What is a BOM?
Built For
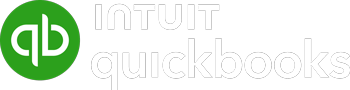
- The definition of a Bill of Materials (BOM)
- Components of a BOM
- The role of a BOM in manufacturing and engineering
- Using inventory management software for creating and managing BOMs
- Utilizing BOMs in Kitting and Assemblies
- A company’s transformation through effective BOM management
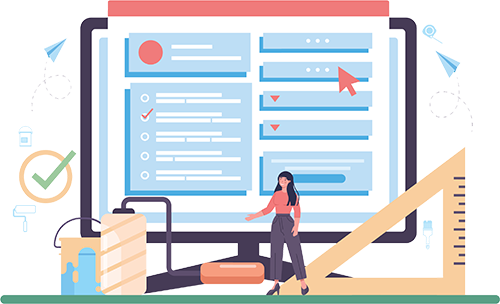
Have you ever wondered what keeps the wheels of manufacturing and engineering industries turning smoothly? A key component is a BOM, which is short for Bill of Materials. This nifty little list is like the ultimate recipe for any product, big or small, that comes out of these industries.
Now, you might be thinking, “A list? How exciting can that be?” But trust me, a BOM is more than just a list; it’s the backbone of product planning, production, and procurement. It’s like the secret sauce that ensures everything comes together just right – no missing ingredients or last-minute surprises.
In the following sections, we’ll unravel the mystery behind a BOM, why it’s such a big deal, and how it works its magic to keep everything from chairs to spaceships on track. So, buckle up and prepare for a behind-the-scenes tour of one of the most important yet often overlooked parts of the manufacturing and engineering world!
Definition of BOM
Let’s get down to brass tacks and talk about what a Bill of Materials (BOM) really is. Imagine you’re building something. A BOM is essentially your shopping list and instruction manual rolled into one. It lists everything you need – from the tiniest screw to the largest panel – and details how these parts combine to create the final product.
But a BOM isn’t just a random collection of items. It’s meticulously organized, typically showing the hierarchy of components. So, now that we’ve answered, What is a BOM? at a high level, let’s peel another layer and look at the nuts and bolts – quite literally – of what goes into these BOMs.
Components of a BOM
Just like a gourmet dish is more than just a bunch of ingredients thrown together, a BOM is more than a simple list of parts. Here’s what typically goes into a BOM:
- Part number: This unique identifier for each part helps you track and reference each item.
- Part name: This one’s pretty self-explanatory – it’s the name of the part. Simple, yet essential for clear communication.
- Description: A few words that describe what the part is or does. It’s like a mini-introduction for each item on your list.
- Quantity: How many of each part is needed. It’s crucial to get this right – imagine building a chair and realizing you’re one leg short!
- Unit of measure: This tells you how the quantity is measured – pieces, pairs, liters, etc. It’s what keeps you from ordering screws by the liter!
- Procurement type: This details whether the part is bought (like a standard screw) or made (like a custom-designed widget).
- Bill of Materials level: This shows where each part fits in the assembly hierarchy. It’s like organizing a family tree but for parts.
- Reference designators: These are used in electronics BOMs to specify where components go on a circuit board. It’s like assigning seats at a wedding but for electronic parts.
- Manufacturer: Knowing who makes the part can be crucial, especially for quality control and ordering replacements.
- Notes and instructions: Any extra bits of information that might be helpful. This could be anything from handling instructions to alternative parts if the original isn’t available.
Each component in a BOM has its role, ensuring that nothing is overlooked and that the final product comes together seamlessly. It’s like conducting an orchestra where every musician and instrument plays a vital part in creating a harmonious symphony.
In the next section, we’ll explore how BOMs are used in real-world manufacturing and engineering and why they are crucial to these processes.
