7 Tips for How to Organize Parts Inventory
Built For
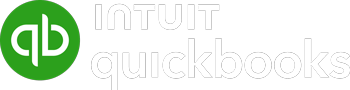
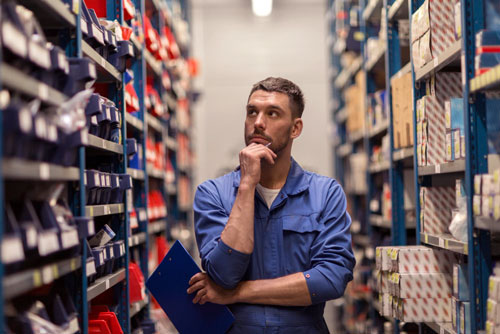
Why and how to organize parts inventory
Organizing parts inventory is crucial for any business, especially those involved in distribution, manufacturing, assembly, or repair services. Proper organization reduces time wasted searching for parts, reduces the chances of errors, and can save costs by preventing unnecessary reorders of parts lost in the inventory.
While the exact approach for how to organize parts inventory will vary depending on the size and type of your inventory, the layout of your warehouse, and other specific needs of your operation, certain methods and concepts span all parts warehouse operations, significantly enhancing efficiency, accuracy, and productivity.
How to organize parts inventory tip #1: Categorization
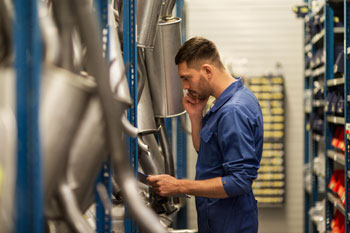
Categorizing parts based on common characteristics such as type, size, function, or application improves overall efficiency and creates a more organized and structured warehouse. Concepts and concerns to keep in mind when categorizing include:
- Establish clear categories. Create broad categories and subcategories if necessary. The aim is to create clear categories that allow a part type’s location to be known at a glance. A logical and consistent categorization system will make finding parts and tracking inventory levels easier.
- Optimize space. By categorizing parts based on size, weight, or other physical characteristics, warehouses can optimize the use of space which leads to cost savings and a safer work environment.
- Tracking demand. Categorization makes it easier to track inventory levels and reorder parts and also helps identify patterns in demand, such as which categories of parts are most popular or which tend to sit in the warehouse for a long time.
- Reduce errors. Proper categorization minimizes the risk of mistakes (like mis-picks and mis-ships) because it’s easier to locate and identify the correct item.
- Complying with regulations. Certain regulations may require specific categorizations for certain parts. For instance, hazardous materials may be required to be stored separately from other goods.
- Training new employees. When parts are categorized and organized logically, it’s easier to train new employees or temporary workers as they can quickly understand the layout of the warehouse and locate items they need.
- Auditing or counting. A systematic categorization makes it easier during audits or inventory counts to check if the inventory matches the recorded data, ensuring accountability and reducing discrepancies.
How to organize parts inventory tip #2: Label everything
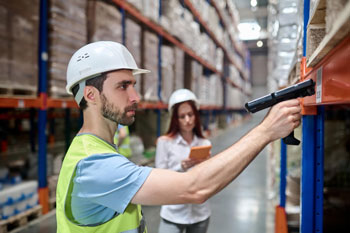
Labels play a crucial role in warehouse operations, including the organization and management of the parts inventory. Each part, shelf, and box should be marked with a unique identifier. Identifiers can be a barcode, which can be scanned for quick access to information about the part, a SKU number, or any other form of a unique ID. Labels can also include important information about the part, such as its name, category, location, descriptions, expiration dates, and special storage instructions.
Labels speed up the picking and packing process allowing warehouse employees to quickly scan a label to confirm they have the correct part rather than manually searching for the information. Additionally, labels can indicate if parts are fragile, heavy, or potentially hazardous and help ensure warehouse staff handles items correctly. Overall, labels facilitate warehouse operations, improve productivity, reduce errors, enhance safety, and enable efficient inventory management.
How to organize parts inventory tip #3: Use a bin system
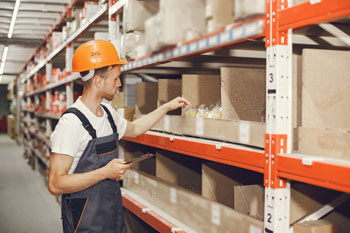
A bin system plays a pivotal role in how to organize parts inventory in warehouses or storage facilities and offers several advantages that streamline inventory management:
- Organization and structure. Each bin in a bin system represents a unique location in the warehouse. Parts are assigned to specific bins, which creates a structured, organized storage system.
- Location tracking: With a bin system, tracking the exact location of every part in the warehouse is easy, speeding up the picking process and reducing the risk of misplacing items.
- Inventory control: By allocating specific bins for different parts, inventory levels can be monitored and controlled more efficiently.
- Efficiency and productivity. Workers can find and pick items more quickly when a bin system is in place.
- Accuracy. By using a bin system, the risk of errors in picking and packing is significantly reduced. Each part has a specific location, making it easy to verify that the correct part has been picked.
