Optimizing a Bakery Distribution System
Built For
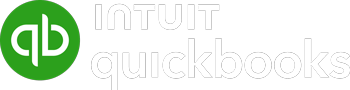
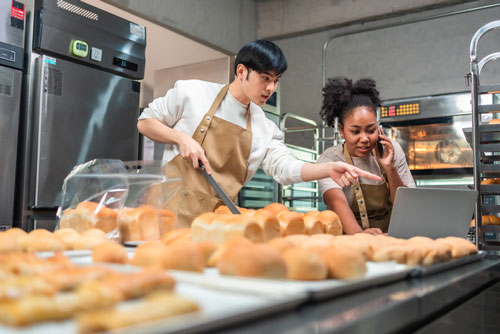
What is a bakery distribution system?
A bakery distribution system serves as the backbone of the wholesale bakery business, ensuring that freshly baked goods reach distributors, retailers, and consumers in a timely and efficient manner. From sourcing raw materials to delivering finished goods, a bakery distribution system encompasses a range of activities, connecting the bakery with its various stakeholders.
For wholesale bakeries, the distribution system is a critical component of their operations, involving purchasing, inventory management, order processing, packaging, storage, and distribution. In the past, these activities were primarily manual, relying heavily on human judgment, spreadsheets, and reminder notes. However, technological advancements have shifted the focus toward leveraging software solutions for optimized, real-time decision-making and streamlined operations.
Given the perishable nature of bakery products and the need to maintain quality while complying with food safety regulations, an efficient distribution system is more than a luxury—it’s a necessity. Therefore, understanding software’s role in modernizing this system is essential for bakery owners looking to scale their operations, improve efficiency, and meet customer expectations.
Exploring the components of a bakery distribution system
In this article, we’ll explore the various challenges involved in bakery distribution and how a software solution revolutionizes the way wholesale bakeries manage their businesses, including:
- Purchasing: Sourcing raw materials, forecasting demand, and managing suppliers
- Process Manufacturing: Variable recipe and yield capabilities
- Inventory Management, Packaging, and Storage Order Management: Versatility in sales orders and fulfillment
- Distribution and Tracking: Direct store delivery and route management
- Traceability
- QuickBooks integration
Purchasing: Sourcing raw materials, forecasting demand, and managing suppliers
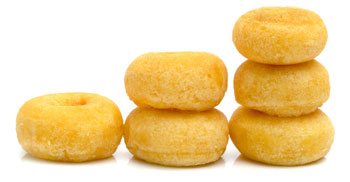
One of the initial steps in the bakery distribution system is purchasing, which involves sourcing high-quality raw materials and accurately forecasting demand to ensure sufficient stock levels. A bakery distribution system automates these processes by analyzing historical data to forecast demand, enabling wholesale bakeries to make data-driven decisions on what to buy and when eliminating the risks associated with over-purchasing and stock spoilage. Additionally, an often-overlooked aspect of purchasing is supplier management. It is crucial to know where raw materials come from and ensure they meet quality and sustainability standards. A bakery distribution system assists with tracking and evaluating supplier performance, managing contracts, and providing reordering alerts based on pre-determined thresholds. These capabilities help maintain a high level of product quality and foster solid and reliable relationships with suppliers, which can be invaluable in supply chain disruptions.
Additionally, an often-overlooked aspect of purchasing is supplier management. It is crucial to know where raw materials come from and ensure they meet quality standards. A bakery distribution system assists with tracking and evaluating supplier performance, managing contracts, and providing reordering alerts based on pre-determined thresholds. These capabilities help maintain a high level of product quality and foster solid and reliable relationships with suppliers, which can be invaluable in supply chain disruptions.
Process Manufacturing: Variable recipe and yield capabilities
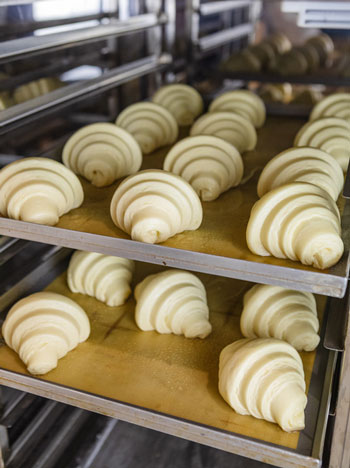
The wholesale bakery industry presents a unique set of challenges regarding production. Unlike other types of manufacturing, where the same product is created uniformly, wholesale bakeries often deal with a myriad of recipes that can change based on seasonal availability of ingredients, customer preferences, or even promotional events. This variability extends to the yields, where the quantity of end product can differ depending on various factors like ingredient quality, environmental conditions, and human expertise.
Tracking raw material variations
One of the first steps in managing this complexity is accurately tracking variations in raw materials. A bakery distribution system with process manufacturing tools keeps meticulous records of each batch of raw materials, including quality indicators, sources, and storage conditions, which is especially critical when working with natural ingredients that may have variations in flavor, texture, or moisture content. By doing so, bakeries can adjust recipes accordingly to maintain product consistency.
Calculating optimal yields
Calculating optimal yields is another challenge faced by bakeries. Bakery distribution software uses historical data and real-time input to calculate the most efficient use of ingredients, thereby maximizing yield without sacrificing quality, helping wholesale bakeries cost-effectively by minimizing waste and optimizing raw materials.
Scaling recipes
Scaling recipes is an everyday activity in the wholesale bakery industry, where a recipe for a dozen might need to be multiplied to produce hundreds or thousands. A bakery distribution system automates this scaling process to ensure the final product remains consistent.