The Role of BOM in Manufacturing and Engineering
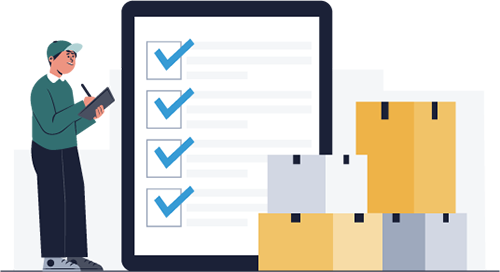
Let’s put on our hard hats and move into the industrial world to see how BOMs make themselves indispensable in manufacturing and engineering. It’s not just about having a list; it’s about the pivotal role this list plays in turning ideas into tangible products.
- Blueprint for production: A BOM acts as a comprehensive blueprint for production, guiding the manufacturing process and ensuring every component is available at the right time and place.
- Quality control: BOMs are vital in maintaining quality standards. By specifying exact parts and materials, they ensure that the finished product meets the specifications.
- Cost estimation and budgeting: BOMs are crucial in estimating the cost of a product. They provide a clear picture of all the materials and components needed, which helps in budgeting and financial planning.
- Supply chain management: Managing the supply chain becomes more manageable with a well-structured BOM. It helps in planning purchases, avoiding shortages or overstocking, and managing inventory efficiently.
- Facilitating communication: A BOM is a universal language in the world of manufacturing and engineering, ensuring everyone, from designers to factory floor workers, is on the same page.
- Enhancing productivity and efficiency: By having a detailed BOM, organizations streamline operations, reduce waste, and improve overall efficiency. Knowing exactly what you need in your kitchen before you start cooking saves time, effort, and many headaches.
Clearly, the Bill of Materials is not just a list; it’s the cornerstone of successful product development and manufacturing.
Creating, Managing, and Advancing BOMs with Inventory Management Software
In this digital age, creating and managing Bills of Materials (BOMs) has taken a quantum leap forward, thanks to the wonders of inventory management software. Let’s explore how this technology is changing the game:
Simplifying BOM creation
Gone are the days of manually drafting BOMs on paper or spreadsheets. Inventory management software allows for quick and easy creation of BOMs. It’s like having a smart assistant who helps you jot down the list and ensures it’s organized and error-free.
Real-time updates and version control
With traditional methods, keeping BOMs up-to-date was a Herculean task. Now, inventory management software enables real-time updates and version control. This means changes are instantly reflected and accessible to everyone involved, reducing the risk of using outdated information.
Integration and communication
Inventory software integrates seamlessly with QuickBooks, ensuring everyone works with the same updated information, enhancing communication and coordination.
Efficiency in tracking and ordering
Inventory software takes the guesswork out of tracking parts and components. It can automatically alert when stock levels are low and even assist in reordering, ensuring that production never hits a snag due to missing parts.
Cost analysis and reduction
By providing detailed insights into material usage and inventory levels, inventory software aids in cost analysis, helping companies identify areas where they can reduce expenses and cut waste.
Inventory management software has transformed BOMs from static lists into dynamic, interactive tools that boost efficiency, accuracy, and collaboration. It’s like having a high-tech command center at your fingertips, keeping the intricate machinery of manufacturing and engineering running smoothly and smartly.
Next, let’s tackle some of the challenges in BOM management and the innovative solutions to these hurdles.
Utilizing BOMs in Kitting and Assemblies
When we talk about BOMs, it’s not just about individual parts but also how these parts come together in kitting and assembly processes.
Understanding Kitting and Assembly
First, what are we talking about when we say “kitting’ and ‘assembly?” Kitting involves grouping individual items into a single kit and then treating them as a single item.
Assembly, on the other hand, refers to the process of combining various components to create a finished product.
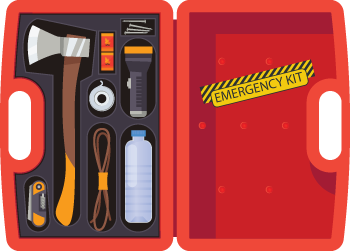
BOMs in Kitting
In kitting, BOMs list all the components that must be included in each kit. This is particularly useful in industries selling products in sets or kits, like electronics or DIY furniture. The BOM ensures that all necessary parts are included in the kit and helps in maintaining consistency across kits, ensuring each customer receives a complete set.
