What is inventory management?
Built For
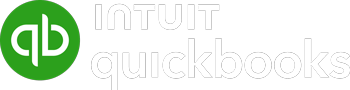
What is inventory management?
and discusses:
- Different types of inventories
- Core objectives of inventory management
- Inventory management methods and definitions
- Technological advances that simplify inventory management
It’s interesting to note how many of our customers, who previously relied solely on QuickBooks for their financials and trusty spreadsheets for everything else, have contacted us and asked, “What is inventory management?” It’s a testament to the journey many businesses undertake, reaching that pivotal moment when they recognize there’s more to scaling up than just sales and numbers. They intuitively sense the need to grasp the concept of inventory management, realizing it’s the next big step in their growth journey.
While the question and the answer to “What is inventory management?” can have many variations and complexities, let’s start by addressing the primary subject straight away.
What is inventory management?
Inventory management is the backbone of successful product-centric businesses. At its core, inventory management efficiently oversees the constant flow of goods in and out of an establishment. Whether the establishment is a wholesale, distribution, or manufacturing company, the principles of inventory management apply universally, aiming to ensure that the right products are available in the correct quantity at the right time.
But why is inventory management so crucial? Imagine running a popular online home goods website but running out of a trendy style just as demand peaks. Or consider a lighting manufacturer that has all the necessary parts to assemble a lamp except for the power plug. These scenarios highlight how inventory mismanagement can lead to missed opportunities, unsatisfied customers, and significant financial losses.
In the forthcoming sections, we’ll explore the intricacies of inventory management and examine inventory methods, benefits, and technology. Whether you’re a business owner looking to streamline your operations or an individual keen on understanding the dynamics of stock management, this article aims to answer your inventory management questions.
Understanding Inventory
Before continuing with our discussion of “What is inventory management?” we need to answer “What is inventory?” When we talk about inventory, we’re referring to the tangible goods or items a business intends to sell to consumers or use in production. It’s essentially the lifeblood of any wholesale, manufacturing, or distribution company, and managing it efficiently is crucial to ensure a smooth flow of operations and sales.
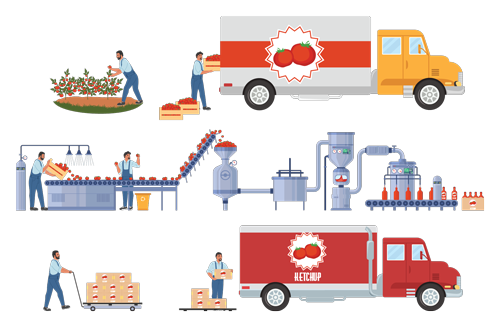
The Different Types of Inventories
- Raw Materials are the essential components or ingredients used to produce finished goods. For instance, a furniture manufacturer might have lumber as a raw material, while a bakery would stock up on flour, eggs, and sugar.
- Work-in-Progress (WIP). As the name suggests, these goods are still in production but have yet to reach their final form. For our furniture manufacturer, a half-assembled table might fall under this category.
- Finished Goods are products that are completely produced and are ready for sale. Once it’s fully assembled and polished, the table or the loaf of bread fresh out of the oven are both examples of finished goods.
It’s important to understand these distinctions because each type requires a different approach to inventory management. While raw materials must be ordered and stocked in anticipation of production, finished goods must be managed based on demand forecasts and sales patterns.
For businesses, inventory represents a significant investment. Inventory ties up capital, requires storage space, and can have associated costs like insurance, security, and potential depreciation. Risk accompanies investment, which is why understanding inventory, in all its forms and stages, is the first step toward effective inventory management.
Basics of Inventory Management
Inventory management is far more than just counting stock on shelves; it’s a multifaceted discipline that integrates various business operations, from procurement to order management and fulfillment. At its essence, inventory management aims to ensure that products are readily available when customers need them and to maintain optimal stock levels to minimize costs.
The Core Objectives of Inventory Management
- Achieving a balance between availability and cost control. One of inventory management’s primary objectives is to ensure products are available when needed, thus preventing stockouts, which can lead to missed sales opportunities and unhappy customers. However, holding too much inventory ties up capital, occupies space, and can lead to increased handling costs or potential obsolescence. The goal is to find the right balance.
- Optimized turnover. Efficient inventory management strives to maintain a healthy turnover rate, meaning that products are sold and replaced frequently, ensuring freshness for items with expiry dates and reducing storage costs.
- Loss prevention. Proper inventory management helps minimize theft, damage, or waste losses.