Ensuring consistency and efficiency
Consistency is a significant concern with the complexities of variable recipes and yields. A robust bakery distribution system helps manage these variables in a streamlined manner. Real-time data collection and analytics allow bakeries to monitor quality and make immediate adjustments. Moreover, automating these processes contributes to operational efficiency, enabling bakeries to fulfill large orders without compromising quality.
Inventory Management, Packaging, and Storage
Given the perishable nature of bakery products, inventory management, packaging, and storage are crucial elements of the distribution system. A bakery distribution system monitors stock levels in real-time, suggesting optimal packaging methods and setting alerts for temperature or storage conditions, reducing waste, and ensuring products are stored and handled in compliance with food safety regulations.
Order Management: Versatility in sales orders and fulfillment
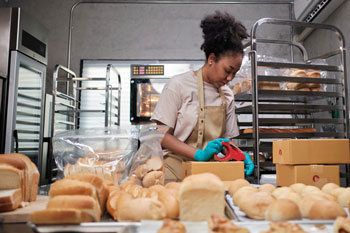
Modern bakery operations face a complex landscape regarding order management, given the many options customers now expect. From full or partial case deliveries to blanket orders, previous order duplication, and Electronic Data Interchange (EDI), a versatile and robust order management system has never been more pressing.
Full or partial case deliveries
Bakeries often have to deal with variable order sizes, ranging from full cases for larger clients like grocery stores to partial cases for smaller retail locations or special events. The order management capabilities of a bakery distribution system allow bakeries to easily adjust order specifications, ensuring precise quantities are prepared and delivered, thus minimizing waste and maximizing customer satisfaction.
Blanket orders
Sometimes, customers place blanket orders that span multiple delivery dates. Managing such orders manually can be cumbersome and prone to errors. With a bakery distribution system, these blanket orders are automated, providing reminders for upcoming deliveries and enabling easy adjustments in case of changes in customer needs.
Previous order duplication
Repeat business is a cornerstone of the wholesale bakery industry. The ability to duplicate previous orders with just a click saves both the bakery and the customer considerable time and is especially useful for businesses that place consistent, recurring orders.
Electronic data interchange (EDI)
EDI is increasingly becoming a standard requirement, particularly for wholesale bakeries that deal with larger retailers or supply chains. EDI, used in conjunction with a bakery distribution system, allows for automated, real-time exchange and management of orders, invoices, and other essential documents between bakeries and customers, dramatically speeding up order processing times and reducing manual errors.
Distribution and Tracking: Direct store delivery and route management
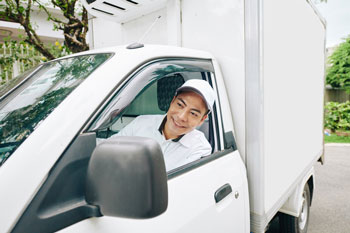
Efficient distribution and tracking are vital for a successful bakery distribution system. A bakery distribution system’s advanced features, such as direct store delivery and optimized route management, allow quicker and more accurate deliveries. With real-time tracking, the bakery and customers are kept in the loop, improving customer satisfaction and enabling better decision-making.
Traceability
Traceability is an indispensable feature of a modern bakery distribution system. By leveraging the bakery distribution system’s lot tracking, bakeries ensure product safety, simplify compliance and build stronger, trust-based relationships with consumers and stakeholders.
Real-time tracking of products
Bakery distribution software solutions include real-time tracking capabilities. From the moment raw materials arrive at the facility to when the finished goods are delivered to the customer, every step is meticulously recorded and monitored, providing a transparent supply chain that allows bakeries to verify the quality and safety of their products at any stage of production.
Managing recalls effectively
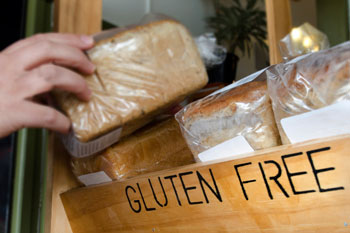
Despite the best safety measures, product recalls are an unfortunate reality in the food industry. In such events, traceability software proves invaluable, allowing bakeries to quickly identify the batch or batches of products affected and track down their distribution points. This rapid response meets regulatory requirements and protects the brand’s reputation by demonstrating a commitment to consumer safety.
Tracing quality issues to their source
If quality issues arise—be it a change in taste, texture, or shelf life—the traceability features of a bakery distribution system help identify the root cause. Whether the problem stems from a particular batch of raw materials, a step in the production process, or even a storage condition, pinpointing the source is made easier, enabling the bakery to implement corrective measures swiftly minimizing any negative impact on the business.
Enhanced compliance reporting
Finally, robust traceability features in the bakery distribution system make it easier for bakeries to comply with local, state, and federal regulations. Compliance reports can quickly be generated, providing auditors with the necessary information in a readily accessible format, simplifying the auditing process, helping bakeries proactively manage compliance, avoiding penalties, and maintaining good standing with regulatory agencies.
QuickBooks Integration
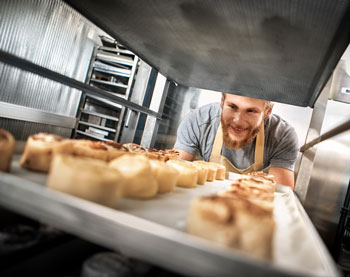
QuickBooks is the accounting software used by most small to medium-sized wholesale bakeries. The ability to integrate bakery distribution software with QuickBooks significantly streamlines financial processes and ensures seamless data flow between systems, making it possible to gain the purchasing, batch process, traceability, and inventory, packaging, storage, order, and distribution management capabilities they require – without leaving QuickBooks.
Call us at 817-870-1311