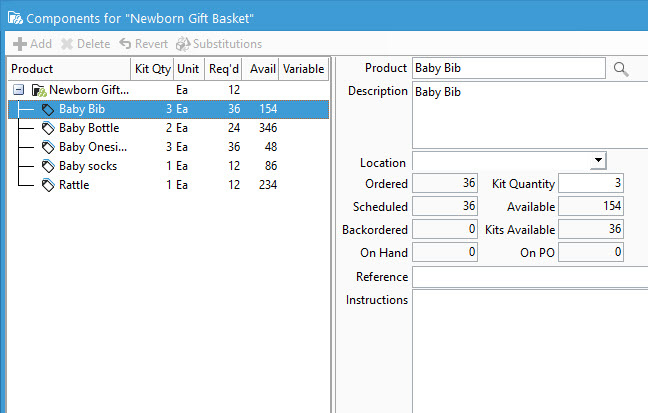
BOM Costs & Batch Process Manufacturing
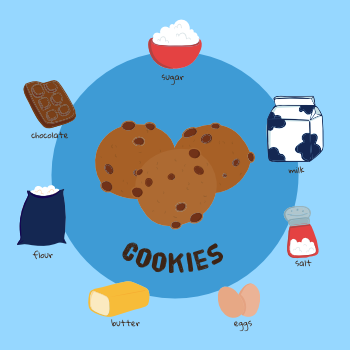
Batch processing is the method used to manufacture food and beverage products. A final food and beverage product is similar to a standard assembly because the components (ingredients) used are pulled from inventory to create the new product and then the new product is added back into inventory. The difference with a standard assembly and a food and beverage assembly is that the food/beverage assemblies are usually variable unlike standard assemblies. Recipes may vary from batch to batch, depending on situational circumstances like ingredient variations, seasonal variations, changing requirements, and substitutions. Additionally, the end product (yield) may vary as a result of changes or spillage. So, the final cost of the products can change batch to batch, unlike most other assemblies, where the amount of each component used remains the same each time.
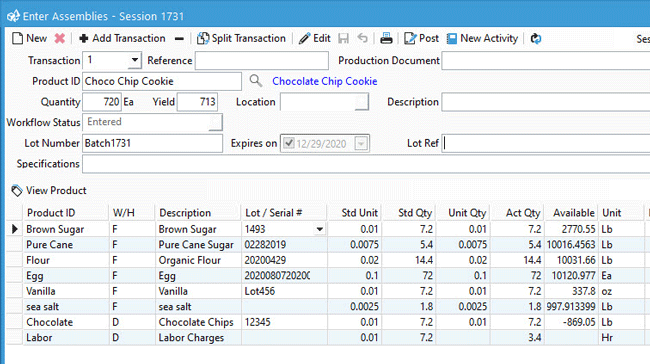
In Acctivate, the recipe/BOM for chocolate chip cookies can be stored. The ingredients will be depleted from inventory, like in a standard assembly, and re-entered as a new product. Each ingredient/component has a dropdown, allowing amounts for each component to be adjusted as needed to reflect any changes that take place during the manufacturing process, including the yield of the batch. The final unit cost will come from the components themselves and be divided by yield of the batch.
BOM Costs in Acctivate
- The Bill of Materials may be changed at any time while preserving the sales history for previously assembled or kitted products.
- A Bill of Materials may have an unlimited quantity of components.
- The components, the completed product, or both, may be serialized or lot numbered.
- Partial assemblies can be posted and the remainder can be kept in progress until ready to post.
- Adjustments to Custom Kitting can occur to make one-off changes to the quantity of kit components or add/remove components from a kit on a sales order.
- Custom manufacturing (Variable build assembly) to support component variations
- Batch process manufacturing allows for components to be adjusted based on seasonal requirements, availability, or the requirement for substitutions.
- For product produced, batch process manufacturing provides the ability to compensate for variable yield with the ability to alter the quantity produced.
Call us at 817-870-1311