Pick and Pack Warehouse Layout Helps Optimize KPIs
Built For
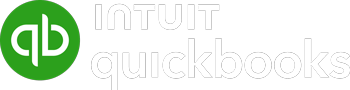
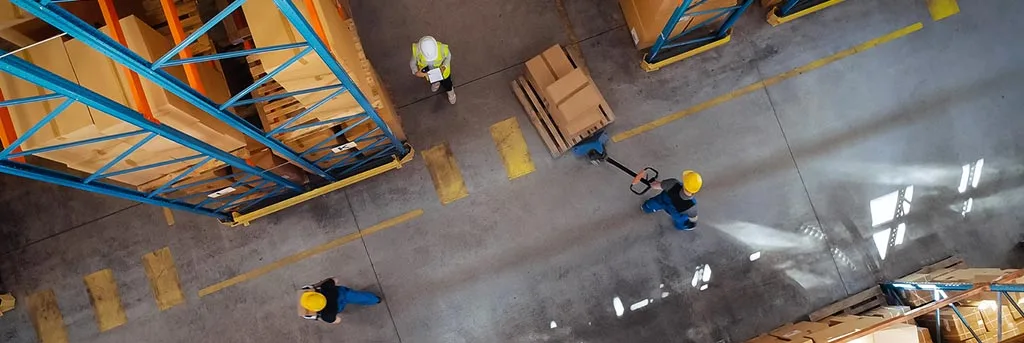
The 2021 WERC® DC Measures report reveals the operational metrics that are benchmarks for warehouses and distribution centers and which ones are prioritized.1 There are 36 total metrics that are measured, and they are grouped into categories of customer, financial, capacity/quality, inbound, outbound, perfect order index, and cash-to-cash cycle.
The top three of five metrics show that more businesses are prioritizing quality and capacity within the warehouse, and the other two focus on the customer and perfect order index:
- Average warehouse capacity used
- Order picking accuracy
- Peak warehouse capacity used
- On-time shipments
- Percent of orders with on-time delivery
Establishing an organized and ideal pick and pack warehouse layout that helps to streamline processes strengthens these metrics and other KPIs for businesses to perform at a best-in-class level.
Improve capacity and quality within the warehouse
Global B2B ecommerce operations are expected to grow to USD 25.65 trillion by 2028 from 7.72 trillion in 2021. 2 As ecommerce becomes exceedingly prevalent it is important for businesses to keep up with demand at all operational levels including the warehouse. As orders are processed, it is up to an impeccable fulfillment process to ensure customers are satisfied, especially in terms of expecting fast deliveries.
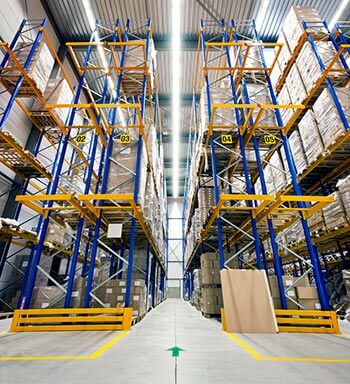
Looking at the top metrics, when figuring average and peak warehouse capacity used, businesses should ensure that they are maximizing their warehouse space properly.
- Average warehouse capacity used is the average amount of warehouse space used over a specific interval of time, i.e., monthly, or yearly.
- Peak warehouse capacity used is the amount of warehouse space used during peak seasons.
Key performance indicators of needing to optimize warehouse space is when average capacity is below 75% and peak capacity is under 85.8%.
Improvements can be made to maximize existing square footage and improve worker productivity, such as:3
- Remove excess inventory
- Select the right storage equipment
- Minimize aisle widths
- Fill open vertical space
- Slot products in optimum location sizes
- Utilize random storage method
- Perform layout assessment
The way product is stocked also makes a difference in warehouse optimization as workers navigate the area to pick and pack orders. A pick and pack warehouse layout setup that allows for pickers to retrieve high demand products easily and quickly take them to packing stations can improve fulfillment speeds to meet the high expectations of ecommerce and all sales channels.
Filling the warehouse space properly requires an essential component, an inventory management software, such as Acctivate, with real-time visibility into inventory levels to know what, when and how much to stock.
An efficient system will also enable inventory to be managed within multiple warehouses and locations within warehouses, giving way to better and faster picking processes that complement best-in-class order picking accuracy.
The order picking accuracy metric can be improved with an inventory management software equipped with mobile warehouse management that replaces inefficient manual, paper-based picking with an automated means via mobile barcoding and picklists. In Acctivate, the pick and pack warehouse layout and entire layout can be defined, which will intelligently route workers to products when picking orders and enable batch picking. With a high order picking accuracy, customers receive their order correctly and businesses don’t risk incurring additional costs and dealing with disgruntled customers.
Boost customer and perfect order index metrics
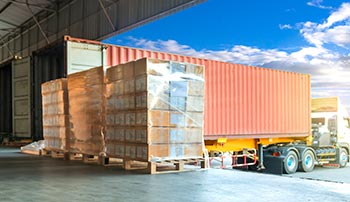
With an efficient pick and pack warehouse layout, best-in-class metrics can be achieved for on-time shipments and the percent of orders with on-time delivery. With streamlined order picking in place from better organization and the inventory management tools mentioned above, fulfillment can be completed successfully with on-time shipping and delivery.
Inventory management software makes higher on-time shipment and delivery metrics reality with tools that manage all orders in one central hub for high volume processing, integrate with shipping workstations for UPS, USPS, FedEx, and DHL, track shipments through to delivery, and enable follow-up with customers.
Call us at 817-870-1311