Inventory management challenges and solutions
Built For
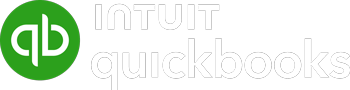
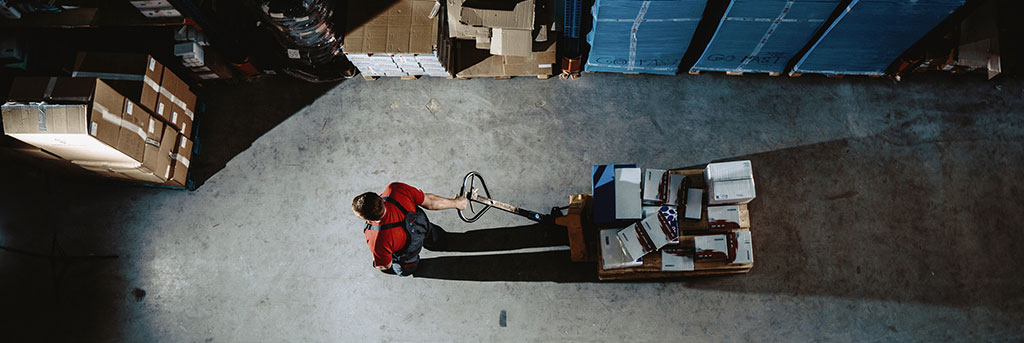
Inventory management challenges and solutions- a moving target
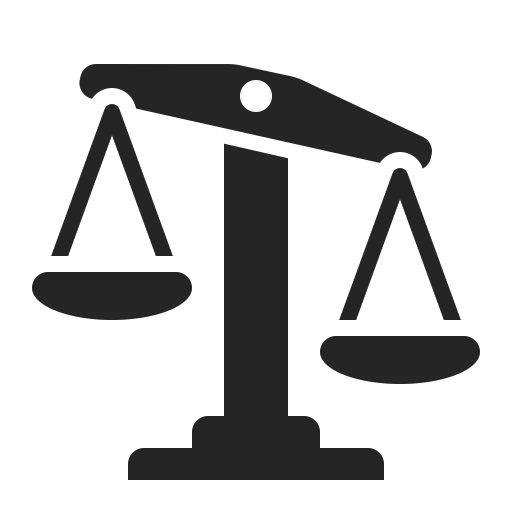
There’s too much inventory…
There’s too little inventory…
It can be a tricky task getting inventory control just right. In fact, even large retailers struggle to find a balance between carrying excess inventory and out-of-stocks.
Inventory management challenges and solutions, an emerging struggle in inventory control
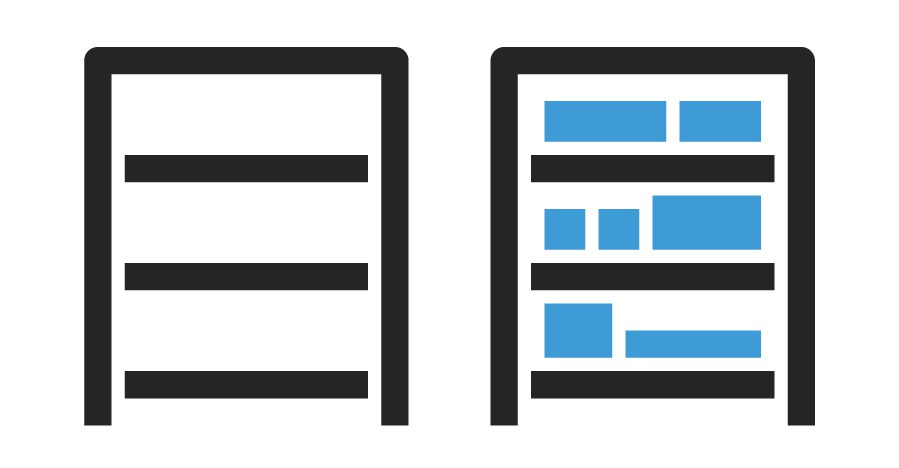
Recently, Walmart put their focus on inventory optimization. This was in response to inventory growing at a faster rate than sales for the multi-billion dollar retail chain — resulting in a steady accumulation of inventory.
Conversely, the number two retailer Target took initiative to reduce the number of out-of-stocks occurring. Though inventory rates slightly outpaced sales, Target’s dedicated efforts led to “record in-stock levels”, which has led to better order fulfillment rates and higher customer satisfaction for the mega-retailer.
What has led to such a drastic range of inventory effects for Walmart and Target? In addition to the volatility in consumer demand and uncertainties in the supply chain that have always been around, eCommerce has further exacerbated inventory complications.
Walmart and Target aren’t the only businesses struggling to find the right balance of inventory — most businesses have been impacted by the brick-and-mortar and online shopping supply chain dilemma.
A recent Wall Street Journal logistics report explained that…
Many brick-and-mortar retailers are trying to figure out the right balance of inventory on store shelves for walk-in customers and in warehouses to meet highly-volatile online demand. Although moving inventory up the supply chain and into distribution centers can reduce redundant inventory, it can leave stores low on stock and cost sales. Fulfilling orders out of stores can further complicate the equation.”