- Space optimization. A bin system optimizes the use of storage space. Parts can be grouped by size, weight, or frequency of use to use the available space best.
How to organize parts inventory tip #4: Conduct regular audits
Performing regular inventory audits or inventory counts, either manually or using technological solutions like barcode scanners and inventory management software, is critical to efficient and effective inventory management. Regular inventory audits help ensure inventory records are accurate and up-to-date. Audits identify:
- Discrepancies between records and actual physical inventory due to issues like theft, damage, miscounting, or clerical errors.
- Overstocking and understocking. By verifying the quantity of inventory regularly, overstocking (where you have too much of a particular item) and understocking (where you have too little) can be reduced or prevented.
- Trends, such as parts that are selling quickly, those that are not moving, seasonal fluctuations, and more.
- Problems or inefficiencies in your inventory management system, allowing for necessary changes to improve efficiency to be made.
- Space usage issues. Inventory can be rearranged or reorganized as necessary to optimize storage space.
How to organize parts inventory tip #5: Establish a logical warehouse layout
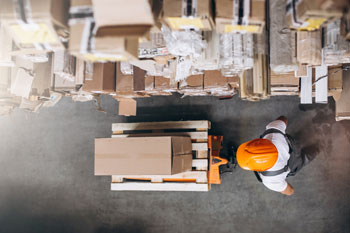
A logical warehouse layout is a key component of how to organize parts inventory and contributes to the smooth functioning of a warehouse. Significantly impacting accuracy and efficiency when picking parts, inventory should be arranged in a way that makes sense and is operationally beneficial, such as by groups of similar parts or optimized based on picking routines.
Establishing a logical warehouse layout provides various benefits to warehouse operations and overall business performance, including workflow efficiency, better space utilization, reduced operational costs, increased safety, and improved customer satisfaction.
How to organize parts inventory tip #6: Training
Warehouse staff must be trained on inventory organization methods and understand the importance of maintaining the system for organizing parts inventory.
- Understanding the system. For the inventory system to work effectively, all employees must understand how it operates, including how to use the inventory management software, label and categorize items, handle goods, and where and how to store items.
- Maintaining accuracy. Proper training helps ensure that all staff members follow the same procedures when adding new items to the inventory, picking items for orders, or updating inventory levels.
- Improving efficiency. Well-trained employees perform their tasks more efficiently, leading to faster order fulfillment and improved operational efficiency.
- Reducing errors. Mistakes in inventory management, such as miscounting items or storing items in the wrong place, leads to problems like stockouts or excess inventory.
- Standardizing operation. Training ensures employees follow the same procedures, leading to consistency and standardization in inventory management operations.
Effective training is an ongoing process. As new employees are hired, procedures are updated, and new technologies are introduced, additional training will be needed to ensure everyone understands how to manage and organize the parts inventory.
How to organize parts inventory tip #7: Implement inventory management software
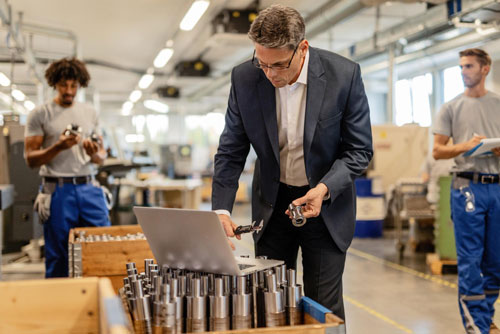
While it’s possible for smaller businesses with less complex inventory needs to organize parts inventory without inventory management software, it will typically be more time-consuming and, most likely, less accurate.
By using inventory software, such as Acctivate, businesses have better control over their parts inventory, leading to improved operations, customer satisfaction, and ultimately, their bottom line, with many inventory management processes and tasks automated and valuable insights for decision-making gained.
Acctivate inventory management software for organizing parts inventory
A leader in providing parts inventory management solutions, Acctivate delivers a wide range of features to help businesses effectively organize and manage their parts inventory, including:
- Real-time inventory management with inventory levels updated as parts are received or sold, reducing the risk of stockouts or overstocking.
- Multiple location management for inventory tracking across multiple locations, especially useful for businesses with more than one warehouse or storage facility.
- Lot and serial number tracking, crucial for businesses that need to track specific batches of parts or individual items for quality control, recall management, or warranty purposes.
- Barcode scanning. Acctivate integrates with barcode scanning systems to facilitate efficient and accurate inventory updates.
- Reorder point alerts when inventory levels fall below a predetermined threshold, helping to prevent stockouts.
- Landed cost tracking associated with each part, such as cost of the product, transportation fees, customs, duties, taxes, insurance, currency conversion, crating, handling, and payment fees.
- Integration with QuickBooks, allowing for a seamless flow of inventory, order, and financial data between Acctivate and QuickBooks.
- Reporting and analytics tools for better understanding inventory and making data-driven decisions.
Built for QuickBooks, Acctivate helps businesses maintain better control over their parts inventory, improve operational efficiency, and make informed decisions to optimize inventory management.
Call us at 817-870-1311