- Forecasting. Predicting future sales trends is integral to inventory management. Accurate forecasts allow businesses to procure products accordingly, preventing overstocking or understocking.
Inventory Management’s Role in the Supply Chain
Inventory management is just one piece of the giant puzzle that is the supply chain. The supply chain encompasses everything from raw materials sourcing to delivering the finished product to the customer. Inventory management ties into several aspects of the supply chain:
- Supplier relationships. Building solid relationships with suppliers ensures timely delivery of goods and potentially better terms and pricing.
- Warehouse management involves optimizing storage space, handling goods efficiently, and ensuring quick retrieval of products when needed.
- Demand planning involves understanding market trends, seasonal fluctuations, and customer preferences – all of which help anticipate demand.
- Distribution. Efficiently moving goods from the warehouse to retail outlets or directly to consumers.
Inventory Management Methods and Definitions
Businesses have different needs, so no one-size-fits-all approach to managing inventory exists. Over the years, various methods have been developed to help companies optimize their stock levels. Here are some of the most popular and widely used inventory management methods:
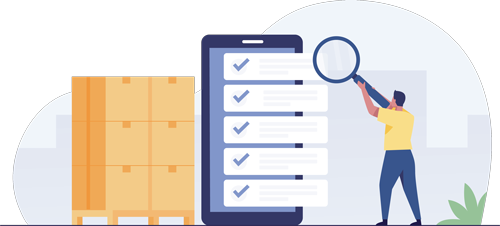
Periodic review system
This method, also called the Fixed-Interval Order System, involves reviewing the inventory at regular intervals (e.g., monthly or quarterly) and placing orders to replenish stock based on the current inventory levels. It’s a straightforward method but might not be responsive to sudden changes in demand.
Perpetual inventory system
Here, inventory levels are continuously monitored in real time. Every time a sale is made, or new stock is received, the inventory count is updated. This method is often associated with inventory management software, as it would be nearly impossible to accomplish this task manually for businesses with significant sales volumes and many product types.
Economic order quantity (EOQ)
EOQ calculates the optimal order quantity that minimizes the total costs of ordering and holding inventory. EOQ considers factors like demand rate, order cost, and holding cost to determine the ideal amount to order.
Just-in-Time (JIT) inventory management
Originating from Japanese manufacturing, JIT aims to minimize inventory levels by only ordering and producing goods as they are needed. JIT reduces carrying costs but requires a reliable supply chain.
ABC analysis
ABC analysis classifies inventory into three categories based on importance. “A” items are high-priority, often being high-value or fast-moving. “B” items are moderately important, and “C” items are less important. Resources are then allocated accordingly, focusing more on “A” items.
Safety stock
Safety stock involves keeping a buffer stock to protect against unforeseen fluctuations in demand or supply. Safety stock acts as insurance against stockouts, but deciding the right amount requires a careful analysis of demand patterns and supply reliability.
Drop shipping
Drop shipping is a method where a business doesn’t take possession of the products it sells. Instead, when a product sells, the drop shipper procures it from a third party and has it shipped directly to the customer.
Each of these methods has its advantages and drawbacks. The best method (or combination of methods) for a particular business depends on its size, industry, sales volume, and specific operational needs. Inventory management software handles many calculations and tasks associated with many of the methods.
Importance of Inventory Management
Inventory management, often deemed a backstage operation, holds center stage when it comes to ensuring the smooth running of a business. Effective inventory management gives businesses the stability and foresight to navigate fluctuations and uncertainties.
The benefits of inventory management include:
- Optimized cash flow. Money tied up in stock is money that’s not being used elsewhere. Inventory management ensures that funds are only spent on necessary stock, freeing up cash for other crucial aspects of a business.
- Enhanced customer satisfaction. We’ve all experienced this one as consumers. I recently purchased an item for a gift that appeared to be in stock on the website. A week later, when it had yet to ship, I contacted the company only to be told it was out of stock. I was not pleased. Consistently having the right products available for customers leads to fewer out-of-stocks, faster shipping times, and increased customer satisfaction and loyalty.
- Reduced holding costs. Storage isn’t free; in fact, it is pretty expensive these days. Efficient inventory practices minimize the costs of storing products that aren’t selling.
- Decreased risk of overstock and stockouts. Overstocking can lead to deadstock, which may never be sold. On the flip side, stockouts can mean missed sales opportunities. Effective inventory management strikes the right balance.
- Informed decision-making. Proper inventory tracking provides insights into which products are flying off the shelves and which are not. Real-time, accurate information is invaluable for decision-making, from procurement to marketing strategies.