Finding solutions to inventory management challenges
So how did Walmart and Target effectively reach their inventory control goals?
To reduce the amount of excess inventory that was accruing (while also avoiding an increase in out-of-stocks), Walmart revealed that the company utilized technology and implemented more efficient supply chain processes.
Target created “out-of-stock action teams” to set standards for levels of safety stock and inventory allocated for distribution centers, as well as utilizing technology for supply chain optimization.
Though the challenges and goals for both retailers were different, the common denominator for both retailers was the use of technology to improve inventory control.
Fortunately, technology exists to help small businesses attain better inventory control. Major office supply retailer Staples explains in an article on business logistics that…
As small businesses move into virtual and dual retail models, keeping up with product status and movement can be difficult…
As inventories, supply chains, and order fulfillments become increasingly complex, merging traditional inventory management tools with automated data entry can help reduce errors that result in costly overstock, backorders, refunds, and customer service issues.”
Inventory management challenges and solutions faced by businesses of all sizes
Inventory management poses challenges for businesses of all sizes, requiring effective solutions to ensure streamlined operations. As illustrated above, one of the main difficulties is maintaining an optimal balance between supply and demand. Overstocking leads to increased holding costs and the risk of product obsolescence, while understocking can result in stockouts and dissatisfied customers. Moreover, accurately forecasting demand proves challenging due to market fluctuations and unexpected events. Inventory theft and shrinkage also pose significant financial losses. To address these issues, businesses implement inventory management software and data analytics tools to improve demand forecasting accuracy and help minimize excess stock while maintaining smooth production and delivery.
Utilizing technology for small business inventory control
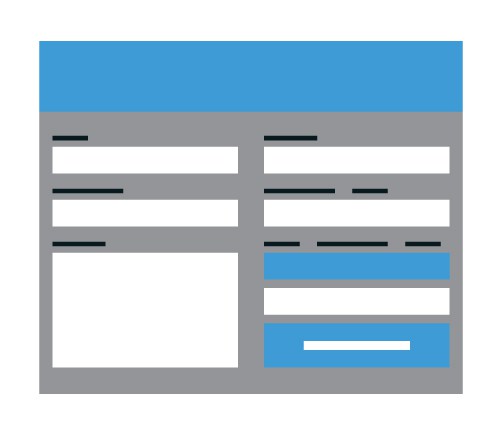
Software is a great way to utilize technology to aid in small business inventory control. The use of inventory control software provides automation of data entry in areas such as:
- Receiving inventory
- Relocating inventory
- Preparing items for order
- Shipping inventory
Additionally, inventory control software provides accurate, real-time inventory levels for maximum control.
Here are some examples of instances where having accurate inventory levels are usually challenging for businesses:
- Having multiple warehouses, distribution centers, or retail locations
- Having a web store and physical locations
- Having backordered or drop-shipped orders
However, inventory control software is able to keep track of inventory in instances that normally prove challenging when managed manually, even when multiple locations, web stores, and backordered or drop-shipped items are involved.
Depending on the specific solution, inventory control software benefits are numerous. This is especially helpful for small businesses, where the manpower required for managing and overseeing manual processes is not abundantly available. For instance, Acctivate inventory control software is able to ensure that a dedicated amount of safety stock is available for your business through the use of Reorder Alerts.
Reorder Alerts in Acctivate will inform the user(s) of when the minimum inventory level for a specific product has been reached. Acctivate will even make reordering the product as easy as one click if a purchasing preset has already been established for that specific product. This is because Acctivate consolidates inventory with purchasing and sales, providing each business insight and the capabilities to efficiently manage supply chain flow.
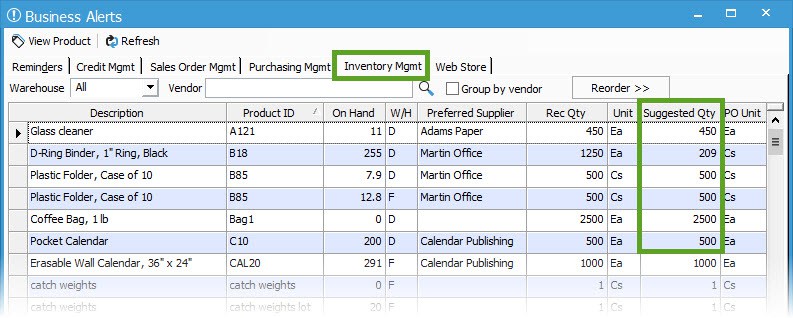
Thus, small business inventory control is optimized and maximized with inventory control software.
For more on small business inventory control, check out our inventory control fact page here
Acctivate — affordable, powerful software for small business inventory control
Acctivate provides inventory control software for small businesses that’s powerful, easy to use, and affordable. Small businesses of all industries trust Acctivate for effective and efficient inventory control. The great part about Acctivate inventory control software is its ability to scale for your business’ growth — Acctivate will grow with your business, not against it.
Call us at 817-870-1311