Built For
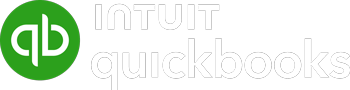
Acctivate Blog
Business best practices
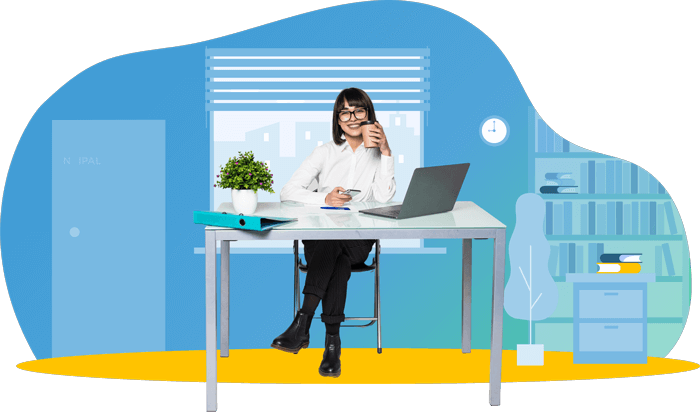
Featured Articles
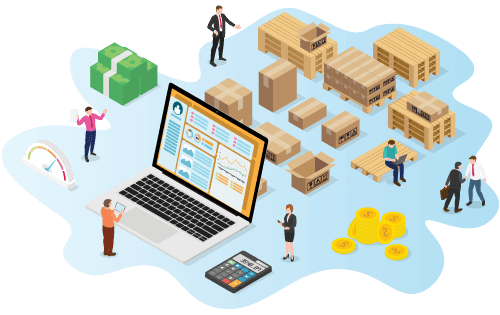
7 Inventory Strategies
Let’s dive into some of the most effective inventory strategies that can help your business operate smoothly, save money, and keep your customers smiling.
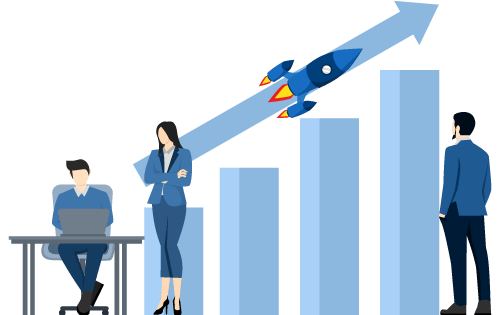
Software to Scale Your Business
Let’s explore how inventory and order management software can help take your business to the next level and make growth a lot smoother.
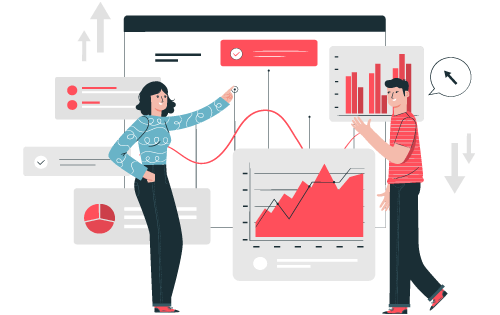
Driving Operational Growth with Inventory and Order Management Software
We’ll explore how inventory and order management software drives operational growth by improving efficiency, enhancing inventory control, boosting order fulfillment speed, and supporting expansion.
Forecasting and Demand Planning Made Easy with Inventory Software
Struggling with stockouts or excess inventory? Matt Allen of Acctivate Inventory Software, shares how inventory software simplifies forecasting and demand planning for a smoother…
From Warehouse to Customer: Mastering Efficient Distribution
Mastering efficient distribution ensures that your products move seamlessly from warehouse to customer, minimizing costs while maximizing speed and accuracy.
Business Growing Pains? Inventory Software Can Help You Scale Smoothly
We’ll explore typical business growing pains and how inventory software can help you scale smoothly without losing control.
Building a Successful Inventory Business
Running an inventory business can be rewarding, but it requires careful planning, organization, and the right tools to succeed.
Multi-location Inventory Management Simplified
Let’s break down how multi-location inventory management can be simplified with smart strategies and the right tools.
Scale Efficiently and Maintain Quality as You Grow
Today, we explore how businesses can scale efficiently without sacrificing the quality that built their reputation
Find Out More!
Learn more about Acctivate Inventory Software by connecting with our product experts.
Call us at 817-870-1311