- Boosted operational efficiency. Streamlining inventory processes, from reordering to warehousing, ensures operations run smoothly and efficiently.
- Scalability. As businesses grow, so do their inventory needs. A robust inventory management system scales with the company, accommodating larger product volumes and more complex supply chain requirements.
- Loss prevention. Efficient inventory tracking reduces the risks associated with theft, damages, and obsolescence.
- Improved supplier relationships. Consistent and predictable order patterns foster trust with suppliers, often leading to better deals and more favorable terms.
- Environmental responsibility. By avoiding overproduction and excess inventory, businesses can minimize waste, contributing to more sustainable practices.
Technological Advancements Simplify Inventory Management
Advanced inventory management software centralizes inventory and order management and provides users with tools that revolutionize procurement, inventory control, and order management, ensuring precision, efficiency, and real-time insights.
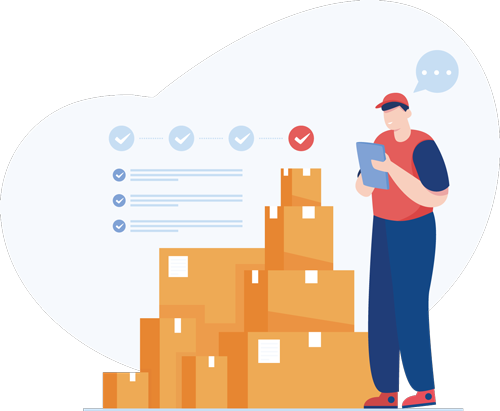
Inventory management software provides businesses with the following:
- Real-time visibility into their stock levels across multiple warehouses and locations. This dynamic view eliminates guesswork and ensures timely replenishments.
- Advanced forecasting tools to tap into historical sales data, trend analysis, and seasonal fluctuations, allowing for better-informed purchasing decisions and minimizing overstock and stockouts.
- Barcode scanning and mobile access accelerate the order fulfillment process, reduce human errors, and ensure accurate stock counts.
- Multi-channel inventory, order management, and fulfillment, centralizing orders and customer information from eCommerce platforms, online marketplaces, EDI, and direct sales channels.
- Lot and serial number tracking ensures traceability and compliance, which is invaluable for businesses dealing with perishable items or those in regulated industries.
- Multi-location capabilities offer inventory and warehouse management across multiple physical or virtual locations.
- Automated workflows ensure that tasks such as order approvals, reordering, and alerts are seamlessly executed without manual intervention.
- Seamless QuickBooks integration allows businesses to use QuickBooks for financial and payroll functionality while gaining access to advanced inventory and order management.
Summary: “What is inventory management?”
What is inventory management?
Inventory management oversees the flow of goods in and out of a company’s stock. It involves the management of raw materials, work-in-progress (WIP), and finished goods to ensure the right amount of stock at the right time to meet customer demands and operate efficiently.
Why is inventory management critical?
Effective inventory management is critical to avoid out-of-stocks and excess inventory. It ensures optimal stock levels for customer satisfaction, reduces storage costs, minimizes risk, and allows for more accurate forecasting and planning.
What are the different types of inventory?
There are three main types of inventory: 1. Raw Materials: Basic goods that are used to produce finished items. 2. Work-in-Progress (WIP): Goods are being manufactured but still need completion. 3. Finished Goods: Completed products ready for sale or distribution.
What are some standard inventory management methods?
Inventory management methods include the periodic review system, perpetual inventory system, economic order quantity (EOQ), Just-in-Time (JIT) inventory, ABC analysis, safety stock, and drop shipping.
How does technology impact inventory management?
Technology has significantly streamlined inventory management through advanced software that offers real-time stock visibility, forecasting tools, barcode scanning, automated workflows, and integration with financial systems like QuickBooks. Inventory management software improves accuracy, efficiency, and decision-making in inventory management.
Can inventory management scale with my business?
A robust inventory management system is designed to scale with your business, handling larger product volumes and more complex operations as your business grows.
How does inventory management improve customer satisfaction?
By maintaining optimal inventory levels, businesses can prevent stockouts, ensure timely deliveries, and manage customer expectations effectively, improving customer satisfaction and loyalty.
Embracing the Future of Inventory Management
As the business world hurtles forward, driven by rapid technological advancements, inventory management has undergone, and will continue to experience, a transformative evolution. We at Acctivate are happy to have contributed to merging technology with traditional inventory practices over the past decades. As we move forward, we will continue to innovate and usher in an era of even greater inventory management precision, efficiency, and adaptability.
Call us at 817-870-1311