BOMs in Assembly operations

BOMs provide a detailed roadmap for assembly operations, showing how various components fit together to create the final product. The BOM details the sequence in which parts should be assembled, which is critical for complex products. The BOM also specifies the tools and techniques required for the assembly process, ensuring efficiency and quality control.
Inventory Management with Kitting and Assembly BOMs
Efficient inventory management is crucial in kitting and assembly. BOMs help track inventory levels of individual components, avoiding overstocking or shortages.
BOMs for kitting and assembly aren’t static; they must be flexible to accommodate custom orders or product variations. Inventory software solutions can dynamically adjust BOMs based on specific customer requirements or product customizations.
Quality control and error reduction
By providing clear instructions and lists, BOMs reduce the likelihood of errors during the kitting and assembly process, leading to higher-quality products and greater customer satisfaction.
In summary, BOMs are not just essential for listing parts; they are integral to the successful kitting and assembly of products, ensuring that every kit is complete and every assembly is done correctly. They help maintain quality, efficiency, and customer satisfaction in these complex processes.
Case Study: St. Jude Candle Company’s Transformation Through Effective BOM Management
Background
St. Jude Candle Company (SJCC), initially a small factory, experienced rapid growth, producing an average of 40,000 candles daily. This rapid expansion presented significant challenges in managing their production processes and inventory.
Initial Challenges
- Rapid growth management: In its early growth phase, SJCC needed help to keep up with demand. CFO David Wingard noted, “The first two years we were just trying to stay afloat and keep up with demand…transaction processing was suffering.”
- Manufacturing capabilities: Their initial financial management software lacked essential manufacturing capabilities, particularly in handling Bills of Materials (BOMs) and assembly transactions.
Solution: Acctivate Inventory Management Software
SJCC adopted Acctivate, an integrated solution enhancing their accounting software, specifically addressing BOM and assembly transaction needs.
- Enhanced manufacturing process: Acctivate’s discrete manufacturing (assembly) and custom manufacturing (kitting) features streamlined SJCC’s production.
- Reporting and data visualization: The software’s reporting capabilities provide real-time business intelligence, improving transaction process flow and data input efficiency.
- Improved production efficiency: Wingard remarked, “We have fine-tuned our production process…it goes smoother on the production end.”
- Better cost analysis: Acctivate allows for detailed cost analysis of BOMs, aiding in product review and decision-making for new products.
- Real-time reporting: Acctivate’s reporting tools enabled timely information delivery to essential stakeholders, including the bank for credit line requirements.
- Sustained growth: Nine months post-implementation, SJCC saw a 10.5% growth, with plans for facility expansion and increased production capacity.
- Scalability with technology: Plans to incorporate barcoding for enhanced production and inventory management, with Acctivate’s capability to support this future transition.
Conclusion
St. Jude Candle Company’s integration of Acctivate Inventory Management Software transformed their BOM and overall manufacturing process, turning their rapid growth into a manageable, efficient, and scalable operation. This strategic move streamlined their current operations and equipped them for future technological advancements and continued growth.
What is a BOM? FAQs
What is a Bill of Materials (BOM)?
A BOM is a comprehensive list that outlines all the components, materials, and instructions necessary to construct a product or assembly. The BOM serves as an essential blueprint for manufacturing and is crucial in ensuring accuracy and efficiency in the production process.
Why is accurate BOM management important for manufacturing companies?
Accurate BOM management ensures that all necessary components are available for production, helps estimate costs, maintains quality control, and streamlines the manufacturing process. Inaccuracies in BOM can lead to production delays, increased costs, and quality issues.
Can BOMs be used for complex products with multiple sub-assemblies?
Yes, BOMs are designed to handle complex products with multiple sub-assemblies. They detail each component at every level of the assembly process, ensuring that even the most intricate products can be efficiently manufactured.
How has technology, like inventory management software, transformed BOM management?
Technology, particularly inventory management software, has revolutionized BOM management by automating data entry, facilitating real-time updates, enhancing collaboration across departments, and improving supply chain management, leading to increased accuracy, efficiency, and cost-effectiveness in manufacturing processes.
Call us at 817-870-1311